Shaft seals are integral components in a variety of machinery, serving as the gatekeepers between moving parts and the surrounding environment. Their primary function is to prevent leakage of fluids along a rotating or reciprocating shaft, thereby maintaining the efficiency and safety of the equipment. In industries ranging from automotive to aerospace, the reliability and performance of shaft seals can significantly impact operational success.
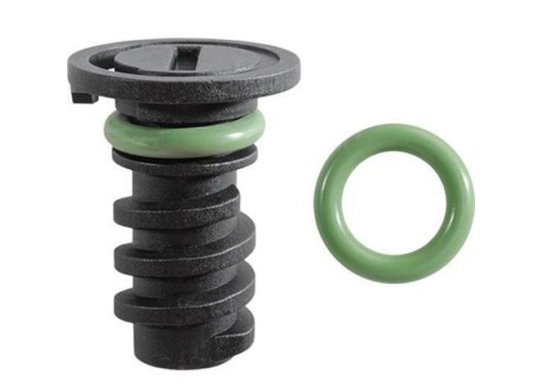
To optimize your understanding of shaft seals, it’s essential to delve into their types, materials, applications, and selection criteria. Shaft seals come in various designs such as lip seals, labyrinth seals, and mechanical seals, each suited for specific applications based on their operational needs. Lip seals are typically used for their simplicity and effectiveness in preventing fluid leakage in low-pressure applications. Labyrinth seals, on the other hand, are often employed in high-speed applications due to their non-contact design, which minimizes friction and wear. Mechanical seals provide an advanced solution for high-pressure and high-temperature environments, ensuring robust sealing under demanding conditions.
The choice of material plays a crucial role in the performance of shaft seals. Materials like nitrile, Viton, and silicone are common due to their resistance to various fluids and temperature ranges. Nitrile rubber is highly resistant to petroleum-based oils and fuels, making it ideal for many automotive applications. Viton offers superior chemical resistance and can withstand higher temperatures, making it a preferred choice in chemical processing industries. Silicone seals, known for their excellent thermal stability, are used in applications where extreme temperature variations occur.
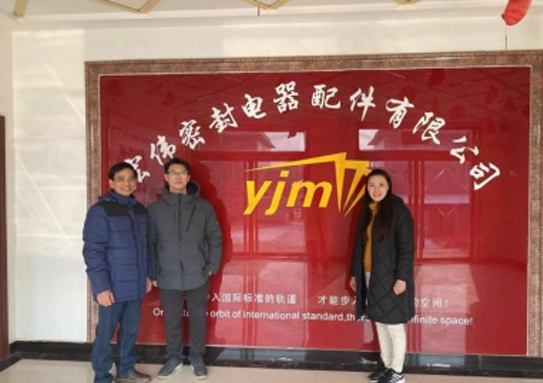
When selecting a shaft seal, it’s imperative to consider several factors the nature of the fluid being sealed, operating temperature, pressure levels, shaft speed, and environmental conditions such as exposure to dust or moisture.
Understanding these operational parameters ensures that the chosen seal provides optimal performance and longevity. For instance, in high-speed applications, seal designs that minimize frictional forces are recommended to prolong seal life and maintain efficiency.
shaft seal
The installation process also affects the performance of shaft seals. Proper alignment and handling are crucial, as misalignment can lead to premature wear or failure. Ensuring that the shaft is smooth and free of burrs or sharp edges will help in extending the seal’s lifespan and effectiveness. Furthermore, maintenance practices such as regular inspection and lubrication are vital in preserving the integrity of the seal over time, particularly in environments with high wear and tear.
For professionals seeking reliable, high-performance solutions, engaging with trusted manufacturers and suppliers of shaft seals can provide unparalleled insights and product availability. Leading companies often offer specialized engineering support to assist in designing and selecting the most appropriate seal for specific requirements. Their expertise ensures that customers receive a tailored solution that aligns with technological advancements and industry standards.
With the continuous evolution of technology, innovations in material science and engineering are paving the way for more efficient and durable shaft seal designs. Future trends indicate a shift towards self-lubricating seals that reduce maintenance requirements and extend operational lifespans. These advanced seals help in reducing downtime and improving overall cost-efficiency for businesses.
In conclusion, shaft seals are indispensable components that guarantee the seamless operation of machinery across diverse sectors. By integrating expert knowledge, innovative technology, and best practices in maintenance, businesses can significantly enhance their equipment’s durability and performance. Investing in the right shaft seal solutions not only safeguards machinery but also optimizes operational efficiency, reflecting positively on the bottom line. Engaging with industry experts and keeping abreast of technological advancements ensures that businesses remain at the forefront of innovation in their respective domains.