Choosing the right oil seal for your machinery can be a daunting task, especially when precision and durability are paramount. The 80x100x10 oil seal serves as an ideal choice for a variety of applications where these specifics are concerned. As someone who has spent years in the field of machinery maintenance and optimization, I've come to appreciate the vital role oil seals play in ensuring equipment longevity and performance.
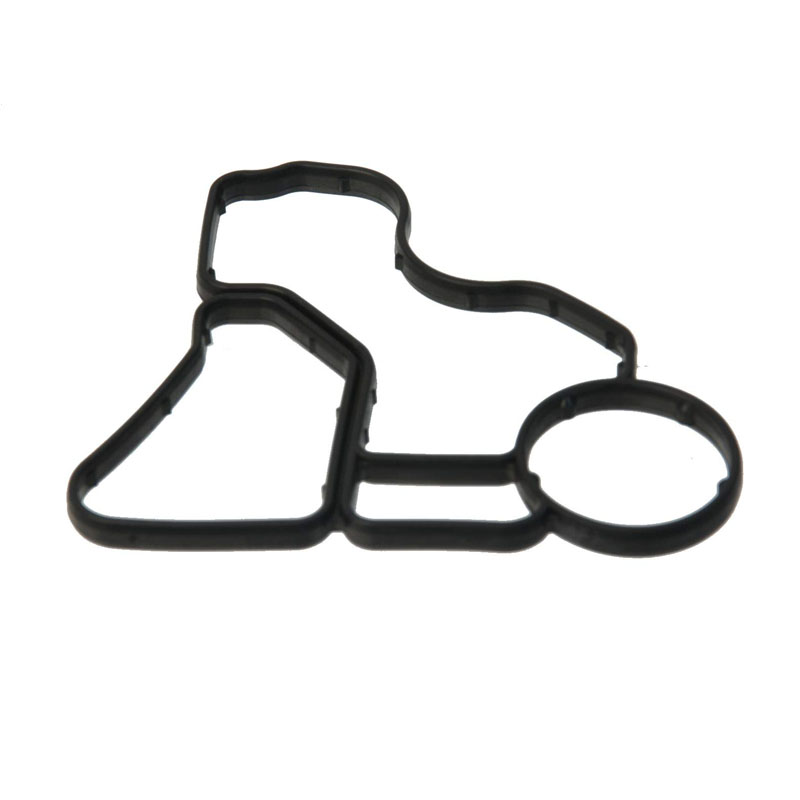
Oil seals, especially the 80x100x10 type, are not merely rubber rings but crucial components that prevent oil leakage and maintain an efficient lubrication system within machinery. An oil seal’s primary function is to separate components in rotary motion while maintaining essential lubrication, preventing dust and contaminants from entering the system.
The 80x100x10 size is specifically designed to fit perfectly in compatible machinery, ensuring that it aligns accurately with the shafts and housings it is intended for.
From my expertise, an 80x100x10 oil seal is not only significant for its dimensional attributes but also for the material composition it comes in. High-quality oil seals are typically crafted from durable materials such as Nitrile Rubber (NBR), Viton, or Silicone, each offering distinct advantages based on the operational environment. NBR is renowned for its resistance to wear and compatibility with a wide range of temperatures. On the other hand, Viton is exceptional for high thermal resistance and chemical stability, making it preferable in environments with extreme temperature fluctuations or exposure to chemicals. Silicone seals provide excellent performance in varying temperature conditions but are utilized where less chemical exposure is expected.
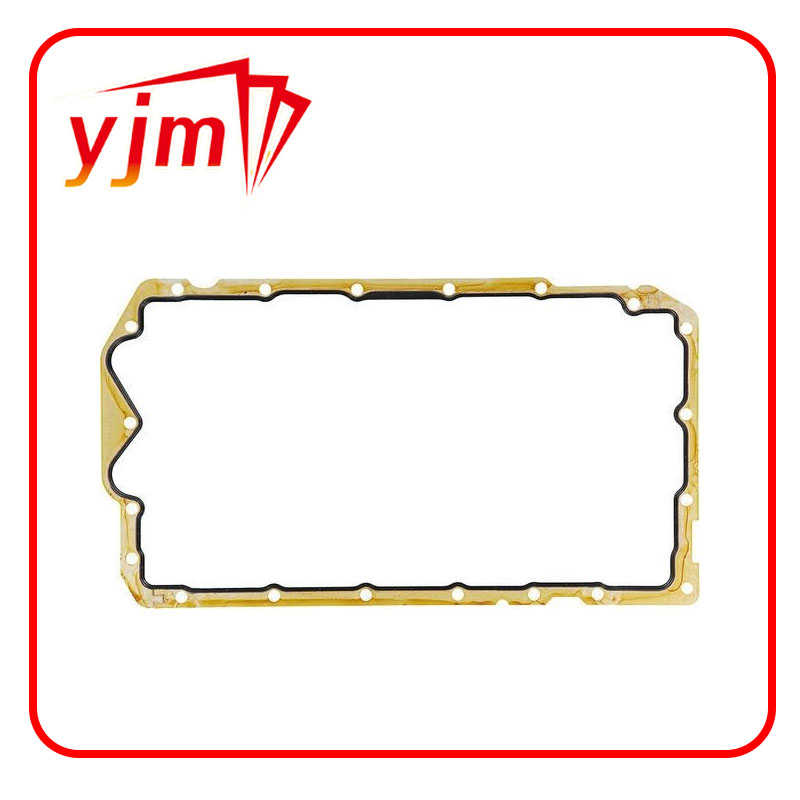
Understanding your machinery’s operating conditions is critical when selecting an 80x100x10 oil seal. Machinery that operates continuously or at high rotations per minute (RPM) benefits from seals made from materials resistant to wear under high-speed conditions. Furthermore, ensuring that seals are compatible with the lubricants being used can prevent premature seal failure.
80x100x10 oil seal
Authoritativeness in selecting an 80x100x10 oil seal also involves assessing the seal manufacturing standards. Reputable manufacturers often adhere to rigorous manufacturing protocols, and their products come with certifications that authenticate the seals' quality and reliability. Opting for seals from such manufacturers can mitigate risks associated with seal failures, which could lead to significant downtime and repair costs.
In my professional experience, a trusted oil seal supplier will also offer detailed testing and analysis reports. This assurance guarantees that the 80x100x10 oil seals have undergone comprehensive testing for pressure endurance, thermal resistance, and elasticity. Engaging with suppliers who provide in-depth documentation elevates trust, ensuring that the seals you invest in are genuine and capable of performing under specified conditions.
To sum up, when deciding on an 80x100x10 oil seal, leverage your choice on both empirical analysis and proven expertise. Engage with suppliers who exhibit a robust understanding of material properties, manufacture adhering to the highest standards, and offer tangible documentation on product reliability. These steps cultivate an environment where machinery operates efficiently, reducing the risks of catastrophic failures and ensuring long-term operational success. Selecting the right oil seal is as much about understanding the technical specifications as it is about building relationships with authoritative suppliers in the industry.