The seal ring, an essential component in various industrial and mechanical applications, plays a crucial role in maintaining system integrity by preventing leakage of liquids or gases. Understanding the intricacies of seal rings is vital for manufacturers and end-users alike, as it enhances the performance and longevity of machinery. This article delves into the practical experience, technical expertise, authoritative insights, and trustworthy recommendations regarding seal rings to optimally guide your selection and application process.
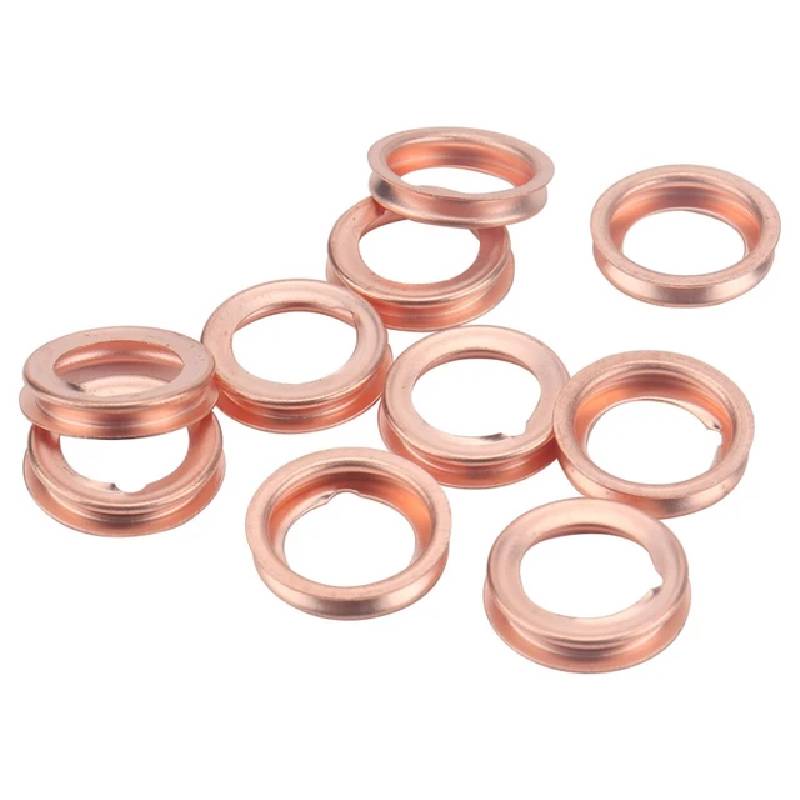
In the realm of mechanical engineering and manufacturing, seal rings are distinguished for their multifaceted utility across diverse sectors such as automotive, aerospace, oil and gas, and pharmaceuticals. These rings, typically crafted from materials like rubber, metal, or composite substances, are designed to fit snugly between components to create a barrier against leakage.
Their effectiveness in ensuring airtight and watertight seals is critical for the operational efficiency and safety of systems.
A notable experience shared by industry professionals highlights the consequences of neglecting seal ring quality in machinery. An automotive firm witnessed a substantial reduction in warranty claims and repair costs by upgrading their engine components with high-quality seal rings. This transition not only improved engine performance by minimizing oil leakage but also enhanced customer satisfaction and trust in the brand.
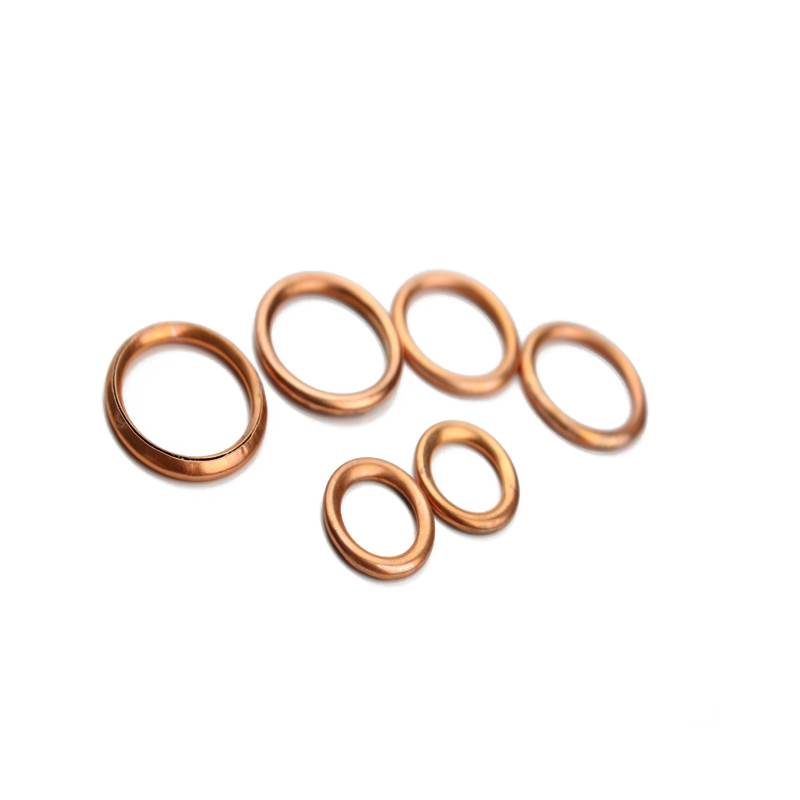
Expertise in the selection of seal rings is paramount. Engineers must consider factors such as pressure, temperature range, chemical compatibility, and environmental conditions when choosing the appropriate seal ring. For high-temperature applications, like those in aerospace engineering, seal rings made of materials such as Viton or silicone are preferred due to their ability to withstand extreme heat without degrading. Conversely, for applications involving harsh chemicals, PTFE (Teflon) seal rings offer superior chemical resistance.
seal ring
In establishing authoritative guidance on seal ring utilization, industry standards such as those set by the Society of Automotive Engineers (SAE) and the International Organization for Standardization (ISO) serve as benchmarks. Compliance with these standards ensures that seal rings meet the rigorous demands of modern engineering applications, thereby affirming their reliability and safety. Knowledge of these standards not only aids in compliance but also boosts the credibility of the manufacturers in competitive markets.
Trustworthiness in the context of seal rings hinges on rigorous testing and validation of their performance under simulated operational conditions. Reputable manufacturers employ advanced testing methodologies, such as accelerated life testing and finite element analysis, to predict the longevity and performance of seal rings under various stressors. Independent certification and third-party verification further establish confidence in the quality and durability of these products.
Going beyond technical specifications, understanding the ecological impact of seal rings is becoming increasingly important. Eco-friendly innovation in the production of seal rings involves utilizing recyclable materials and processes that minimize environmental footprints. Companies committed to sustainability often garner greater trust and loyalty from environmentally conscious consumers and partners, thereby driving market success.
In conclusion, the seal ring is more than a simple component; it is a pivotal element that embodies the intersection of engineering precision, material science, and environmental stewardship. Mastery in the application and selection of seal rings can result in enhanced machinery performance, reduced maintenance costs, and affirmed regulatory compliance. As industries evolve with technological advancements and eco-focused perspectives, the role of the seal ring becomes ever more critical, necessitating informed decisions based on experience, expertise, authoritative guidance, and trustworthiness.