Exploring the World of O-Rings Innovative Solutions for Modern Industries
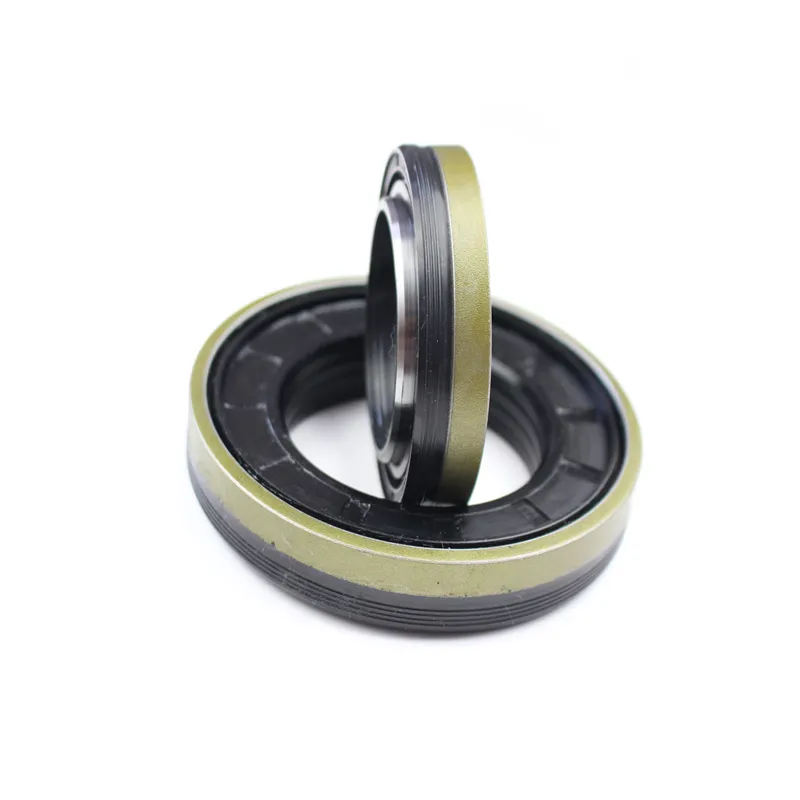
The engineering world is no stranger to the importance of robust seals, and O-rings are a quintessential element in this realm. As industries evolve, the demand for high-quality sealing solutions has grown exponentially, elevating O-rings to an indispensable status. Yet, not all O-rings are created equal; variations in materials and designs cater to specific industrial needs. Let's delve into the intricacies of O-rings, unveiling the secrets behind their unparalleled success and why they matter more today than ever.
The Essence of O-Rings
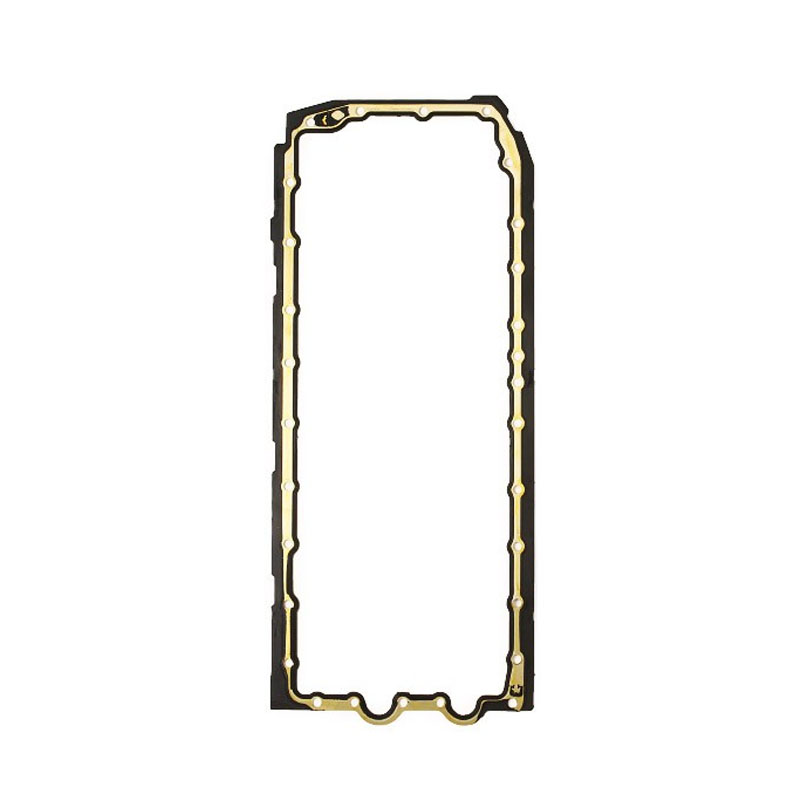
At the core of any O-ring's functionality is its unique toroidal shape, which creates a robust seal between two surfaces. This simple yet effective design is revered for its capacity to withstand extreme pressure and temperature variations. Industries such as automotive, aerospace, and pharmaceuticals rely heavily on O-rings to maintain system integrity and prevent leakage. But what makes these circular components the first choice for engineers worldwide?
Material Matters From Elastomers to Metals
The material composition of an O-ring determines its suitability for specific applications. Rubber and elastomers, including nitrile, silicone, and fluorocarbon, offer flexibility and resistance to various chemical exposures. Nitrile rubber, for instance, excels in oil-resistant applications, making it a preferred choice in the automotive industry. On the other hand, silicone rubber is ideal for high-temperature environments due to its thermal stability.
Beyond conventional materials, industries are increasingly exploring metal O-rings. These are particularly beneficial in high-pressure applications due to their ability to maintain integrity under extreme conditions. Stainless steel, nickel alloys, and copper are some of the metals transforming O-ring applications in sectors like aerospace and petrochemicals.
Innovations Driving Precision
The evolution of manufacturing technologies has a significant impact on O-ring production. Advanced methodologies such as precision compression molding and injection molding have set new benchmarks in quality and consistency. These processes allow manufacturers to produce O-rings that adhere to the most stringent tolerances, ensuring that each unit performs optimally within its designated environment.
Moreover,
custom O-ring solutions are becoming increasingly popular. Companies now offer bespoke sealing solutions tailored to specific industrial needs, considering factors such as pressure, temperature, and media exposure. This tailored approach enhances performance and reliability, fostering trust among industry stakeholders.
o ring o ring
Certifications and Quality Assurance
The reliability of an O-ring is heavily contingent upon strict adherence to industry standards. Organizations such as ISO (International Organization for Standardization) and ASTM International (formerly known as American Society for Testing and Materials) set rigorous guidelines to ensure quality and consistency. O-ring manufacturers dedicated to excellence often undergo comprehensive certification processes, which include testing for tensile strength, elongation, volume change, and compression set.
This adherence to standardized testing and certification builds trust and reassures end-users of the product's dependability. Purchasing from certified manufacturers means investing in equipment longevity and operational safety, minimizing risks associated with seal failures.
Challenges in O-Ring Applications
Despite their effectiveness, O-rings face challenges that can compromise their sealing capabilities. Factors like improper installation, compression set, and material incompatibility can lead to premature failure. Users must be diligent in selecting the right O-ring material for specific applications, taking into consideration the operational environment's temperature, pressure, and chemical exposure.
Additionally, ensuring that installation is conducted appropriately is critical. Misalignment or over-compression can permanently damage an O-ring, leading to potential leaks and system failures. Regular maintenance checks and adhering to manufacturer's guidelines can mitigate these risks, ensuring the O-rings perform optimally throughout their lifecycle.
The Future Outlook Sustainability and Beyond
The future of O-rings lies in sustainable manufacturing practices and innovative materials. The push towards eco-friendliness is prompting manufacturers to explore biodegradable and recyclable materials without compromising the functional integrity of O-rings. Ongoing research in polymer science promises the development of next-generation O-rings that can withstand harsher environments while leaving a minimal carbon footprint.
In conclusion, the humble O-ring remains a vital component in engineering solutions worldwide. As industries continue to function in more demanding environments, the evolution of O-rings in material science, precision manufacturing, and sustainable practices ensures that they remain pivotal in maintaining operational integrity across sectors. The commitment to innovation and adherence to quality standards reflect their undeniable value in the modern industrial landscape.