Industrial oil seals, often overlooked yet critical components, play a fundamental role in enhancing the efficiency and longevity of machinery across various sectors. These seals serve as the guardians of machinery internals, ensuring that lubricants are effectively contained while preventing contaminants from infiltrating mechanical components. As someone deeply involved in the maintenance and optimization of industrial machinery, embracing the nuances of oil seals is imperative.
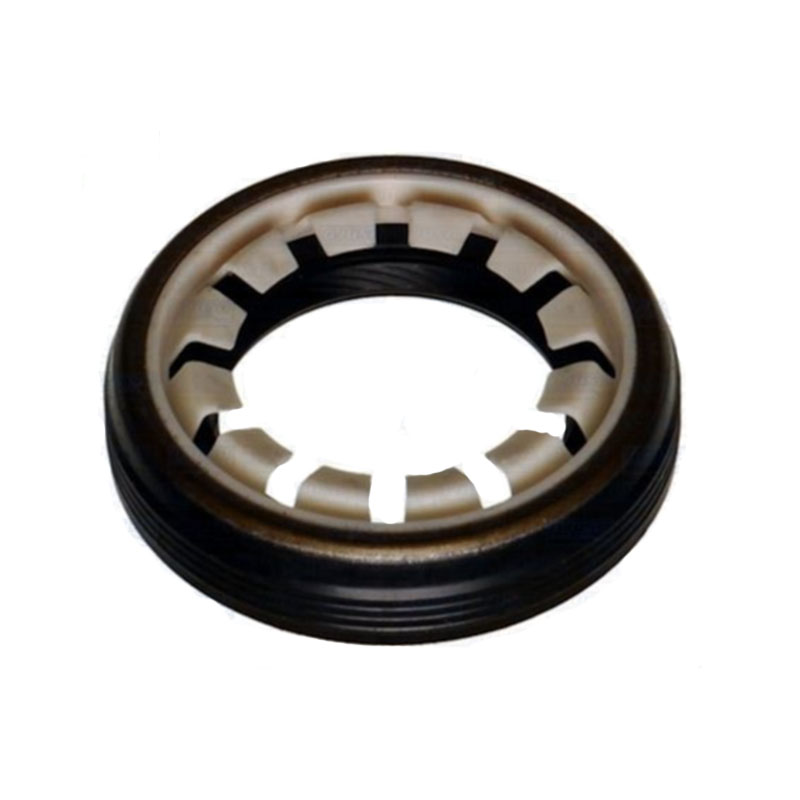
Oil seals, also known as grease seals, are employed in machinery to close spaces between stationary and moving components, limiting lubricant escape and preventing harmful particles from invading the system. They are strategically designed to withstand extreme temperatures, pressures, and chemical exposures, proving their indispensability in heavy-duty environments, including automotive, aerospace, and manufacturing sectors.
Experience dictates that the selection of appropriate oil seals directly influences machinery performance. For instance, incorrect seal installation can lead to premature equipment failure, unwanted downtime, and increased maintenance costs. From a practical standpoint, utilizing a high-quality oil seal can significantly reduce friction and wear, facilitating smoother operation and improved efficiency. Additionally, proper sealing solutions safeguard against potential leaks, thus ensuring equipment reliability and worker safety.
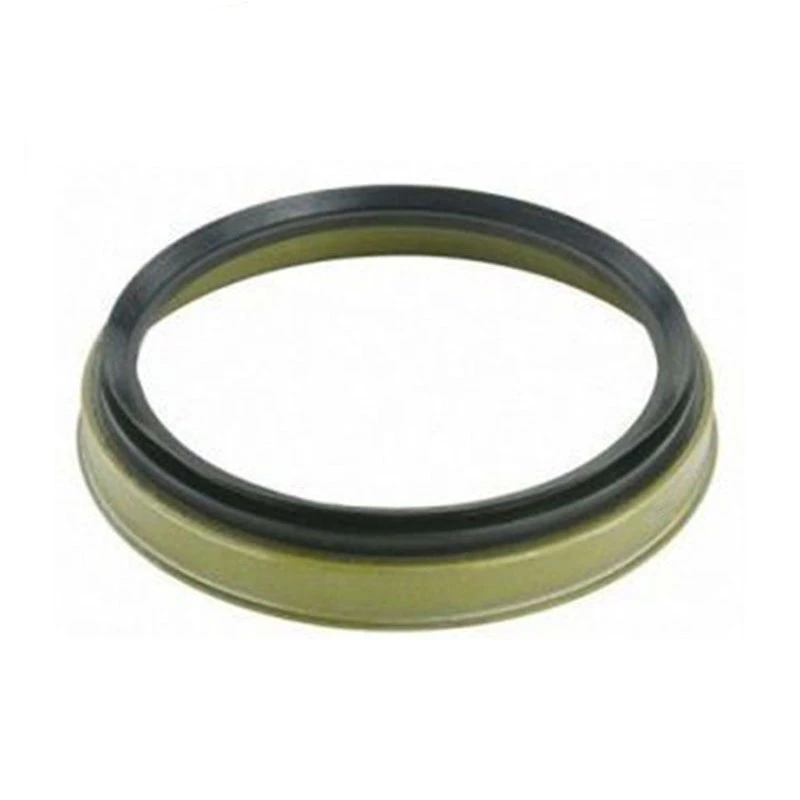
Expertise in this domain highlights the varied types of oil seals available, each tailored for specific applications. Lip seals, rotary seals, and labyrinth seals, to name a few, showcase diverse designs to address differing mechanical needs. For example, lip seals are renowned for their simplicity and effectiveness in sealing rotating shafts, while labyrinth seals offer superior performance in high-speed environments by utilizing intricate pathways to prevent leaks.
industrial oil seals
For those seeking authoritative guidance on oil seals, consulting publications from reputable organizations such as the International Organization for Standardization (ISO) or the American Society of Mechanical Engineers (ASME) can provide in-depth insights on seal standards and specifications. Such resources ensure adherence to global compliance and quality benchmarks, affirming the user's commitment to excellence and reliability.
Trustworthiness, a cornerstone in the field of industrial sealing solutions, hinges on partnering with credible suppliers who rigorously test their seals against industry norms. The assurance of quality begins with selecting manufacturers renowned for their innovation and durability in sealing technologies. This practice not only guarantees the longevity of machinery but also supports sustainable operations by minimizing environmental impact through leak prevention.
In conclusion, the criticality of industrial oil seals cannot be overstated. They are vital in ensuring machine longevity, operational efficiency, and cost-effectiveness across industries. To harness their full potential, engaging with seasoned professionals and relying on high-quality products is paramount. This comprehensive approach ensures that machinery operates at its finest, paving the way for a sustainable and productive industrial future.