Choosing the right O-ring piston seal is crucial for the optimal performance and longevity of machinery and devices reliant on pneumatic or hydraulic systems. This critical component maintains the integrity of the chamber it seals, ensuring efficient energy transfer and preventing leaks. By drawing on years of industry experience and expertise, this guide will delve into the essential qualities of an effective O-ring piston seal and provide practical advice on selecting the best product for your needs.
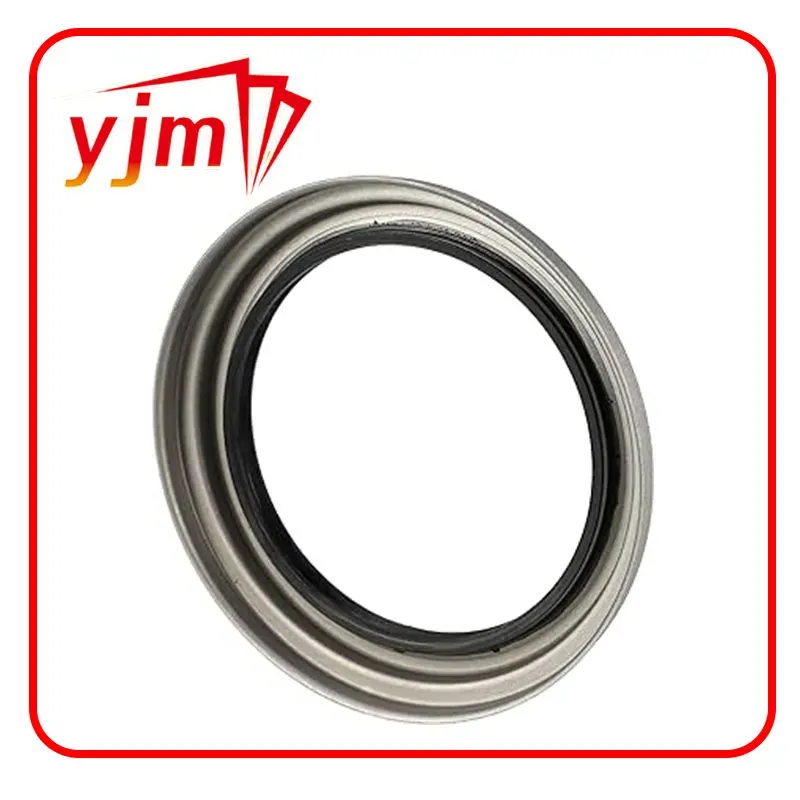
O-ring piston seals are most commonly found in applications ranging from automotive engines to industrial machines, where they prevent fluid or gas leakage between the piston and the cylinder. One imperative aspect when selecting an O-ring is understanding the operating conditions, including temperature extremes, pressure variations, and the nature of the fluid or gas involved. For example, in environments that encounter high temperatures, materials like Viton or Silicone may be more applicable due to their resistance to heat as compared to Nitrile rubber, which is more suited for moderate temperatures.
Understanding material compatibility is vital for product longevity and performance. Not all materials perform equally in every scenario. Fluorocarbon (Viton) O-rings, for instance, exhibit remarkable chemical resistance to solvents and fuels, making them preferable for automotive or aerospace applications. However, their high-temperature stability comes at a higher cost compared to general-purpose materials like Nitrile. Ultimately, selecting the right material involves balancing performance requirements with budget constraints.
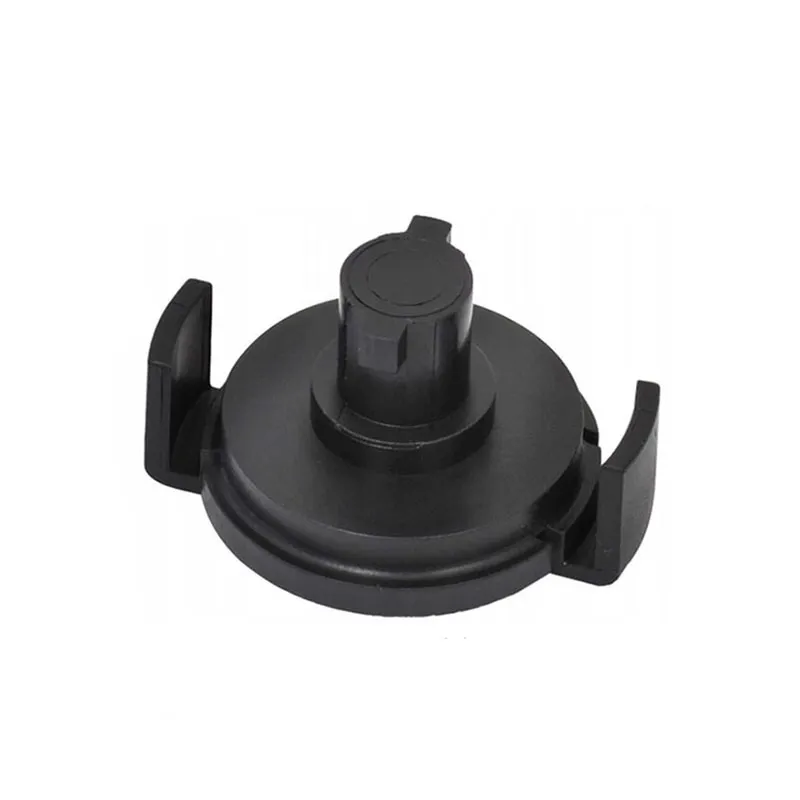
Dimensional accuracy and installation are other areas where expertise proves invaluable. An improperly fitted O-ring can lead to premature failure, leaks, or extensive damage to machinery. Measurement should not just account for the diameter but also for the cross-section thickness, ensuring it matches the specifications of the equipment. Installation requires careful handling to avoid twisting or pinching, phenomena that are often responsible for early seal degradation.
Authoritativeness in the field of O-ring technology comes not just from technical specifications, but also from trusted third-party certifications and industry standards compliance. Reputable manufacturers often provide comprehensive documentation and testing results that verify their product's suitability for specific applications. Adhering to standards like those set forth by ASTM or ISO can provide additional peace of mind. Engaging with certified suppliers helps build a layer of trustworthiness, reinforcing confidence in the seals used.
o ring piston seal
From a practical standpoint, routine maintenance and monitoring are indispensable practices. Even the most robust O-ring piston seals are susceptible to wear over time due to friction, chemical exposure, or mechanical stress. Regular inspections under operational and off-line conditions can help detect early signs of deterioration, such as surface cracks or flattening, that might otherwise lead to system failures. Maintaining a log of maintenance activities can also assist in predicting and preventing future issues.
In keeping with the contemporary thrust towards environmental sustainability, it’s also worth considering the lifecycle impact of seal materials. Some manufacturers have started to offer eco-friendly alternatives that do not compromise on performance. These innovations use sustainable manufacturing processes or materials that reduce environmental impact. Opting for such green options might provide an additional layer of consideration, beyond traditional efficacy metrics.
Lastly, it’s essential to remain updated with ongoing advances in sealing technology. As industries evolve, so do sealing requirements and technologies. New composite materials, enhanced by nanotechnology or improved manufacturing techniques, are continually being developed. Engaging with trade publications, attending workshops, and continuous education sessions benefit decision-makers by providing fresh insights into emerging trends and helping to maintain competitive advantages.
In conclusion,
the selection of an O-ring piston seal should not be taken lightly. It requires a combination of technical expertise, material knowledge, and trust in the manufacturing process. By prioritizing these key considerations, industries can ensure optimal machinery performance and maximize the lifespan of their components. Whether in crafting, maintaining, or innovating with seals, the importance of a well-informed approach can never be understated, as it is integral to achieving operational excellence.