Oil seal manufacturing is both an art and a science, demanding a balance of precision, materials expertise, and cutting-edge technology. In industries where machinery efficiency and longevity are paramount, the role of oil seals becomes increasingly vital. These components are not merely mechanical buffers; they are crucial protectors against contamination and facilitators of performance efficiency.
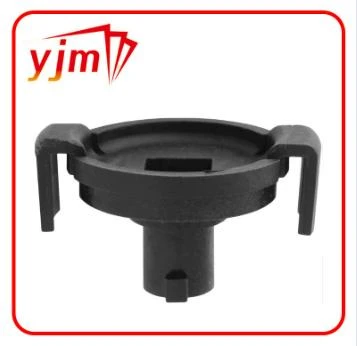
High-quality oil seals are the unsung heroes within the mechanical world. Their primary function is to prevent the escape of lubricants and halt the ingress of contaminants. This seemingly simple duty requires immaculate geometric precision and material resilience. For over three decades, our manufacturing facility has dedicated itself to perfecting the manufacture of these mechanical masterpieces.
The oil seal production journey begins with understanding material science. Nitrile rubber, fluorocarbon, and polyurethane are just a few of the materials we use, each selected for its unique properties. Nitrile rubber, for example, offers excellent resistance to petroleum-based oils and fuels, making it ideal for applications involving extensive interaction with hydrocarbons. On the other hand, fluorocarbon seals are designed to withstand higher temperatures and harsh chemicals, offering durability in more aggressive environments. With a keen eye on material innovation and environmental sustainability, our materials experts continuously experiment and develop advanced composites that extend the lifespan of oil seals and enhance their sealing capabilities.
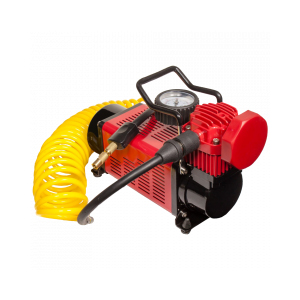
In addition to material selection, our expertise extends to advanced design facilities, where synthetic simulations are used to predict operational stress and performance longevity. Each oil seal is subjected to rigorous testing procedures, employing our proprietary technology that simulates real-world operating conditions. This method ensures that each batch of oil seals complies with both industry standards and the customized requirements of our clients. Our clients, ranging from automotive giants to industrial equipment manufacturers, trust us to deliver reliable components that align with their precise engineering specs.
oil seal manufacturing
Moreover, we pride ourselves on investing in state-of-the-art production technology. CNC machines, high-precision mold manufacturing, and automated assembly lines not only enhance production efficiency but also maintain quality consistency across products. In participation with academia, we've developed enhanced sealing technologies that incorporate self-lubricating membranes, reducing friction and wear.
Transparency and trust underlie our business philosophy. Through open dialogue with clients, performance insights, and reliability assessments, we aim to establish lasting partnerships. Customer visits are welcomed, offering them an inside look into our rigorous production processes and quality checkpoints.
In conclusion, oil seal manufacturing demands an intricate dance between material science, technology, and human expertise. Our commitment, fortified by years of experience, empowers us to deliver products with unmatched performance and longevity. This dedication cements our position as leaders in the industry, continually pushing the boundaries of what precision engineering can achieve for our diverse clientele worldwide.