Oil seal retainers play a crucial role in maintaining the integrity and functionality of machinery across various industries. These components, designed to hold oil seals securely in place, prevent leakage and ensure the smooth operation of mechanical systems. With the growing demand for efficient and durable machinery, it is essential to understand the significance of opting for high-quality oil seal retainers.
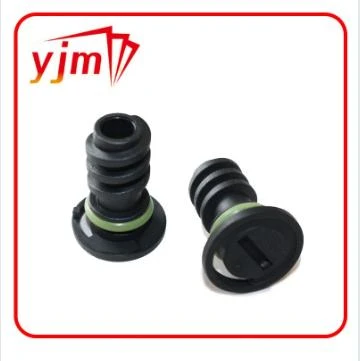
Expertise in the manufacturing and application of oil seal retainers is vital for ensuring machinery operates at peak efficiency. The retainer's primary function is to support the oil seal, allowing it to keep lubricants within machinery and contaminants out. This capability is particularly important in engines, gearboxes, and hydraulic systems where even a slight oil leak can lead to significant performance losses or equipment failure. The precision in the design and production of these retainers ensures they fit perfectly with the corresponding oil seals, maintaining a reliable environment for optimal mechanical function.
Authoritativeness in how oil seal retainers are discussed in the industry emphasizes the importance of materials and design. Retainers can be made from various materials, including metal, rubber, and composites, each offering distinct advantages depending on the operating conditions. For instance, metal retainers provide enhanced durability and are ideal for high-temperature applications, while rubber retainers allow for flexibility and shock absorption. An authoritative approach also includes knowledge of different seal configurations, such as rotary, reciprocating, or static, and how these configurations influence the choice of retainer.
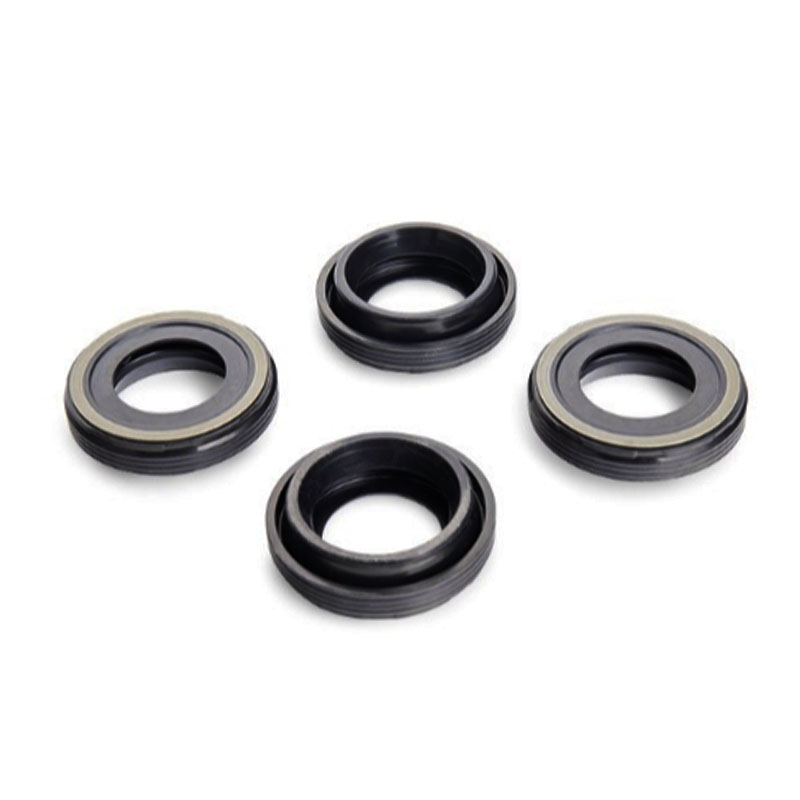
Experience in selecting the right oil seal retainer is an invaluable asset for anyone involved in equipment maintenance or manufacturing. Those with experience can assess the specific requirements of an application, such as temperature range, pressure conditions, and chemical exposure, to choose the optimal retainer. Moreover, they can provide insights into common issues like retainer fatigue or improper installation that can compromise machinery performance. Addressing these potential pitfalls with preventive maintenance strategies and proper installation techniques can extend the lifespan of both retainers and seals.
oil seal retainer
Trustworthiness stems from relying on reputable manufacturers and suppliers with a proven track record of quality and safety. The credibility of an oil seal retainer is often determined by adherence to industry standards and rigorous testing for performance under real-world conditions. Reliable suppliers offer transparency regarding the materials and production processes used, assuring customers of the retainer's reliability and suitability for their specific needs. Additionally, they provide comprehensive support and technical assistance, reinforcing the customer’s confidence in the products they choose.
For businesses reliant on machinery, investing in top-tier oil seal retainers can significantly enhance the longevity and efficiency of their operations. By incorporating knowledge-driven choices regarding their design, material, and application, companies can avert costly downtimes and extend the service life of their equipment. As machinery continues to evolve and operate under more demanding conditions, the role of oil seal retainers as an integral component of mechanical reliability becomes even more pronounced.
Selecting the right oil seal retainer transcends simple component replacement; it is vital to achieving operational excellence and safeguarding critical infrastructure. Understanding the nuanced interactions between oil seals and retainers can empower maintenance teams and engineers to make informed, strategic decisions that propel productivity and efficiency across industries.