Rotary shaft seals, often dubbed the unsung heroes of mechanical systems, serve pivotal roles in various industrial applications. Their primary function is to retain lubricants, exclude contaminants, and maintain fluid separation in systems where shafts rotate in housings. While these seals might seem like inconspicuous components, their impact on the overall performance, efficiency, and longevity of machinery is monumental.
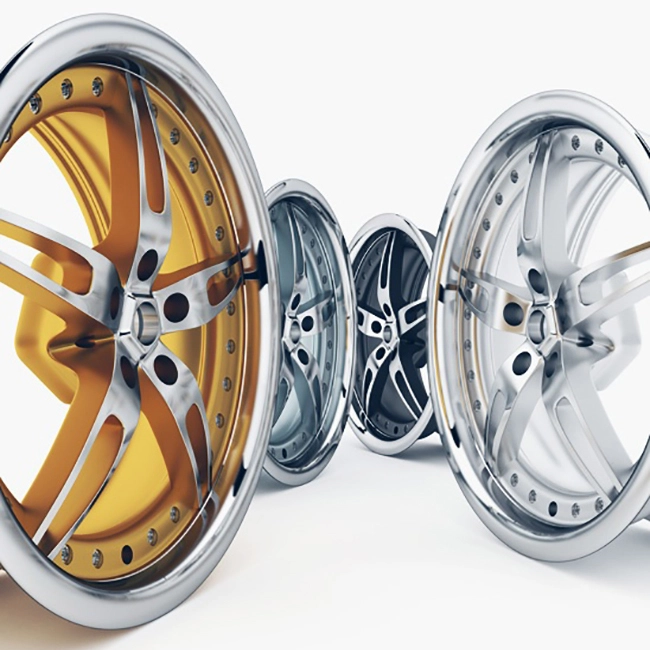
Consider the example of a manufacturing plant where rotary shaft seals are employed in conveyor belt systems. As conveyors operate, minimizing friction between the rotating shaft and the stationary housing is crucial to avoid overheating and premature wear. A high-quality rotary shaft seal can significantly extend the lifecycle of the system, saving substantial costs in maintenance and downtime.
Professional manufacturers invest heavily in research and development to produce advanced rotary shaft seals tailored to meet diverse industrial needs. These seals are constructed from a variety of materials, such as nitrile rubber, Viton, and PTFE, each chosen based on the specific application and environmental conditions. For instance, seals used in food processing must adhere to stringent hygiene standards and are often made from FDA-approved materials.
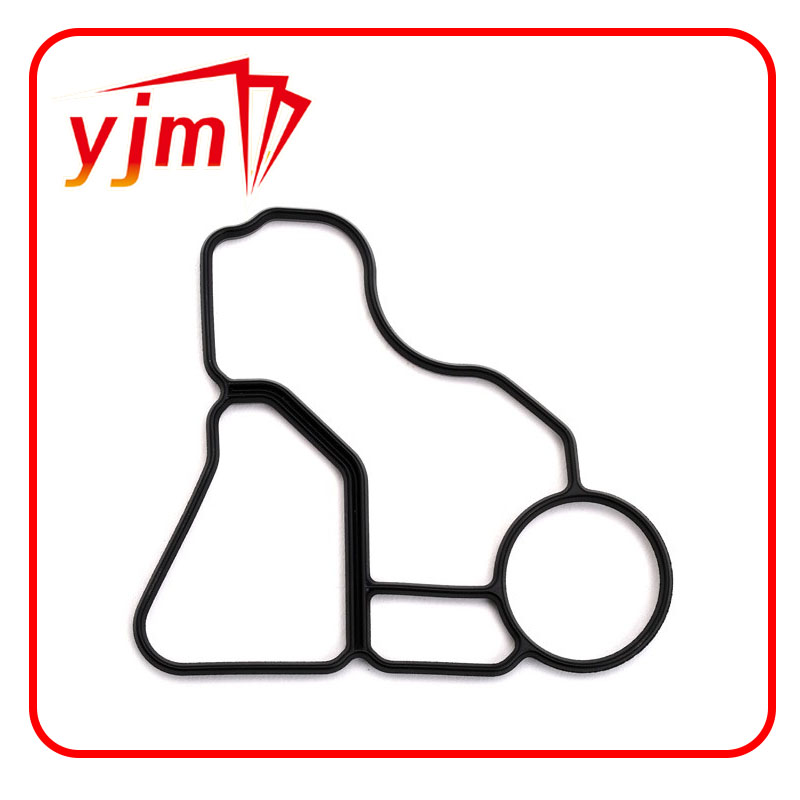
The expertise behind designing these seals lies in understanding the myriad of challenges posed by different applications. Engineers must account for factors such as pressure, temperature, speed, and the type of lubricants or fluids present. The choice of lip design is critical as well; whether it's a single lip for less demanding applications or a dual lip for added protection against contaminants, each design offers unique benefits and is selected after meticulous analysis.
One real-world scenario underscoring the importance of rotary shaft seals is their use in the automotive industry. Vehicles rely on these seals to prevent oil leakage in engines and transmissions. An ineffective seal can lead to significant engine problems or even complete failure, underscoring how essential it is to invest in high-quality seals. Automotive engineers collaborate with seal manufacturers to develop custom solutions that can withstand the high temperatures and pressures found in modern engines, while also providing longevity and reliability.
rotary shaft seals
In aerospace applications, rotary shaft seals must contend with extreme conditions such as high altitudes and temperatures. They are meticulously tested for resilience and endurance, as failure is not an option in this critical field. The aerospace industry exemplifies the necessity of trustworthiness and authoritativeness, where product tests and certifications must be thorough and impeccable to ensure passenger safety.
Despite their small size, rotary shaft seals are pivotal to sustainable industrial operations. As industries pursue more energy-efficient and eco-friendly solutions, the role of these seals is more prominent than ever. They help in reducing energy consumption by minimizing fluid and air leakages in systems, which consequently decreases the workload on the machinery. Furthermore, innovative sealing technologies and materials are being developed to align with the global push toward sustainability, creating seals that last longer and perform better, reducing waste and the demand for frequent replacements.
Selecting the appropriate rotary shaft seal is not merely about matching specifications. It requires a deep understanding of the entire system's architecture and the operational stresses it will face. Companies often rely on the knowledge and experience of dedicated engineers and specialists who provide consultation and service support, confirming that the chosen seals will meet or exceed the application's demands.
As industries continue to evolve, so does the technology behind rotary shaft seals, making them indispensable components in ensuring reliability and efficiency across sectors. The commitment to excellence and advancements in seal technology reinforce their critical role in machinery, underlining their worth as trusted components in sophisticated and demanding environments. Users and engineers must continue to stay informed about the latest developments in seal technology to leverage their full potential and maintain the competitive edge in their respective industries.