High pressure rotary shaft seals play a pivotal role in the optimal functioning of machinery across numerous industries. These components are imperative for maintaining the integrity of systems by preventing fluid leaks and keeping contaminants out. In particular, their application can be seen in automotive, aerospace, and industrial machinery sectors, where they ensure the longevity and efficiency of serious mechanical equipment.
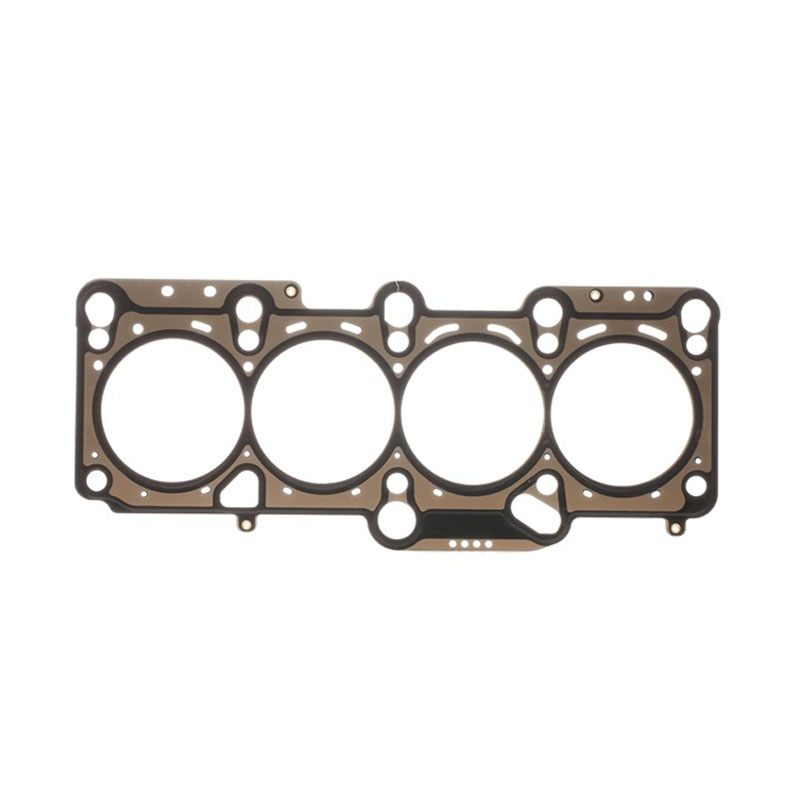
Real-world experience underscores the critical nature of high pressure rotary shaft seals. Consider the scenario of a manufacturing plant reliant on precision equipment to maintain quality control and productivity. A defective seal could mean unforeseen downtime, leading to significant operational losses. For many plant engineers and maintenance managers, investing in high-quality seals is an insurance policy against costly disruptions. This experience underscores why selecting the right seal is not a mere technical requirement but a strategic decision impacting business outcomes.
Expertise in choosing the right high pressure rotary shaft seal involves understanding specific application needs. Different environments demand different sealing capabilities. For example, a seal used in a chemical processing plant must be highly resistant to aggressive chemicals, while those in automotive applications may require resilience against high temperatures and pressures. Material selection, often involving rubbers like nitrile or fluorocarbon, coupled with precise dimensional tolerances, are commonly evaluated factors. Each selection criterion is akin to a chess move, where strategic foresight dictates lasting success in challenging mechanical setups.
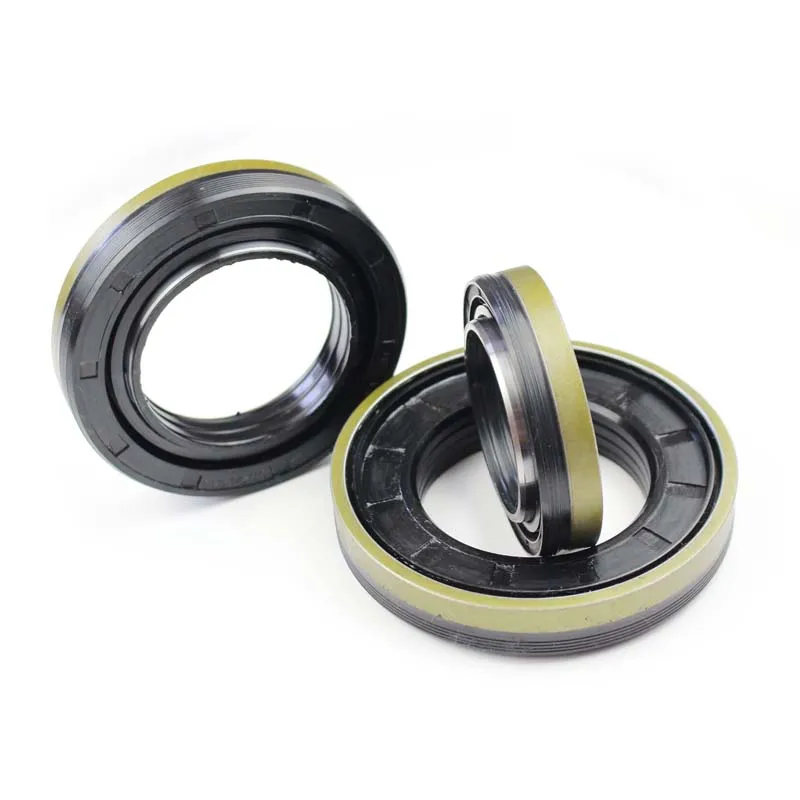
Authoritativeness on the topic comes from understanding global and industry-specific standards, which ensures compliance and peak performance. For instance, seals must often adhere to ISO 90012015 standards for quality management, ensuring that they meet international benchmarks for reliability and performance. Manufacturers who understand and implement these standards prioritize delivering products that can be trusted in the most critical applications. These industrial benchmarks serve as a reassurance to clients, ensuring that the seals will perform under specified conditions without failure.
high pressure rotary shaft seals
Trustworthiness with high pressure rotary shaft seals is critical, built over years of consistent performance and customer satisfaction. Leading manufacturers often offer extensive warranties and after-sales service, positioning themselves as not just providers but partners in business operations. Furthermore, transparent sharing of product data, from detailed specifications and performance metrics to case studies and client testimonials, reinforces trust. For engineers and purchasing managers, this transparency is vital, as it allows informed decisions grounded in demonstrated product performance.
The choice of high pressure rotary shaft seals affects operational safety, product quality, and financial outcomes, making them more than just an engineering component; they are essential contributors to business strategy. Businesses must partner with reputable suppliers who understand the complexity of demands posed by diverse industrial environments. Cutting-edge innovation, adherence to global standards, and robust customer support differentiate leading players in this domain.
In conclusion, high pressure rotary shaft seals are more than just mechanical components—they are vital investments in operational efficiency and reliability. Real-world experiences, professional expertise, adherence to standards, and unwavering trust play essential roles in ensuring that seals deliver impeccable performance. Engaging with a trusted seal provider can safeguard your machinery, optimize performance, and ultimately enhance your competitive edge in the process-driven world.