Understanding Hydrogenated Nitrile O-Ring The Ultimate Guide for Industrial Applications
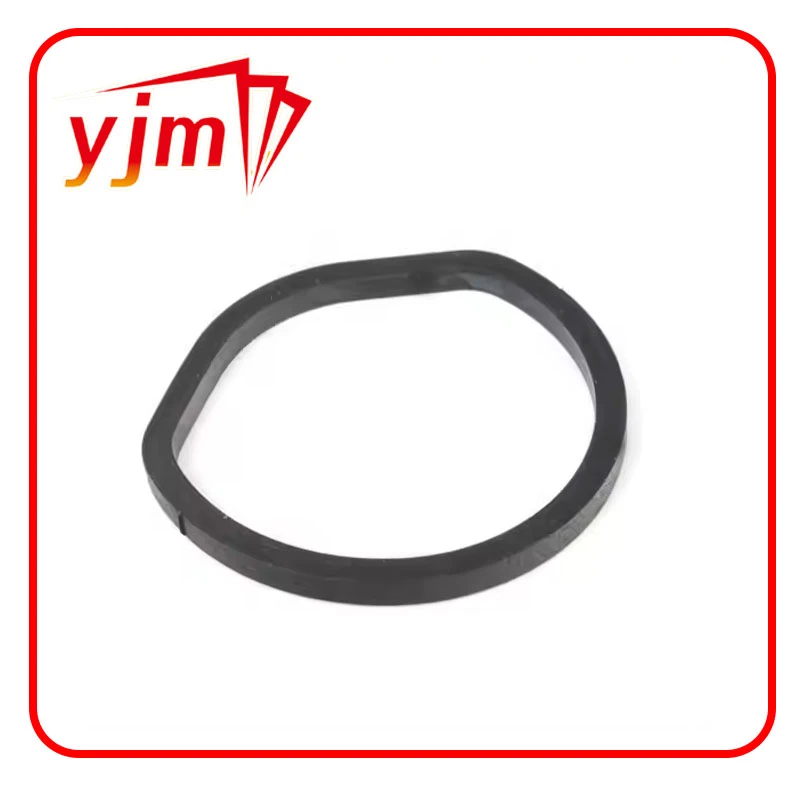
Hydrogenated Nitrile Butadiene Rubber (HNBR) has emerged as a standout material in industries requiring superior performance in extreme environments. HNBR O-rings are well-regarded for their exceptional resistance to various harsh conditions, making them indispensable in both heavy machinery and precision engineering.
Real-world Experience Why Industries Trust HNBR O-Rings
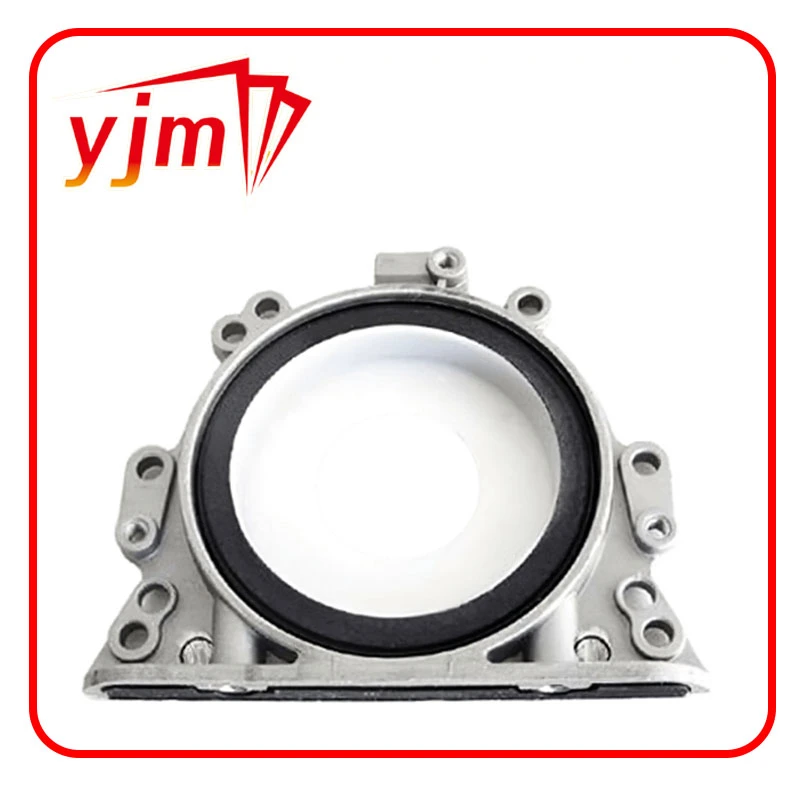
In oil and gas sectors, where equipment is regularly subjected to extreme temperatures and volatile chemicals, HNBR O-rings have proven their reliability. An oil rig operator shared that their move to HNBR significantly reduced unscheduled downtimes, as these O-rings demonstrated admirable wear and tear resistance in subterranean drilling.
Automobile manufacturers also witness improved durability when employing hydrogenated nitrile O-rings. Under-the-hood components, including engine gaskets and transmissions, withstand high heat and aggressive oils without significant degradation, extending service intervals and reducing maintenance costs.
Expertise in Composition The Chemistry Behind the Resilience
The hydrogenation process in HNBR transforms the butadiene component, enhancing the material's strength and thermal stability. This transformation imparts HNBR O-rings with superior abrasion resistance and outstanding mechanical properties over traditional nitrile rubber. The material’s ability to manage temperatures between -40°C to +150°C and resist chemical degradation makes it suited for arduous conditions.
hydrogenated nitrile o ring
Authoritativeness in Manufacturing Rigorous Standards and Quality Control
Leading manufacturers employ cutting-edge technology to produce HNBR O-rings, adhering to stringent international quality standards such as ISO and ASTM. This commitment to quality ensures that every O-ring rolling off the assembly line meets the exacting demands of diverse industries. Companies frequently invest in R&D to enhance properties of HNBR, making sure it aligns with evolving technical requirements. Industry certifications further authenticate the reliability of HNBR O-rings in various applications.
Trustworthiness Commitment to Sustainability and Safety
Committed to eco-friendly practices, manufacturers prioritize sustainable production processes for HNBR O-rings. They employ recyclable materials and energy-efficient technologies to minimize the environmental footprint. Additionally, safety tests focus on ensuring that O-rings do not leach toxic substances, which is particularly crucial in food processing and pharmaceutical industries where contamination is a key concern.
Conclusion Choosing the Right HNBR O-Ring for Your Application
Selecting the appropriate HNBR O-ring involves evaluating the specific requirements of the intended application — from chemical exposure and temperature fluctuations to mechanical stresses. Consult with experts who can provide insights into the best composition and design suited to your operational needs. The future of HNBR O-rings lies in their adaptability and enduring performance, delivering value across various scenarios.
By understanding the production processes, chemical properties, and field-tested performance characteristics of HNBR O-rings, industries can make informed decisions, ensuring efficiency, durability, and reliability in their operations.