Fuel resistant O-rings are pivotal components in numerous industrial applications, known for their ability to withstand the corrosive nature of fuels. They form a critical part of the machinery in sectors ranging from automotive to aviation, safeguarding against leaks and ensuring functionality under extreme conditions. As the demand for high-performance and durable materials intensifies, understanding the nuances of fuel resistant O-rings becomes paramount.
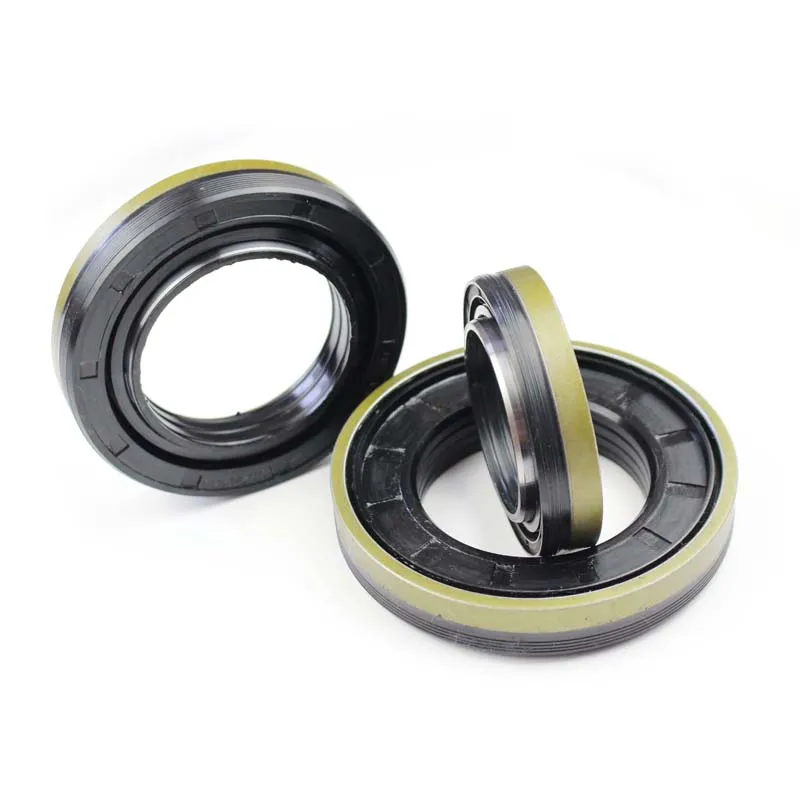
These O-rings are crafted from specially formulated materials such as Viton, fluorosilicone, and hydrogenated nitrile butadiene rubber (HNBR). Each of these materials brings unique properties tailored to meet specific industry needs. Viton, renowned for its exceptional chemical resistance and thermal stability, is a preferred choice in automotive applications, where exposure to high temperatures and aggressive fuels is common. Fluorosilicone, offering flexibility over a wide temperature range, finds use in aerospace sectors, where both thermal extremes and fuel resistance are critical. HNBR, with its balance of mechanical strength and fuel resistance, is often used in industrial machinery.
Case studies abound in demonstrating the efficacy of these O-rings. For instance, a leading automotive manufacturer replaced traditional rubber seals with Viton O-rings in their fuel systems, resulting in a 50% reduction in leaks over a typical five-year vehicle lifespan. This tangible improvement not only enhanced vehicle reliability but also significantly reduced warranty claims related to fuel system failures. These real-world applications underscore the importance of selecting the right material for the O-ring based on the operational environment.

Expertise in selecting and utilizing fuel resistant O-rings also involves understanding the tolerances and pressure limits they are designed to endure. Engineers and designers need to collaborate closely with suppliers to ensure that the selected O-ring fits precisely within the application while withstanding the pressures it will face. Using simulation software to predict performance can further assure the suitability of the chosen O-ring, mitigating the risk of premature failures.
fuel resistant o rings
Authoritativeness in the realm of O-rings comes from continual research and development, which leads to innovations in material science and manufacturing techniques. Leading manufacturers invest significantly in R&D to develop O-rings that offer even higher performance metrics, such as improved permeation resistance and extended operational life. Engaging with research papers and attending industry conferences can provide insights into the latest advancements, cementing a brand's position as a thought leader in the field.
Trustworthiness is established through rigorous testing and certification from recognized bodies. Certifications from organizations such as ISO and ASTM provide assurances of quality and compliance with international standards. Collaborating with certified manufacturers ensures that the O-rings are fit for purpose, passed through stringent quality controls, and consistently deliver on their performance promises.
In conclusion, fuel resistant O-rings are not merely functional components; they are critical to the safety and efficiency of complex systems across multiple industries. By choosing the right materials, understanding the application requirements, staying abreast of technological advancements, and ensuring compliance with international standards, businesses can significantly enhance their operational reliability and performance. In a world where fuel efficiency and safety are increasingly prioritized, the role of fuel resistant O-rings is indispensable, making them a focal point of industrial design and innovation.