Understanding the functionality of oil seals is crucial for anyone involved in machinery maintenance, automotive industries, or engineering. Oil seals, also known as rotary shaft seals, play an indispensable role in ensuring the efficient operation of engines and other mechanical devices. They are more than mere barriers between moving and stationary components; they are meticulously engineered devices that protect mechanical systems from contaminants and leakage.
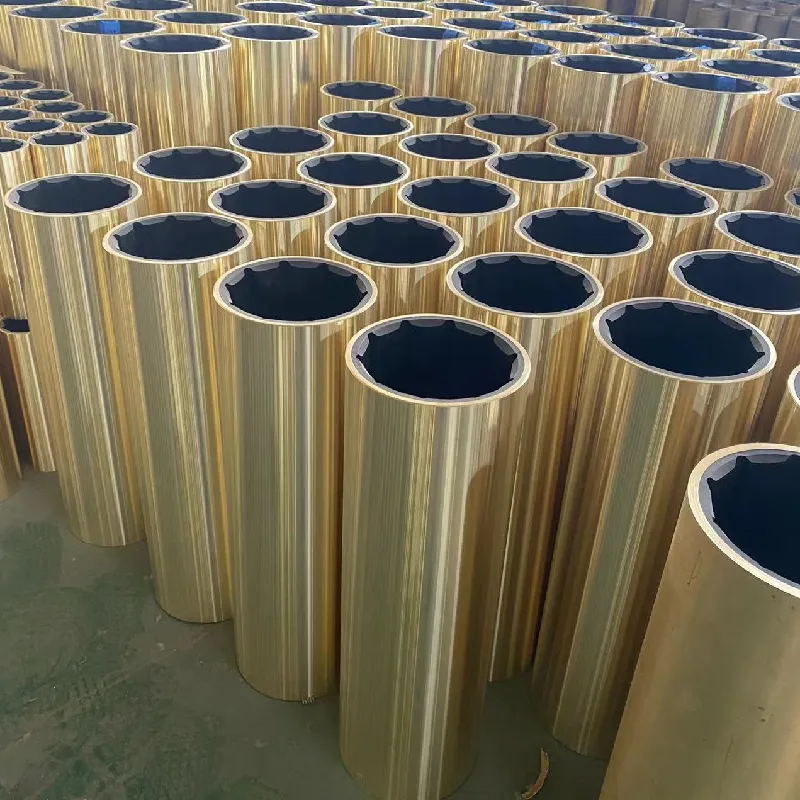
At the core of an oil seal's function is its ability to retain lubricants while excluding harmful contaminants. This is achieved through their unique structure comprising a metal outer case, a flexible inner lip, and a garter spring. The metal outer case provides structural support and rigidity, ensuring the seal firmly fits into its housing. The flexible inner lip, typically made of rubber or elastomer, creates a tight seal against the rotating shaft. The garter spring applies the necessary radial force to maintain the seal's contact, compensating for any shaft eccentricity or vibration.
Expertise in choosing the right oil seal begins with understanding the environment in which it will operate. Operational temperatures, types of lubricants, shaft speeds, and the presence of dust or debris are critical considerations. For instance, in high-temperature applications, fluorocarbon or PTFE seals are preferred due to their superior heat resistance. Conversely, in environments with heavy contamination, seals made with advanced dust lip configurations prevent abrasive particles from penetrating the sensitive components they protect.
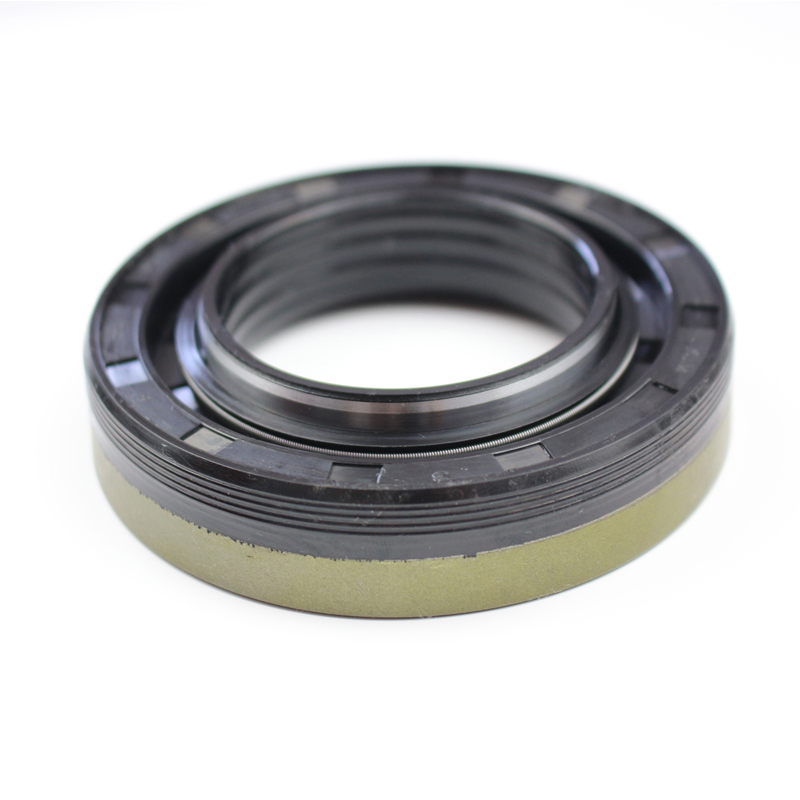
Reliability in performance underscores the authoritativeness of oil seals. Leading manufacturers conduct extensive testing under varied conditions to assure durability and efficiency. These seals are subject to rigorous evaluations, including tensile strength, compression set, and elongation tests to ascertain their resilience. Trustworthy brands maintain meticulous quality control processes, employing state-of-the-art technologies to design seals that meet, and often exceed, international standards.
oil seal function
The use of oil seals extends beyond just automobiles and industrial machinery. They are pivotal in office equipment, household appliances, and even aerospace engineering where precision is paramount. Each of these applications demands oil seals that deliver peak performance tailored to specific operational requirements. This wide range of applications demonstrates the versatility and indispensability of oil seals in modern engineering.
Experience shows that timely maintenance and replacement of oil seals can prevent catastrophic failures and costly repairs. Regular inspection for wear, alignment issues, and material degradation is advised.
When replacing oil seals, ensuring compatibility with the intended application is vital. Incorrect installation—either a misalignment or using a seal not designed for the specific service conditions—can lead to premature failure, emphasizing the significance of expertise in this domain.
In conclusion, oil seals might be small components, but their role in maintaining machinery efficiency and longevity is monumental. Their ability to prevent contamination, manage pressure variations, and sustain lubrication fundamentally impacts device performance and lifecycle. As technological advancements continue, oil seals will undoubtedly evolve, integrating new materials and designs to meet the ever-expanding demands of emerging applications. Recognizing their importance and investing in quality seals from reputable sources assures optimal performance and extended machinery life, validating their value in any mechanical assembly.