When considering the procurement of seals, specifically those with dimensions 12x24x5, it’s crucial to understand their significance in various industrial and mechanical applications. Seals are indispensable components designed to prevent fluid leakage, seal openings, and protect systems from contamination, all while ensuring efficient operation. The specifications 12x24x5 denote a precise size that is commonly used in various machinery and industrial equipment.
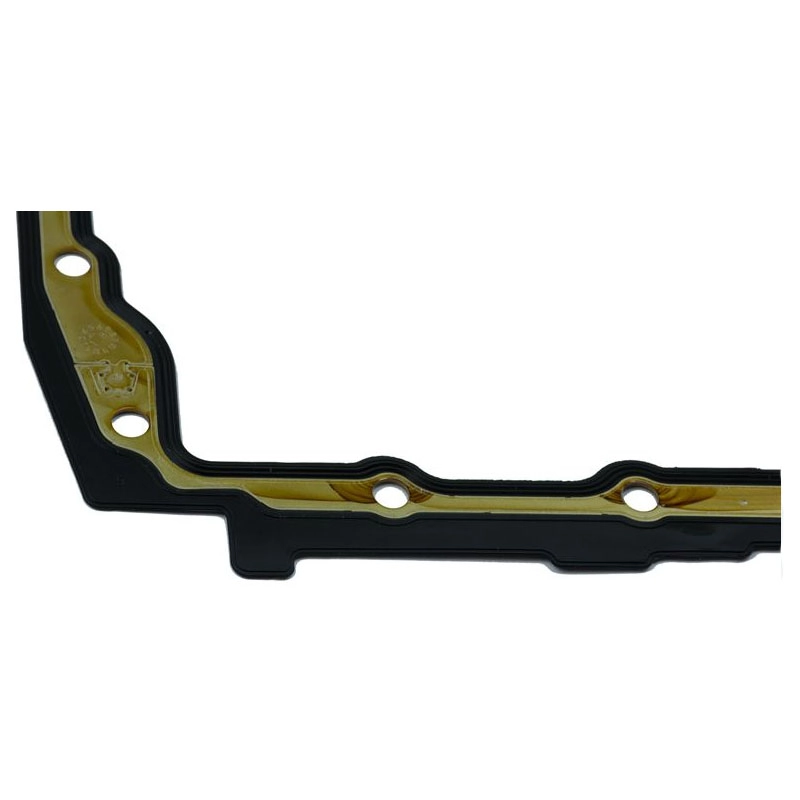
At the heart of seal operation is its material composition, which significantly impacts its performance and longevity. High-performance seals of this size are typically crafted from materials such as nitrile rubber (NBR), fluorocarbon rubber (FKM), or silicone. Each of these materials offers distinct advantages. Nitrile is praised for its excellent oil resistance, making it ideal for automotive applications, while fluorocarbon boasts exceptional thermal and chemical resistance suitable for aerospace and both heavy and light industrial applications. Silicone seals, on the other hand, provide superior flexibility and endurance in extreme temperatures, making them suitable for diverse applications, including food and beverage industries.
The 12x24x5 seal size is used predominantly in rotary applications, where shafts require a tight, friction-minimized fit to prevent leaks. These might include applications in automotive crankshafts, air compressors, and light machinery. The precision in the mentioned dimensions ensures that the seal fits snugly within its designated housing and onto the shaft, preventing any axial or radial misalignment that could lead to premature wear or failure.
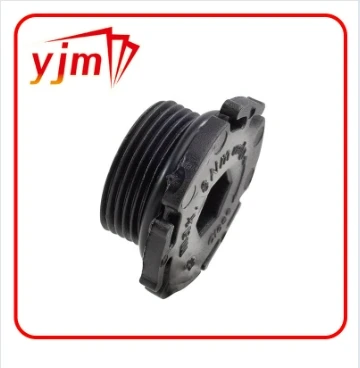
Expertise in selecting the right seal extends beyond simply matching dimensions and materials. An understanding of an application’s pressure and speed dynamics is critical. For high-speed rotational applications, a seal must possess a low coefficient of friction to reduce heat generation and energy loss. It should also withstand the operational pressure without deforming, which could compromise sealing integrity. For this reason, selecting seals with appropriate durometer ratings, which measure hardness, is essential for achieving optimal performance.
One must also consider the lip design of the seal. Common designs include single-lip or double-lip configurations. A single-lip seal is typically sufficient for low to moderate pressure settings where the primary need is to contain lubricants. However, in cases where the primary and secondary separation of fluids is necessary, a double-lip seal, which includes a secondary lip to create an additional barrier against contaminants, is preferred. This is especially relevant in mechanical and hydraulic systems where contamination control is critical to maintaining system integrity.
seal 12x24x5
Durability and reliability are hallmarks of high-quality 12x24x5 seals. Therefore, sourcing these products from reputable manufacturers who adhere to rigorous testing standards ensures that the seals can withstand the demanding conditions they are subjected to. Manufacturers often provide comprehensive data sheets detailing operational limits such as maximum temperature range, pressure thresholds, and expected life cycle, enabling informed decision-making.
In ensuring trustworthiness, it is important to address installation practices. Proper installation is pivotal in realizing the desired performance. Incorrect installation can lead to issues such as lip inversion, spring dislocation, or housing damage. Employing the correct tools and following manufacturer-recommended procedures helps mitigate these risks, ensuring longevity and optimal functionality.
As technology evolves, so too does the enhancement of sealing solutions. Innovations, such as incorporating advanced compounds, novel manufacturing techniques, and improved design paradigms, continue to push the boundaries of seal performance. Companies investing in these advances will provide sealing solutions that not only meet but exceed the standards set by traditional seals.
In conclusion, seals with dimensions of 12x24x5 are small yet mighty components integral to countless systems. By comprehensively understanding their composition, application requirements, and installation considerations, one can significantly enhance performance, reliability, and system longevity. Whether you are an engineer, maintenance manager, or procurement specialist, the expertise and insight into selecting these critical components form the bedrock of efficient, leak-free operations. Make informed choices and partner with trusted suppliers to ensure your machinery and equipment are safeguarded by the best seals available.