TC oil seals play a crucial role in mechanical systems by preventing the leakage of lubricants and the ingress of contaminants. As industries continue to push the envelope in terms of efficiency and performance, the specificity and quality of these seals become increasingly vital. Having been in the field of mechanical engineering for over two decades, I've observed the evolution of oil seals firsthand and how they have adapted to meet contemporary requirements.
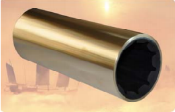
These seals are typically used in contexts where rotational motion is a key component, such as in pumps, engines, and gearboxes. They need to withstand harsh operating environments, enduring varying temperatures, pressures, and exposure to chemicals. Expertise in material science, therefore, becomes essential to their design and manufacture. Advanced materials like Viton, nitrile rubber, and silicone are frequently employed to give TC oil seals their durability and flexibility. Choosing the right material becomes a balancing act; it must be resistant enough to endure operational stress but not so rigid that it loses its sealing capabilities.
Professional experience has shown that the installation of TC oil seals is as critical as their material and design. Any improper handling or misalignment during installation can lead to premature failure. A common mistake observed in the field is neglecting the proper cleaning and inspection of the shaft and housing before installation. Ensuring these surfaces are smooth and free of contaminants can significantly increase the lifespan of the seal. Applying the correct installation tools and techniques, such as using an installation sleeve and lubricant, minimizes the risk of damaging the sealing lip.
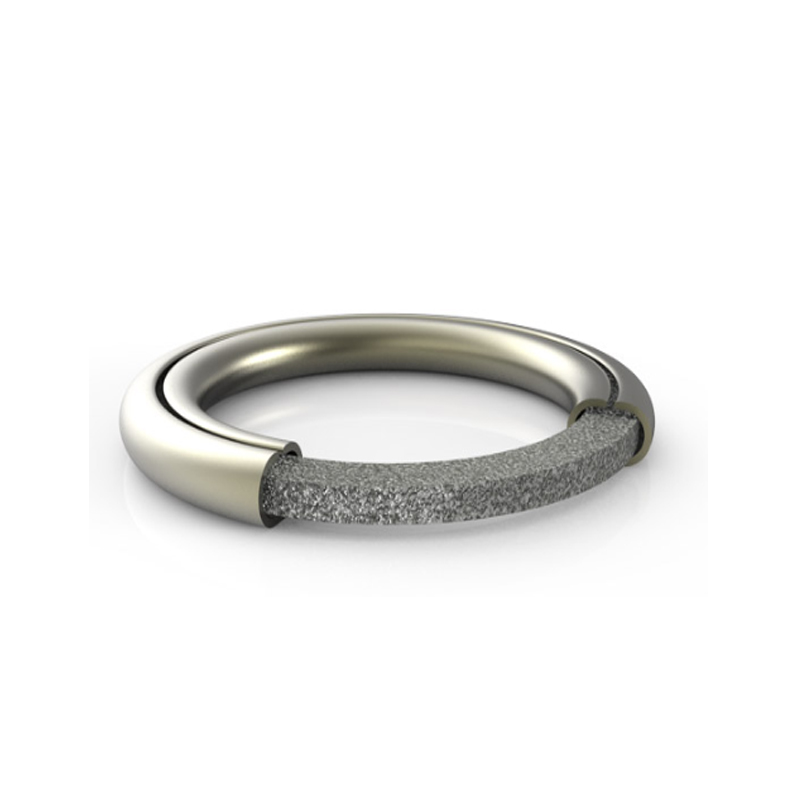
tc oil seal
Authoritative sources in mechanical engineering suggest a comprehensive understanding of the operating environment to choose the appropriate TC oil seal. This involves calculating the pressure differentials it will encounter and the type of fluid it will interact with. Using empirical data and simulations, engineers can design seals tailored to specific operations, thereby maximizing efficacy. Such expertise allows for predictive maintenance and reduces downtime, a significant cost-saving factor in industrial applications.
Trust is also an essential element in the ecosystem of TC oil seals. Manufacturers must maintain stringent quality control processes to ensure each seal performs to its specifications. Regular audits and certifications by independent bodies can bolster confidence in their product lines. Additionally, offering warranties and support services are indicative of a manufacturer's commitment to quality and customer satisfaction. Having a robust after-sales support system ensures that any issues that arise can be quickly addressed, minimizing operational disruptions.
In conclusion, the importance of TC oil seals cannot be overstated in contemporary mechanical systems. They are critical components that safeguard the integrity of complex machinery. As industries strive for greater efficiencies, the demands on these seals will only grow. Thus, a deep understanding of their material properties, installation techniques, and operational environments is indispensable. By aligning expertise with evolving technological demands and maintaining trust through quality and support, professionals can ensure the optimal performance and longevity of TC oil seals.