In the world of industrial machinery, the performance of an entire system often hinges on seemingly small components. Among these, O-ring valve seals play a pivotal role in ensuring the efficiency and reliability of various systems. Their importance cannot be overstated, particularly in industries where precision and reliability are paramount.
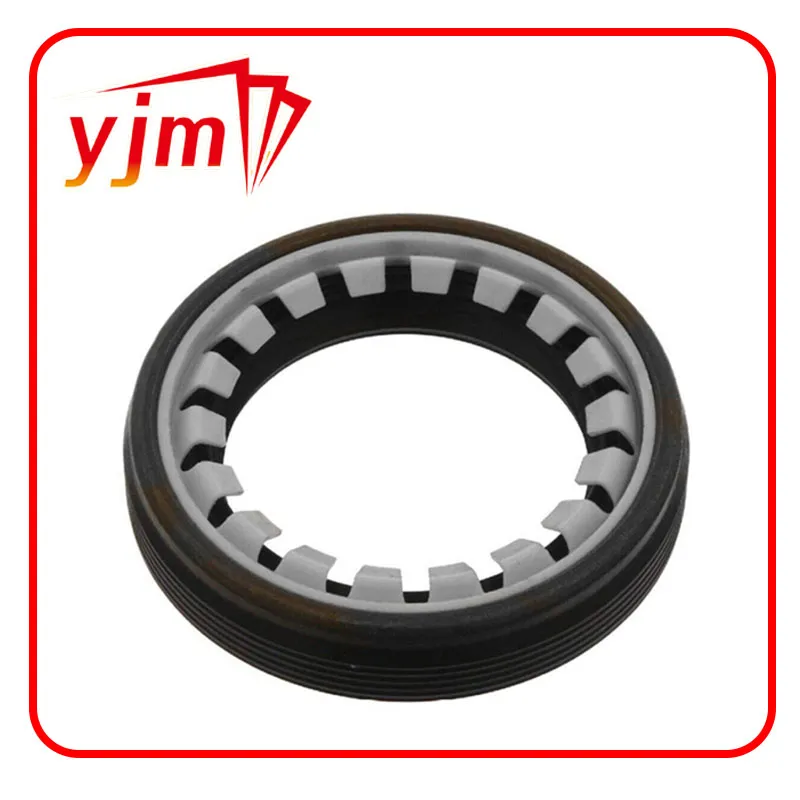
O-ring valve seals are circular gaskets made primarily from elastomers such as nitrile, silicone, or fluorocarbon rubber. Their primary function is to prevent the passage of fluids or gases by blocking any potential escape routes between joint surfaces. These rings are crucial in maintaining pressure within hydraulic and pneumatic systems, as well as in the engines of automotive machinery.
One of the most significant advantages of O-ring valve seals is their versatility. Due to their simplicity in design, they can be used in static, dynamic, and vacuum sealing applications. Their ability to return to their original shape after deformation due to pressure makes them especially effective in dynamic applications, where parts move relative to each other. This feature ensures longevity and a consistent seal even under varying pressures and temperatures.
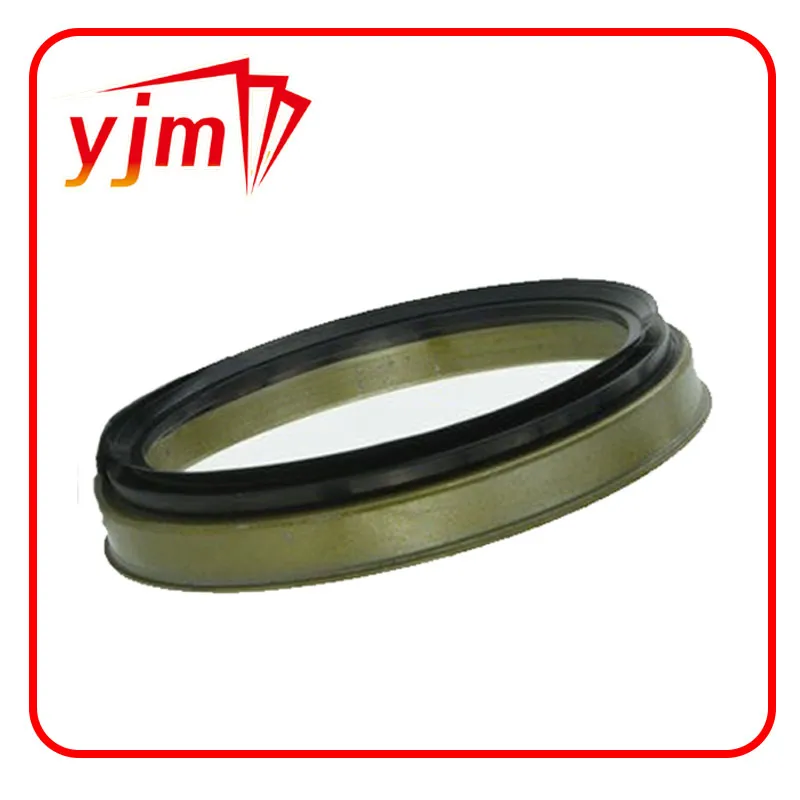
From an expertise perspective, choosing the right material for an O-ring is critical. The material directly correlates with the application's environment. For instance, nitrile rubber is excellent for applications involving water and hydraulic oils due to its resistance to these substances. On the other hand, fluorocarbon elastomers are preferred for high-temperature applications or those involving aggressive chemicals. Understanding the specific demands of your application is the first step toward selecting the appropriate O-ring material.
o ring valve seals
When discussing authority, it is crucial to acknowledge the standards to which O-ring valve seals are manufactured. These components must adhere to rigorous international standards such as those defined by the International Organization for Standardization (ISO) and the American Society for Testing and Materials (ASTM). These standards ensure that O-rings provide reliable performance under specified conditions, making them trusted components in safety-critical systems.
Trustworthiness in O-ring valve seals is built over time through consistent performance. Manufacturers of these seals often provide detailed testing reports that verify the seal's performance under simulated real-world conditions. Users seeking reliability should opt for products who provide transparency in testing and certification. This commitment to quality assurance helps cultivate trust among consumers, reinforcing the reliability of using authenticated O-ring seals.
From a personal experience-based viewpoint, utilizing O-ring valve seals can significantly reduce maintenance costs and downtime. A faulty seal can lead to leaks, which, in turn, can cause systems to fail or function inefficiently. By investing in high-quality seals and ensuring proper installation, businesses can achieve operational efficiency and avoid costly repairs. Moreover, the ease of replacing O-rings ensures minimal disruption, making them a preferred choice for maintenance professionals.
In summary, O-ring valve seals are indispensable components in a multitude of industries due to their simplicity, versatility, and reliability. Expertise in selecting the right material, adherence to stringent manufacturing standards, and proven performance records are essential criteria when choosing an O-ring. Their role in maintaining system integrity, reducing downtime, and ensuring safety make them a fundamental choice for engineers and technicians. When procured from a credible manufacturer, these unsung heroes of industrial machinery prove to be a wise investment, safeguarding both system performance and company resources.