In the bustling world of machinery and mechanical engineering, the relevance of oil seals cannot be overstated, and when it comes to the specific category of oil seals - particularly the 20 30 7 oil seal - understanding its unique properties and applications unlocks a new dimension of mechanical efficiency and safety. These small, yet mighty components are crucial in preventing leakage and contamination, ensuring that machinery operates smoothly, effectively maximizing longevity and performance.
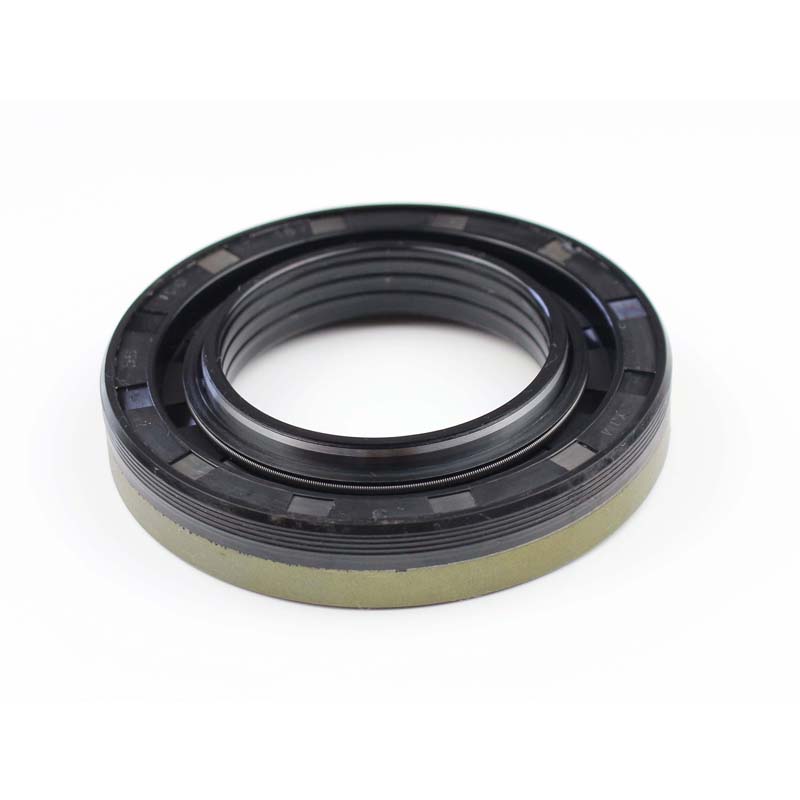
Firstly, let's delve into the specifications of a 20 30 7 oil seal. These numerals aren't arbitrary; they signify the dimensions of the oil seal. The '20' stands for the inner diameter of 20 millimeters; this is where the oil seal makes contact with a shaft. The '30' refers to the outer diameter, measuring 30 millimeters, which interacts with the housing bore. Lastly,
'7' is the width in millimeters. These precise measurements ensure that the seal fits snugly, facilitating its primary function of preventing lubricant leakage.
A real-world experience demonstrates that using an appropriately sized oil seal is critical in various industrial settings, from automotive to factory machines. Consider a manufacturing plant operating several assembly lines around the clock. Each machine relies on hydraulic systems heavily lubricated to reduce friction and prevent overheating. Here, the 20 30 7 oil seal is essential in maintaining the integrity of the lubrication system, ensuring fluid remains within while contaminants such as dust and moisture are kept at bay. Plant managers often share testimonials indicating substantial reductions in maintenance downtime owing to high-quality oil seals.
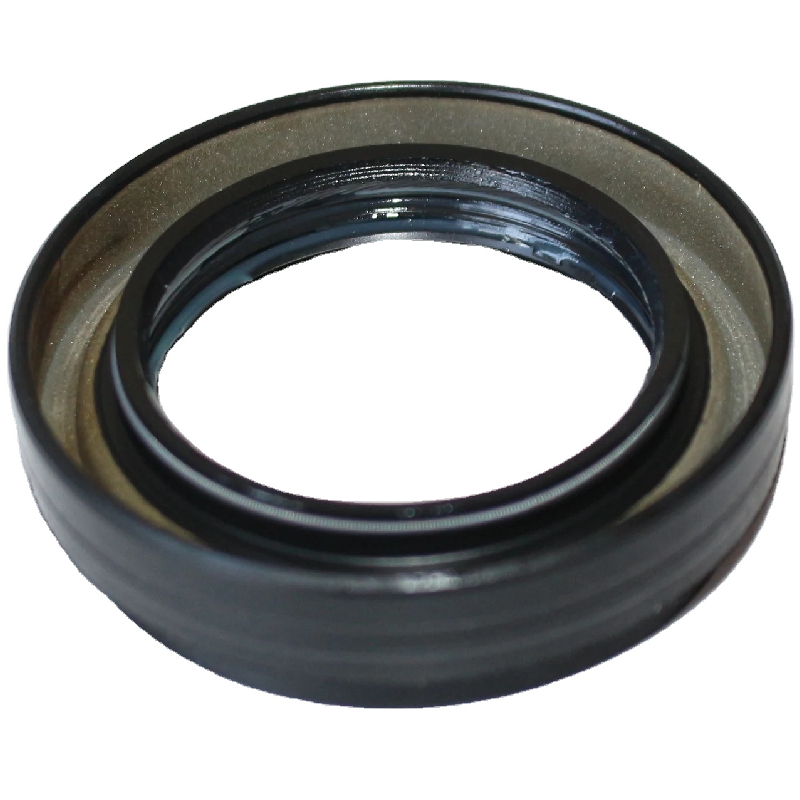
From an expertise perspective, the 20 30 7 oil seal typically comprises high-grade materials, such as nitrile rubber or Viton, chosen for their resilience and resistance to wear and environmental factors. These materials play a crucial role in extending the life of the oil seal under challenging conditions, such as extreme temperatures and corrosive substances, frequently encountered in mechanical operations. Mechanical engineers emphasize the importance of selecting the right material based on the operational environment to prevent premature seal failure.
20 30 7 oil seal
Authority in this field is established through understanding and adhering to international standards such as ISO standards for oil seals. These standards ensure that oil seals meet design and quality assurance criteria, which in turn instills confidence among industry professionals. A 20 30 7 oil seal conforming to these standards guarantees performance consistency, which is why reputable manufacturers seek certifications that reflect these rigorous benchmarks.
The trustworthiness of a 20 30 7 oil seal also depends on rigorous testing under simulated real-world conditions. Comprehensive evaluations, from pressure testing to durability assessments, provide critical insights into a seal's performance capabilities. Documented test results and endorsements from third-party quality assurance organizations further enhance the credibility of these components. In practical terms, utilizing an oil seal from a manufacturer known for extensive testing means fewer unexpected failures and maintenance interventions, thus providing peace of mind to end-users.
In conclusion, the 20 30 7 oil seal represents a pinnacle of practical engineering design, blending precision with reliable materials and backed by stringent standards. For businesses and operations that hinge on mechanical efficiency, investing in high-quality oil seals translates into a tangible competitive advantage. Trustworthy manufacturers will proudly share their expertise in oil seal production, offering not only products but also educational insights for optimal use and longevity. As industrial machinery continues to evolve, the strategic deployment of superior oil seals remains a cornerstone of operational success.