High pressure lip seals are a critical component in many industrial and mechanical systems, functioning as the primary defense against leaks in equipment that operates under high pressure environments. Their role is vital in ensuring the smooth operation and longevity of machinery by preventing fluid escape and excluding contaminants. Understanding the application, selection, and maintenance of high pressure lip seals is essential for professionals across sectors such as automotive, aerospace, marine, and manufacturing.
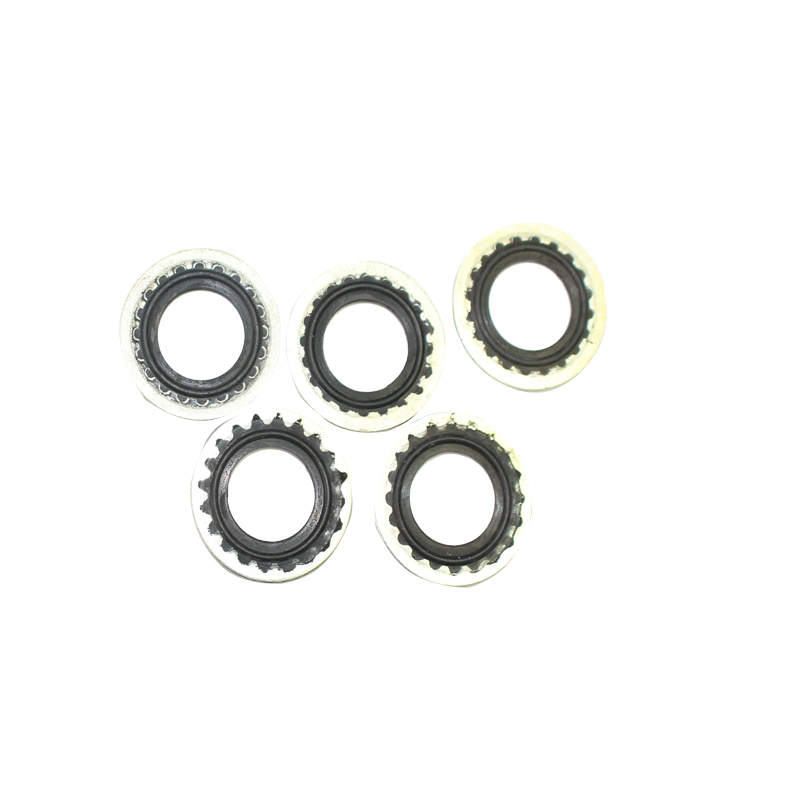
The design intricacy of high pressure lip seals makes them specialized products with unique features suited to handling challenging conditions. Typically constructed from materials such as nitrile rubber, fluorocarbon, or PTFE, these seals are chosen based on the properties they offer, such as temperature resistance, elasticity, and chemical stability. Choosing the right material is pivotal as it directly affects the seal's performance and durability. For instance, fluorocarbon seals exhibit excellent heat and chemical resistance, making them ideal for aerospace applications, whereas nitrile rubber might be more suited for automotive applications due to its cost-effectiveness and adequate performance range.
An experience shared by professionals in the field accentuates the importance of meticulous seal selection. In one notable case, a manufacturing plant faced repeated machinery downtimes due to seal failures. Upon investigation, it was determined that the previously used seals could not withstand the high-pressure condition and elevated temperatures. Transitioning to high-grade fluorocarbon lip seals resolved these issues, drastically reducing downtime and maintenance costs while enhancing the machines' operational efficiency.
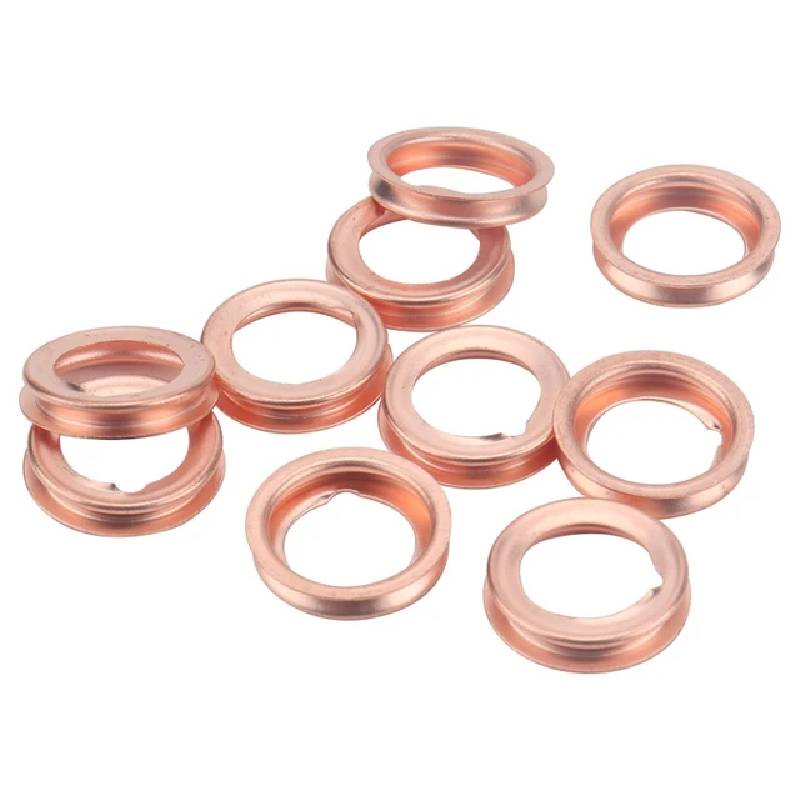
Expertise in high pressure lip seals hinges on understanding pressure ratings and seal design. These seals are engineered to operate under varying pressure levels, with the seal lip design critically influencing their performance. A lip seal must possess a finely tuned balance between lip stiffness and flexibility to adapt to pressure changes without sustaining wear or deformation. The precise engineering behind these seals requires manufacturers to have a profound understanding of fluid dynamics and material science, ensuring that each seal matches its application environment's technical demands.
high pressure lip seal
In terms of authoritativeness, several industry standards guide the production and application of high pressure lip seals. Organizations like the International Organization for Standardization (ISO) and the American Society for Testing and Materials (ASTM) provide frameworks ensuring consistency and quality across the board. These standards cover aspects like seal dimensions, materials testing, and performance criteria, helping manufacturers produce reliable products that meet global industry demands.
Building trustworthiness around high pressure lip seals involves the continuous improvement of seal designs based on feedback and testing protocols. Leading companies in this sector invest in research and development to push the bounds of current capabilities, often incorporating advanced technologies such as computer-aided design and simulation tests to perfect their products. Regular testing through both real-world applications and accelerated lifecycle testing helps in validating their ongoing performance and provides invaluable data that ensures seal integrity over extended periods under harsh conditions.
The future of high pressure lip seals involves innovation geared towards sustainability and efficiency. As the industry shifts towards more eco-friendly practices, manufacturers are exploring biodegradable materials without compromising on performance. Advanced coatings that reduce friction and wear are also under development, which can lead to decreased energy consumption in machinery and extend the lifecycle of both seals and equipment.
In conclusion, high pressure lip seals play an indispensable role across various industries, and their significance cannot be overstated. For professionals tasked with maintaining machinery efficiency and reliability, mastering the nuances of these seals—from selection to application—ensures optimal performance. The synergy of experience, expertise, authority, and trust forms the foundation of advancements in seal technology, paving the way for future innovations that will continue to uphold industrial integrity under high pressure.