Floating oil seals, often recognized as duo cone seals, are crucial components in the sphere of heavy machinery, providing robust sealing solutions to prevent the ingress of harsh contaminants and the egress of essential lubricants. Their innovative design is meticulously crafted to meet the demands of strenuous working environments, offering unparalleled durability and reliability.
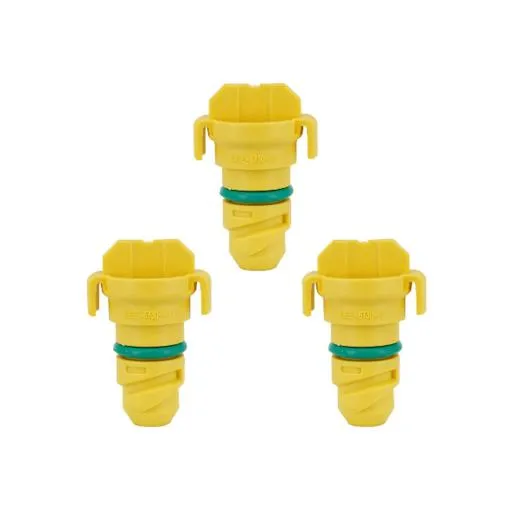
The construction of floating oil seals involves two primary components hard metal rings and elastomeric components. The metal rings are generally composed of high-quality, wear-resistant cast iron or steel, providing the resilience required to withstand extreme operating conditions. Complementing these are the elastomeric elements, typically forged from nitrile rubber or silicone, tailored for flexibility and to accommodate thermal expansion.
One key advantage of floating oil seals is their ability to function across a wide temperature spectrum. In industries such as mining, construction, and agriculture, machinery often operates under severe thermal conditions. Herein lies the expertise of floating oil seals their flawless performance is guaranteed in temperatures ranging from the icy -40°C to the blistering 200°C. This adaptability ensures machinery maintains peak performance without the frequent need for maintenance or replacement, enhancing operational efficiency and reducing downtime.
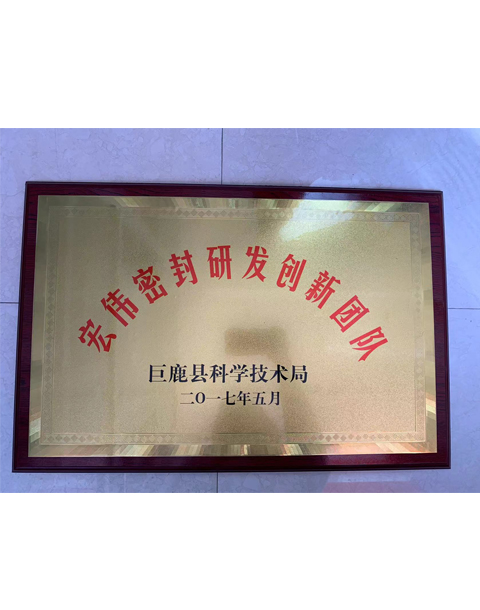
The reliability of floating oil seals can be attributed to their minimalistic design that requires no further lubrication once installed. This not only saves costs over time but also adds an extra layer of environmental protection by minimizing oil leakage. In the competitive market space, companies that employ these seals often report a drastic reduction in equipment failure, asserting the authoritativeness of these seals in ensuring machinery longevity.
floating oil seal
Moreover, the installation process of floating oil seals is straightforward, demanding no sophisticated tools, thereby increasing trustworthiness in fields where operational speed is crucial. The self-lubricating feature marks them as an ideal choice for equipment where accessibility and regular maintenance are challenging. For end-users, this translates to superior peace of mind, knowing that their machinery can continuously function under optimal conditions with minimal intervention.
Floating oil seals also substantially contribute to cost-efficiency. Their longevity and low-maintenance nature often result in a significant reduction in the total cost of ownership. Businesses that prioritize long-term investments in reliable machinery components find floating oil seals an indispensable asset, underscoring their expertise in identifying durable and trustworthy solutions.
In testimonial reviews and field studies, floating oil seals have consistently proven their mettle. Operators across various industries vouch for their ability to maintain high performance levels in unforgiving environments. Such hands-on experience underscores their authenticity and builds a compelling case for businesses seeking to enhance the reliability of their operations.
In conclusion, floating oil seals stand as a testament to engineering ingenuity. Their ability to provide sustainable sealing solutions with minimal maintenance solidifies their reputation as essential components in the arsenal of heavy machinery. When considering investment in machine parts, floating oil seals invariably emerge as the premier choice for those who value experience, expertise, authoritativeness, and trustworthiness. The exceptional performance of these seals confirms their role as a cornerstone in achieving operational excellence, offering industries a reliable pathway to sustained mechanical integrity.