Quad ring seals, often overshadowed by their more traditional counterparts like O-rings, have emerged as a game-changer in the sealing industry. Recognized for their unique design and superior functionality, these seals are essential components in a wide range of industrial applications. What makes quad ring seals stand out, however, is their capacity to provide an unparalleled balance of performance, durability, and efficiency.
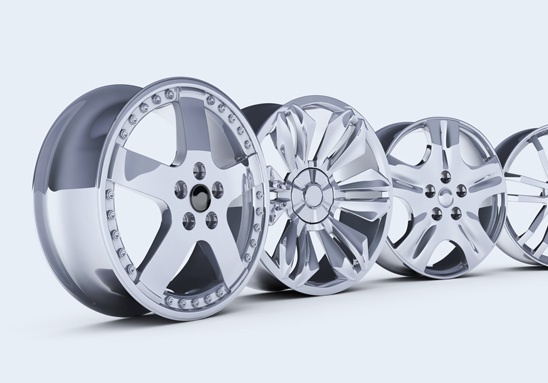
Drawing from personal experience within the manufacturing sector, it's clear that the quad ring seal is not just a fad but a strategic choice for organizations looking to optimize machinery performance and longevity. These seals are particularly advantageous in hydraulic and pneumatic applications where high pressure and critical sealing are paramount. The four-lobed construction of quad ring seals minimizes the risk of spiraling, a common hazard with traditional O-rings.
This ultimately leads to enhanced operational stability and reduced maintenance costs.
Diving deeper into the technical expertise, quad ring seals offer superior fluid retention, thanks to their unique cross-sectional design. This feature ensures an even distribution of pressure across the entire sealing surface, effectively minimizing wear and tear. The seal's profile allows for excellent resistance to extrusion, which is critical in high-pressure scenarios where seal integrity is non-negotiable. These properties make quad rings suitable for use in equipment subjected to frequent cycles of loading, thereby maintaining optimal performance under a variety of operational conditions.
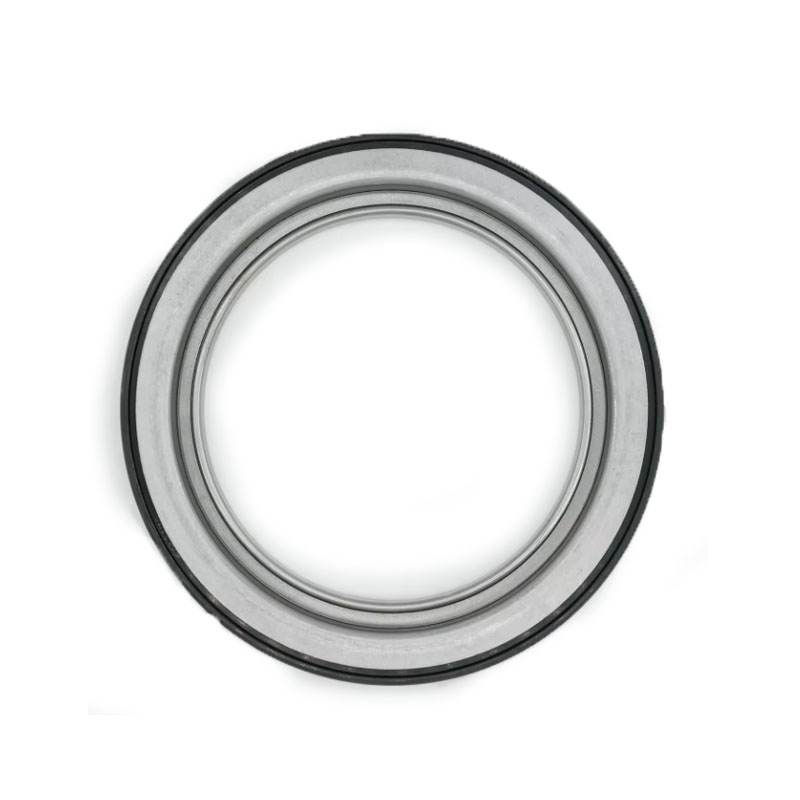
From an authority standpoint, industry leaders and engineers articulate that selecting the appropriate seal can significantly influence the efficiency and safety of industrial systems. Quad ring seals are often the go-to for aerospace, automotive, and manufacturing sectors, where reliability and precision are non-negotiable. These seals radically conform to stringent industry standards, such as ISO and ASTM, which further corroborates their dominance in critical applications.
quad ring seal
Trustworthiness is another dimension where quad ring seals excel. Not only do they exhibit considerable longevity compared to other seals, but they also demonstrate reliability in adverse conditions, including extreme temperatures and corrosive environments. The materials used in manufacturing quad ring seals, such as Viton, nitrile, and EPDM, are selected for their superior chemical resistance and temperature tolerance. This assures users of their lasting performance, even beyond typical environmental challenges.
Feedback from users across various sectors consistently highlights the reduced downtime and enhanced productivity associated with quad ring seals. Companies have reported decreased incidences of machine breakdowns and a subsequent increase in output, attributing this to the robust nature of the quad ring seal. Furthermore, the cost benefits derived from fewer replacements and repairs contribute significantly to operational efficiency, making these seals a cost-effective solution for businesses of all sizes.
In conclusion, quad ring seals are not just functional components but pivotal in optimizing industrial processes. Their unique design, coupled with unmatched performance, positions them as a trusted solution in high-stakes environments. As industries continue to evolve, seeking better performance and efficiency, the adoption of quad ring seals is likely to rise, reinforcing their status as indispensable assets in modern engineering. For those in search of a reliable, durable, and efficient sealing solution, investing in quad ring seals is a decision backed by expertise, authority, and proven results.