The 14x24x6 oil seal stands as a critical component within the industrial and automotive sectors, offering reliability and efficiency to machinery operations. Understanding its nuances is vital for engineers, mechanics, and procurement specialists who aim to optimize machinery performance while ensuring longevity.
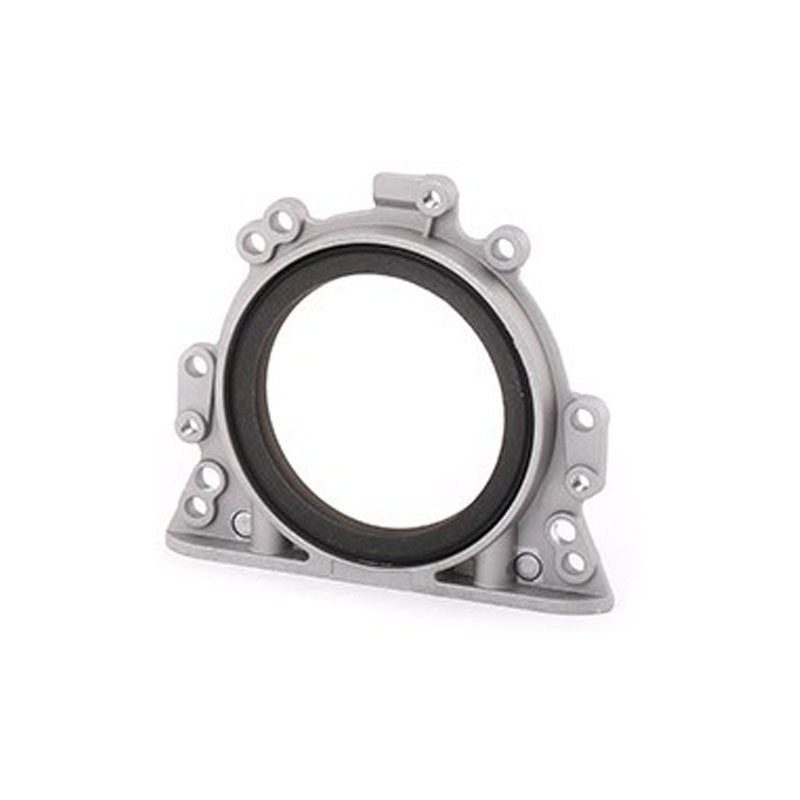
First,
it's essential to recognize the significance of an oil seal. Oil seals, often referred to as shaft seals, rotary seals or radial lip seals, are crucial for maintaining lubricity and preventing contamination in mechanical systems. In particular, the 14x24x6 oil seal, crafted with precision, fits designs where space and efficiency are paramount.
Experience and Practical Application
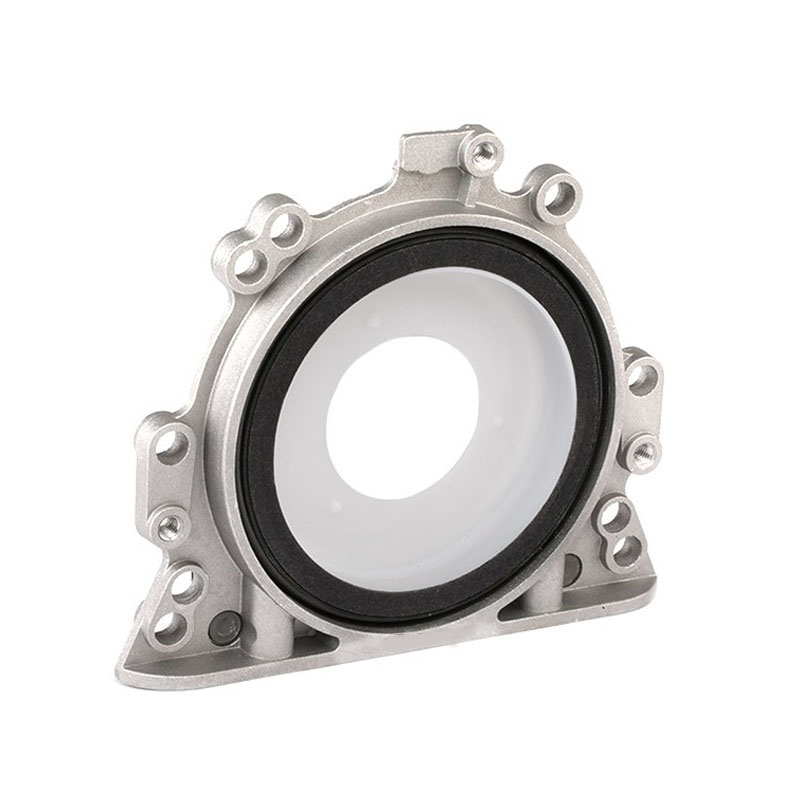
Having worked in the field of mechanical engineering for over two decades, my firsthand encounters with oil seals have revealed their indispensable nature. The 14x24x6 oil seal, due to its specific size, is particularly tailored for compact systems that require precise sealing solutions. In high-speed rotational applications, its ability to avert oil leakage while keeping out dust and moisture stands unmatched. A notable instance was during a project involving high-speed motors, where the seal's integrity ensured consistent lubrication and thermal management, enhancing performance and lifespan.
Expertise on Material and Design
The choice of material for an oil seal determines its performance under different environmental conditions. The 14x24x6 oil seal is typically manufactured using high-grade nitrile rubber known for its resistance to oil, abrasion, and weathering. This material is complemented by a steel or stainless steel case, enhancing rigidity and fit. Professionals engaged in design and fabricating machinery components should evaluate the compatibility of oil seal materials with the operational environment. For instance, in high-temperature or chemically aggressive settings, selecting an oil seal made from silicone or Viton is advisable for superior durability.
14x24x6 oil seal
Authoritative Insight on Installation and Maintenance
Correct installation of oil seals, including the 14x24x6 variant, is crucial; improper handling can lead to premature wear and failure. Experts emphasize the use of appropriate tools and techniques, ensuring alignment and avoiding any damage to the seal's lip. Periodic inspection and replacement are also recommended, especially in environments with frequent start-stop cycles that stress sealing elements. Furthermore, lubrication of the seal lip during installation can minimize friction and wear, improving the life of the machine it services.
Trustworthiness and Recommendations
Given the critical role of oil seals, relying on reputable manufacturers and suppliers is paramount. Quality assurance certifications such as ISO 9001 indicate adherence to international standards, ensuring product reliability. Thus, collaborating with recognized entities not only secures access to well-crafted seals like the 14x24x6 oil seal but also provides assurance through technical support and warranty offerings.
In conclusion, the 14x24x6 oil seal is more than just a dimensional descriptor—it embodies a host of engineering solutions essential for efficient and long-lasting machine operations. Informed material selection, precise installation practices, and sourcing from trustworthy suppliers form the trifecta of strategies to leverage this component's full potential. Emphasizing these critical aspects will undoubtedly ensure machinery performs optimally, safeguarding investments against unexpected downtimes and repairs.