Oil Seal A Crucial Component in Machinery Performance
Oil seals are integral components in the operation of machinery, serving as barriers that prevent the leakage of fluids and the ingress of contaminants. These vital devices maintain the integrity of hydraulic systems, gearboxes, transmissions, and other critical mechanisms, ensuring their optimal performance and extending their service life.
The primary function of an oil seal is to create a tight seal between two moving parts, such as a shaft and housing, while allowing for relative motion. This is achieved through the use of a flexible material, such as rubber or synthetic elastomers, which conforms to the surface of the moving part and creates a seal. The seal is designed to withstand high pressures, temperatures, and speeds, making it an essential component in high-performance machinery.
One of the key factors that determine the effectiveness of an oil seal is its material composition. Different materials have different properties, such as hardness, elasticity, and resistance to wear and tear. For example, silicone rubber is known for its,。,。
Another important consideration is the design of the oil seal. The shape, size, and material of the seal, as well as the method of installation, can all affect its performance The shape, size, and material of the seal, as well as the method of installation, can all affect its performance
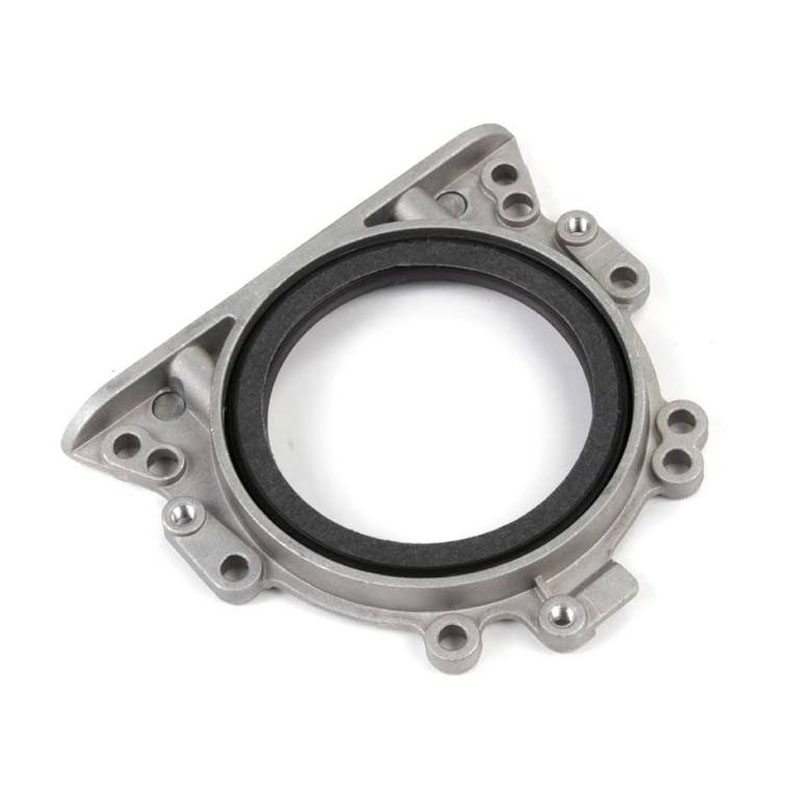
The shape, size, and material of the seal, as well as the method of installation, can all affect its performance The shape, size, and material of the seal, as well as the method of installation, can all affect its performance
oil seal 20 35 7. For instance, a lip seal, which consists of a flexible lip that contacts the surface of the moving part, is commonly used in applications where there is a risk of contamination. A radial shaft seal, on the other hand, provides a complete barrier around the shaft and is often used in high-pressure environments.
Regular maintenance and inspection are crucial to ensuring the longevity and effectiveness of oil seals. Dirt, debris, and wear can all compromise the seal's ability to perform its duties, leading to leaks and other issues. Therefore, it is important to check the seal for signs of damage or wear and replace it as necessary.
In conclusion, oil seals are indispensable components in modern machinery, providing a critical line of defense against fluid leakage and contamination. By selecting the right material and design, and performing regular maintenance, engineers can ensure the reliable performance of these vital devices.