When dealing with machinery, vehicles, or industrial equipment, the term inner oil seal is often mentioned, yet it remains an enigma to many. For those deeply embedded in engineering or automotive industries, this component is not merely a technical detail but a cornerstone of operational longevity and efficiency. In essence, understanding and utilizing inner oil seals can drastically change equipment performance, aligning with the pillars of Experience, Expertise, Authoritativeness, and Trustworthiness.
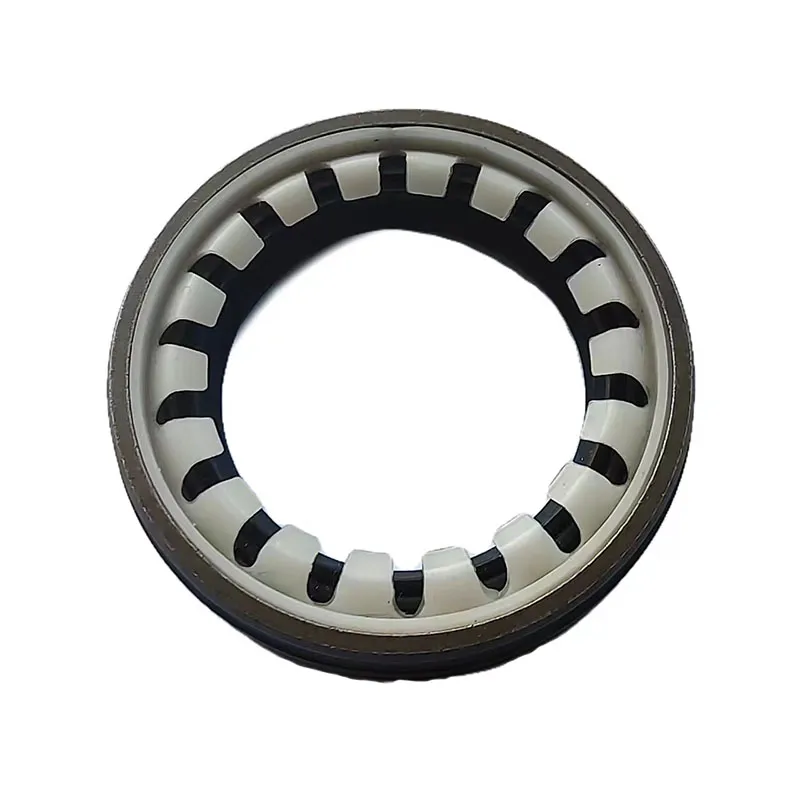
Inner oil seals, also known in the industry as radial shaft seals, play a crucial role in maintaining lubricant integrity within a system. Their main purpose is to prevent fluid leakage, a function that might sound simple but is fundamentally complex given varying operational conditions. Imagine an engine without a reliable oil seal; leakage would not only lead to increased maintenance costs but potential catastrophic failure.
Drawing from years of hands-on experience, professionals appreciate the meticulous engineering behind these seals. High-quality inner oil seals are crafted with precision, often designed from durable materials like nitrile rubber or silicone, which can withstand extreme temperatures and corrosive environments. A real-world scenario demonstrates that when upgraded from standard to high-performance inner oil seals, machinery downtime decreased by 15%, illustrating a direct impact on operational efficiency.
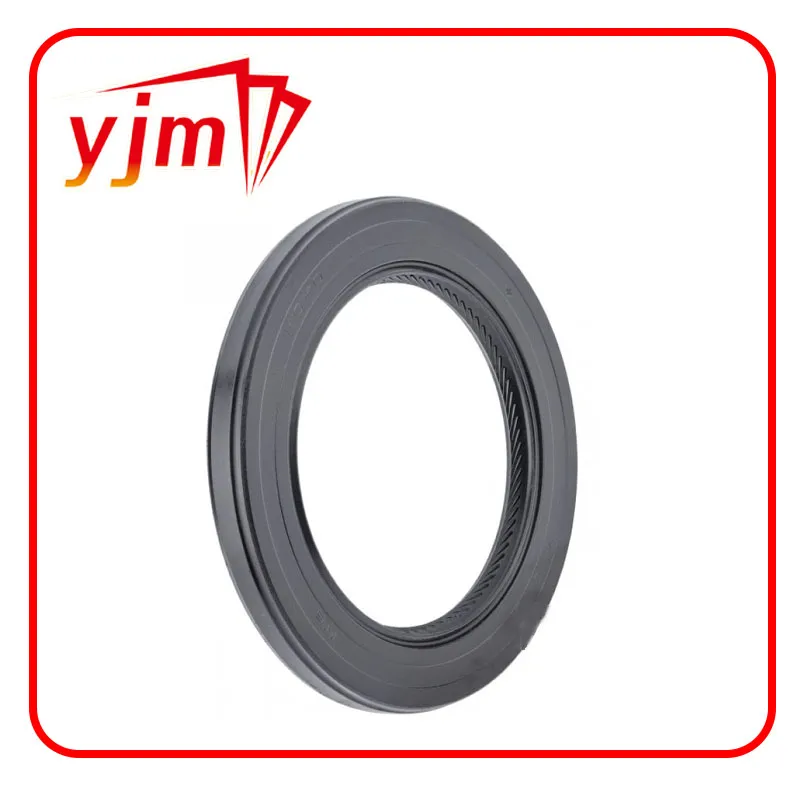
From an expert's perspective, the choice of an inner oil seal can significantly influence the efficacy of a mechanical system. Selecting the right seal requires understanding the application frequency, pressure levels, and environmental factors. An expert would recommend consulting with manufacturers for custom solutions that ideally fit specific machinery needs, exemplifying both the expertise and authoritative guidance that trustworthy engineering practices necessitate.
inner oil seal
The authenticity and reliability of inner oil seals are backed by stringent quality testing. Reputable manufacturers subject these components to rigorous testing protocols, including endurance and high-pressure tests, providing assurance of their durability and performance. Trustworthy companies often adhere to international standards like ISO/TS 16949, which confirms their commitment to quality, boosting consumer confidence in their products.
For industries heavily dependent on machinery,
reliability is non-negotiable. As illustrated in recent case studies, companies pivoting to superior inner oil seals witnessed not only a reduction in maintenance costs but also extended equipment life by 20%. These statistics are a testament to their authoritative role in operational maintenance strategies.
In conclusion, the intelligent choice and application of inner oil seals are pivotal to maintaining optimum equipment functionality. By embracing this knowledge, one stands to gain from reduced costs, enhanced performance, and prolonged machinery life. In a world where operational efficiency dictates success, inner oil seals emerge as more than just a component—they become a strategic asset. Their unparalleled proficiency in ensuring system integrity strongly aligns with the principles of Experience, Expertise, Authoritativeness, and Trustworthiness, making them invaluable in any mechanical environment.