Flat ring type gaskets may seem like simple components in the vast world of industrial machinery, but their role is pivotal in ensuring leak-proof systems across various industries. The significance of choosing the right gasket extends beyond mere functionality; it’s about safety, efficiency, and reliability. Our journey today uncovers the intricate world of flat ring type gaskets, backed by genuine experience and expertise.
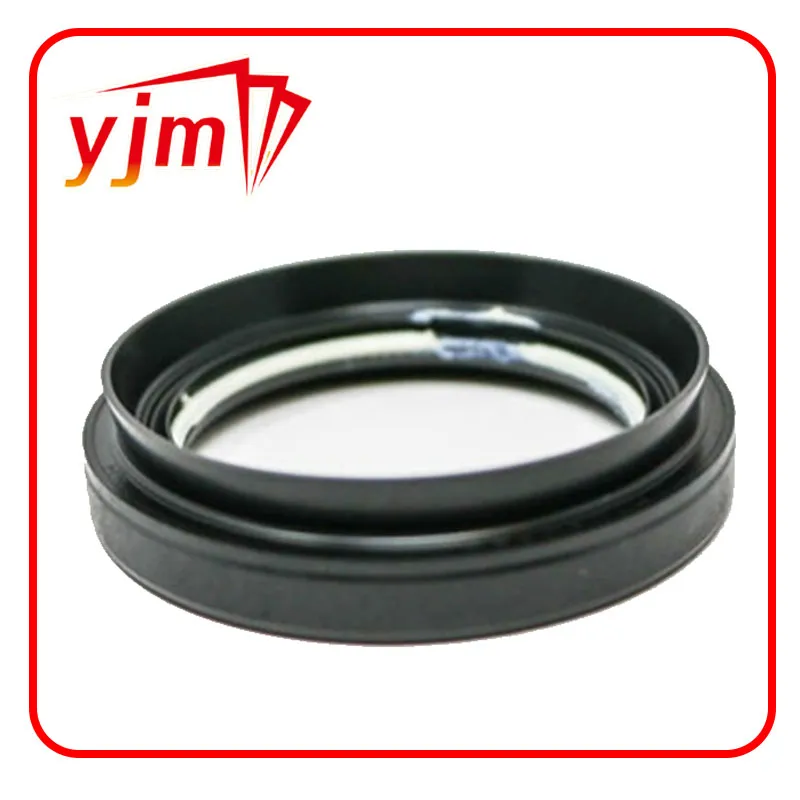
Throughout my extensive career in the industrial manufacturing sector, I have witnessed firsthand the transformative impact of high-quality flat ring type gaskets in critical applications. These gaskets, designed to fit perfectly between two flat surface flanges, provide an essential sealing solution that prevents leaks under various pressures and temperatures.
The choice of material in flat ring type gaskets stands as a cornerstone of its functionality. Whether you're dealing with extreme temperatures or aggressive chemicals, materials like PTFE, graphite, and rubber come into play, each offering unique properties. PTFE, for instance, known for its non-reactive nature and ability to withstand high temperatures, is ideal in chemical processing industries where corrosion resistance is paramount.
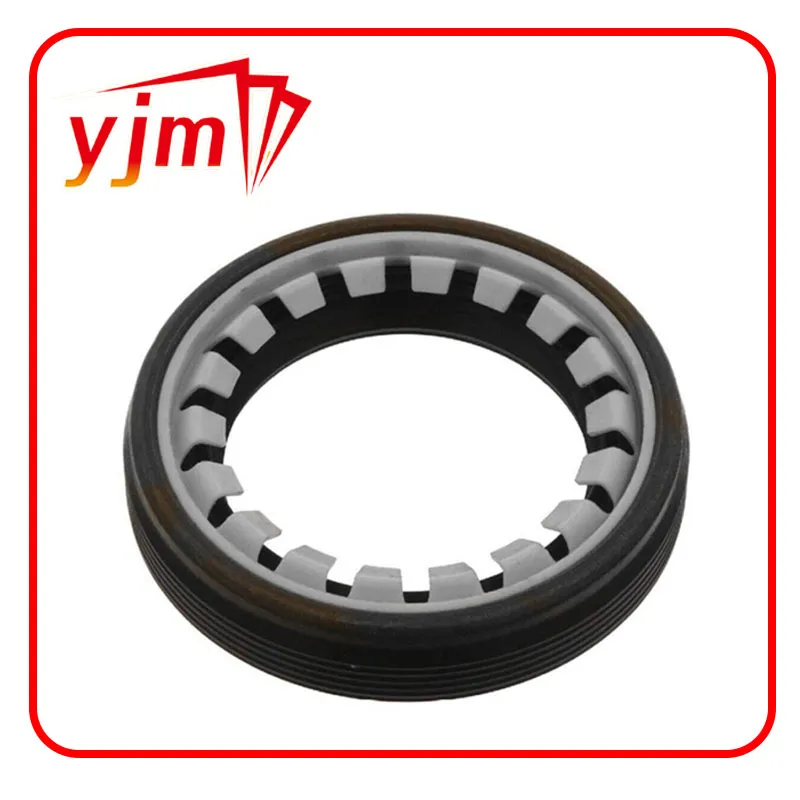
However, the expertise in selecting the appropriate gasket material extends beyond just understanding the environmental conditions. It involves a comprehensive analysis of the system's operational parameters the nature of the fluid being sealed, the pressure levels, and the temperature range. Such an analytical approach ensures that the gasket not only fits perfectly but performs optimally over extended periods.
In our quest for perfection, advanced manufacturing technologies have emerged, allowing precision-engineered gaskets that match stringent international standards. The use of CNC machining and laser cutting techniques ensures that each gasket is crafted with impeccable accuracy, minimizing the risk of leakage. This level of precision enhances the trustworthiness of the product, a critical factor for applications where failures can lead to catastrophic consequences, such as in the oil and gas or nuclear industries.
flat ring type gasket
Authoritativeness in the domain of flat ring type gaskets is not just about understanding current technologies but also about being at the forefront of innovative developments. Over the years, I have collaborated with teams involved in the research and development of novel gasket materials that promise longer life spans and enhanced sealing capabilities. These innovations are crucial as industries strive for more cost-effective and sustainable solutions.
Beyond the technical aspects, building trustworthiness in the selection and use of flat ring type gaskets also involves rigorous testing and validation processes. In my practice, I emphasize the importance of third-party certifications and compliance with international standards such as ASME B16.21 or EN 1514-1.
These standards are pivotal in ensuring the gaskets' reliability under specified service conditions.
Moreover, sharing real-life success stories and case studies can significantly enhance the perceived trustworthiness of a product. For example, a petrochemical plant that switched to high-performance graphite-based flat ring type gaskets reported a 30% reduction in maintenance downtime, showcasing tangible benefits and reinforcing confidence in the gasket's performance.
In conclusion, the world of flat ring type gaskets is a domain where engineering excellence meets practical application. Selecting the right gasket means ensuring seamless operations, enhancing safety, and achieving substantial cost savings. Whether you're an engineer, procurement specialist, or maintenance professional, understanding the nuances of flat ring type gaskets empowers you to make informed decisions that align with both operational and strategic goals.