The O-ring is a small yet indispensable component in a multitude of products, playing a critical role in ensuring secure and leak-proof operations across various industries. The following analysis delves into the profound significance of O-rings, their applications, material considerations, and best practices to enhance their performance and longevity.
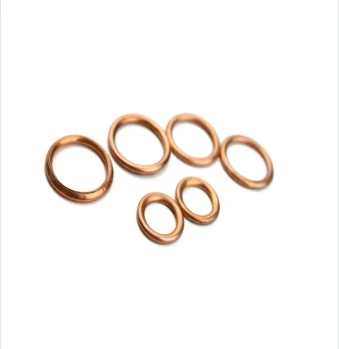
O-rings serve as mechanical gaskets in various equipment, from automobiles to aerospace technologies. Their primary function is to block pathways that could allow fluids or gases to escape, maintaining pressure within the system. This is achieved by placing the O-ring into a groove and compressing it during assembly, creating a tight seal through its elastic properties.
Experience with O-rings reveals that their effectiveness lies in material selection, which depends heavily on the environmental conditions they will face. For instance, O-rings made from nitrile rubber are well-suited for automotive applications due to their resistance to petroleum-based oils and fuels. In contrast, silicone O-rings excel in high-temperature environments, making them ideal for aerospace and cooking appliances.
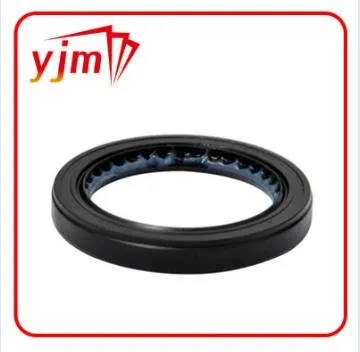
Professional expertise underscores the importance of understanding the operational conditions of O-rings, including temperature variations, chemical exposure, and physical stresses. Selecting the wrong material can lead to premature failure, potentially causing catastrophic system leaks. Engineers and designers must possess a thorough understanding of each material's properties, ensuring optimal performance throughout the product's lifecycle.
The authority of the O-ring as a sealing solution is unmatched, thanks to its simple yet effective design. Experts have continually favored O-rings due to their ease of installation, low cost, and reliability. The standardized design facilitates ease of replacement and minimizes downtime during maintenance, further solidifying their esteemed position in mechanical applications.
o ring
Trust in O-ring performance is bolstered by rigorous testing and quality standards set by international bodies. Compliance with specifications such as SAE AS568B, which defines dimensional tolerances and material grading, ensures that O-rings meet the highest standards of reliability and safety. Manufacturers are encouraged to prove their products through industry certifications, establishing themselves as trustworthy suppliers in a market that demands excellence.
Enhancing the performance of O-rings involves best practices backed by a combination of expertise, experience, and adherence to authoritative guidelines.
Proper lubrication during assembly can prevent abrasion during installation and extend service life. Additionally, the use of the correct size and material for each application prevents over-compression or inadequate sealing.
Real-world experiences consistently advocate for routine inspections and maintenance, where O-rings are examined for signs of wear or distortion. Proactive measures can preempt failures and ensure that systems remain operational, safeguarding the investments made into complex machinery.
In conclusion, the substantial role of O-rings across various products is a testament to their design simplicity and operational effectiveness. Through professional expertise and an authoritative understanding of materials and application conditions, O-rings continue to be pivotal in achieving secure, reliable, and long-lasting seals. The trust established in their performance is a result of continuous innovation and adherence to high standards, securing their place as an indispensable component in mechanical engineering.