Understanding Shaft Seals by Size A Comprehensive Guide
In the world of mechanical engineering, shaft seals play an indispensable role in preventing fluid or gas leakage and maintaining system efficiency. These seals come in various sizes, each designed to accommodate specific shaft dimensions and operating conditions. This article delves into the significance of shaft seals by size, their types, and how they contribute to overall machinery performance.
A shaft seal, also known as a gland pack or stuff box, is a device that prevents leakage along a rotating shaft. It is a critical component in pumps, compressors, turbines, and other equipment where fluids or gases need to be contained. The size of the shaft seal is a determining factor in its effectiveness, as it ensures a proper fit and optimal sealing performance.
Firstly, let's discuss the standardization of shaft seal sizes. In most industrial settings, shaft seals follow standardized dimensions based on international standards like ISO, ANSI, or DIN. These standards ensure compatibility across different manufacturers and simplify the procurement process. For instance, an ISO 6194 compliant shaft seal will have specific dimensions for the inner diameter, outer diameter, and width, which are compatible with shafts meeting the same standard.
When selecting a shaft seal by size, it is essential to consider the shaft diameter. Smaller seals are typically used in applications with compact machinery or low-pressure systems, while larger seals are employed in high-pressure, heavy-duty operations. Oversized seals may lead to excessive friction, causing premature wear, while undersized seals can result in leaks and reduced system efficiency Oversized seals may lead to excessive friction, causing premature wear, while undersized seals can result in leaks and reduced system efficiency
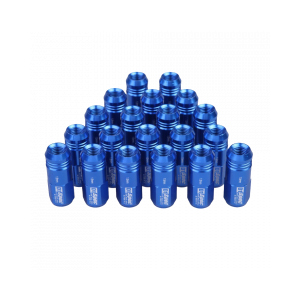
Oversized seals may lead to excessive friction, causing premature wear, while undersized seals can result in leaks and reduced system efficiency Oversized seals may lead to excessive friction, causing premature wear, while undersized seals can result in leaks and reduced system efficiency
shaft seals by size.
There are several types of shaft seals, each designed for specific sizes and applications. Lip seals, also called oil seals, are commonly used for smaller shafts in automotive and light industrial applications. They consist of a rubber-like material that forms a barrier around the shaft. On the other hand, mechanical seals, which are more complex and suitable for larger shafts, involve two mating faces that prevent leakage by maintaining contact under pressure.
Cartridge seals are another type, available in various sizes, offering the advantage of easy installation without requiring specialized tools or machining. They are often used in pumps and agitators where quick seal replacement is necessary.
In addition to size, factors such as temperature, pressure, and chemical compatibility must be considered when choosing a shaft seal. High-temperature environments may require heat-resistant materials, while harsh chemicals necessitate seals made from resistant elastomers or metal components.
In conclusion, understanding shaft seals by size is crucial for ensuring optimal performance, preventing leaks, and maintaining machinery integrity. Proper sizing not only enhances the seal's lifespan but also contributes to overall system efficiency and reliability. Engineers and maintenance professionals should always consult manufacturer specifications and industry standards to make informed decisions when selecting the right shaft seal for their application.