The high pressure shaft plays a pivotal role in numerous industrial applications, being embedded in systems that demand superior efficiency and reliability. As we unravel the complexities of this integral component, it becomes necessary to measure our understanding across various domains, such as design innovation, material selection, and expert handling, to ensure optimized performance in high-stakes environments.
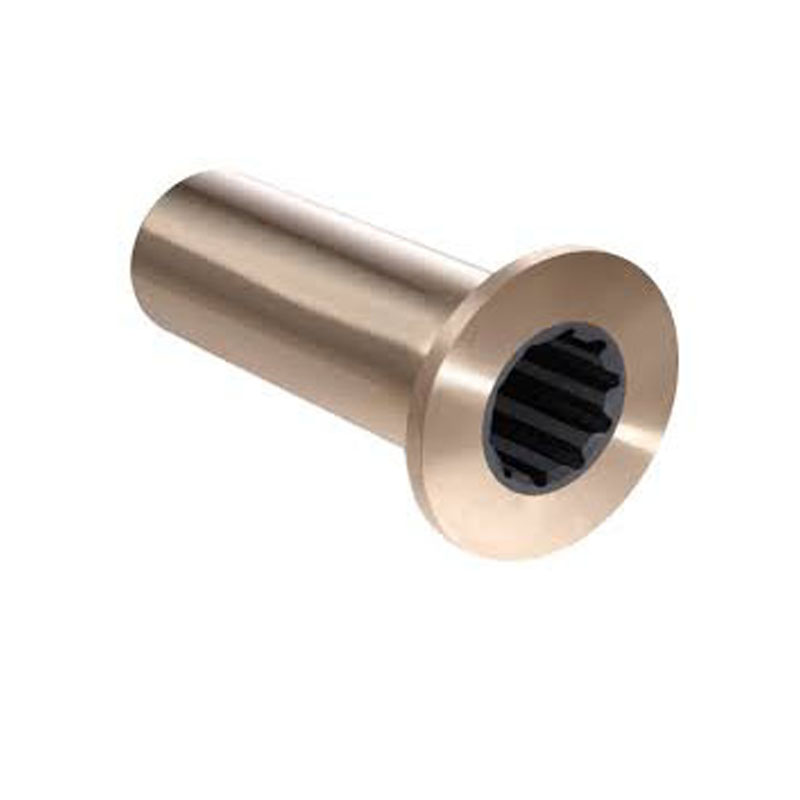
Over the past two decades, the evolution of high pressure shafts has been marked by a significant transformation facilitated by advanced materials and cutting-edge technologies. These shafts are crucial in mechanical assemblies such as turbines, automotive engines, and pump systems, where they bear and transfer high-torque loads. The choice of materials is particularly critical; manufacturers now prefer alloys with higher tensile strength and resistance to corrosion and high temperatures, such as titanium and high-grade stainless steel.
This provides remarkable durability, ensuring that the shafts remain operational under extreme conditions.
Expertise in manufacturing high pressure shafts hinges on precision engineering. Leading manufacturers employ computer-aided design (CAD) and finite element analysis (FEA) to create and optimize shaft designs. These tools determine stress distribution and predict how the shafts will behave under operational loads, thereby preventing premature failures. Moreover, employing state-of-the-art machining centers ensures that tolerances are maintained to within micro-level accuracies, critical for components that operate at high speeds and pressures.
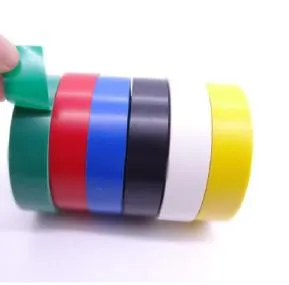
Authoritativeness in this domain is assured through compliance with industry standards and certifications such as ISO 9001 and API standards. Companies that garner these certifications usually exhibit a commitment to quality, ensuring their products meet rigorous international standards. Furthermore, these standards often dictate the maintenance protocols and safety parameters, reinforcing the reliability of high pressure shafts in various applications.
From a practical operational perspective, the experience of end-users and technicians plays a significant role in the effective deployment of high pressure shafts. In airlines, for example, the shaft's performance is consistently monitored through regular inspections and non-destructive testing (NDT) techniques like ultrasonic or magnetic particle testing. This regular surveillance not only identifies wear and tear before catastrophic failures can occur but also extends the life span of the component, thus lowering operational costs.
high pressure shaft
Developments in shaft lubrication and coating technologies have notably enhanced the trustworthiness of high pressure shafts. Advanced lubricant formulations reduce friction and wear, improving shaft durability immensely. In parallel, protective coatings are applied to thwart abrasive damage, which remains one of the common causes of shaft degradation.
Expert handling is paramount in the installation and maintenance of high pressure shafts. Installation often demands precise alignment and balance; failure to adhere strictly to installation protocols could lead to excessive vibrations and operational failures. The insistence on employing trained and certified professionals for these tasks underscores the critical nature of these components in industrial applications.
Moreover, digital monitoring systems and IoT-based predictive maintenance solutions are revolutionizing how high pressure shafts are managed. These systems continuously collect data on operational parameters, allowing for real-time monitoring and analysis. Such innovations significantly minimize unexpected downtimes by predicting potential issues before they become severe.
As industries continue to push the boundaries of ingenuity and efficiency, the implementation of sustainable practices concerning high pressure shafts is becoming more prevalent. Recycling and repurposing strategies not only contribute to environmental conservation but also engender cost savings, reflecting a collective shift towards eco-conscious manufacturing processes.
In conclusion, the production and operations involving high pressure shafts exemplify a convergence of innovative technologies, authoritative industry standards, skilled expertise, and sustainable practices. By fostering these dynamics, stakeholders within the industry ensure that these essential components faithfully serve their purpose, offering enhanced performance and reliability in a wide array of demanding applications. With the ongoing advancements in materials science and digital technology, the future prospects for high pressure shafts are poised for further growth and innovation, cementing their status as indispensable assets in modern engineering feats.