Sump plug crush washers are an often underestimated component within the realm of automotive maintenance. As an automotive enthusiast with years of hands-on experience and a dedication to educating others in this field, I've observed the significant impact a simple crush washer can have on an engine's oil retention and overall performance.
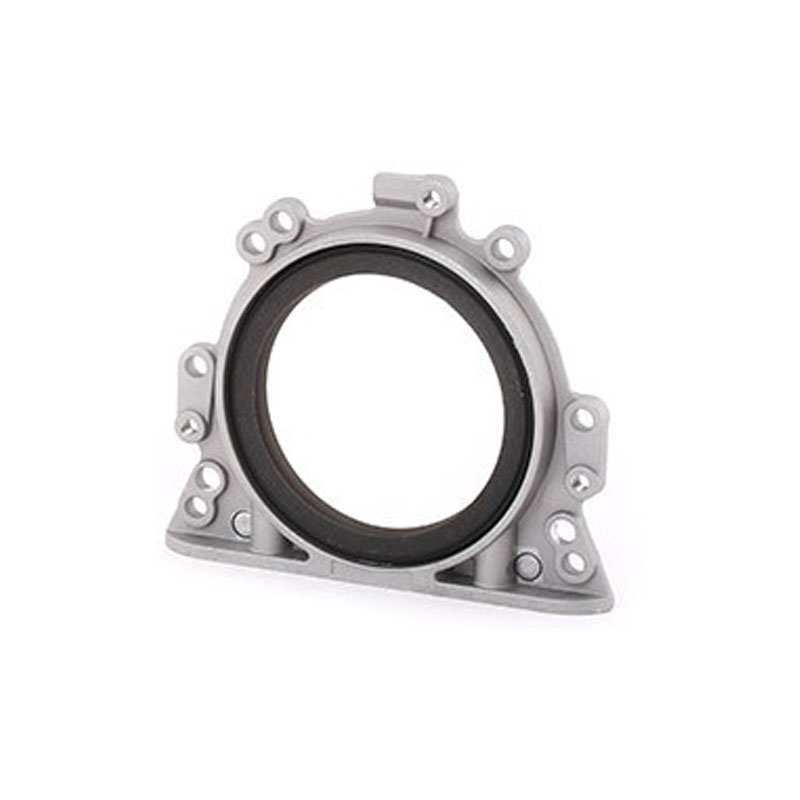
A crush washer, typically made from copper, aluminum, or composite materials, serves as a gasket between the oil drain plug and the oil pan. Its primary function is to provide a leak-proof seal, preventing the oil from seeping through the threads and escaping the sump. While this might seem trivial at first glance, the efficiency of this small component is crucial to the health of your engine.
From a technical standpoint, when you torque down the sump plug,
the crush washer deforms under pressure. This deformation allows it to fill any existing gaps or irregularities on the surfaces it interfaces, ensuring a snug fit. The material choice for these washers is equally significant; metals like copper and aluminum are preferred due to their ability to provide a strong seal while being malleable enough to conform under pressure.
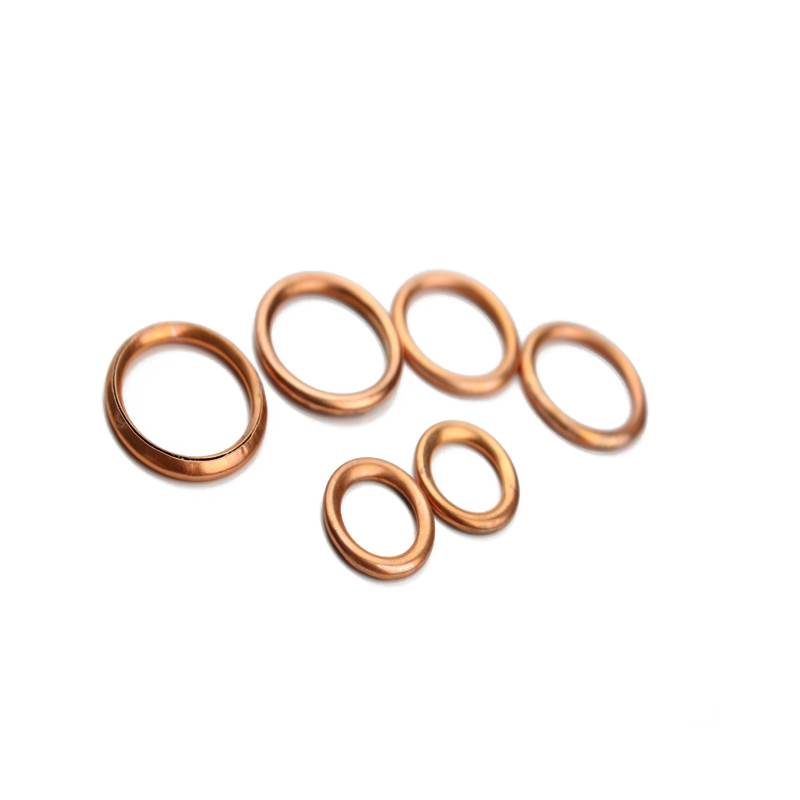
A common oversight among vehicle owners is neglecting to replace the crush washer during every oil change. Many might argue the inconvenience or cost of a replacement is unnecessary, especially if no leaks have been observed. However, from an expert perspective, this is a misguided approach. Over time, these washers lose their malleability and sealing effectiveness due to repeated usage and exposure to varying temperatures. Reusing a crush washer can lead to insufficient sealing, resulting in oil leaks that could escalate into more severe engine issues if left unaddressed.
sump plug crush washer
I recall a particular instance at my garage where a client brought in his mid-sized sedan complaining about a mysterious underhood odor after his DIY oil change. Upon inspection, we discovered that he had reused the old crush washer, which had become flattened and compromised. The leakage, albeit minor at first, had gradually spread, allowing oil to drip onto the exhaust, causing the unpleasant smell. This scenario underscores the necessity for replacing crush washers as part of routine maintenance.
The cost of a new crush washer is negligible compared to the potential expense from an undetected oil leak. Ensuring proper installation involves not only replacing these washers but also using a torque wrench to secure the sump plug to the manufacturer's specified torque. Over-tightening can crush the washer beyond its ability to return to its original state, while under-tightening may fail to provide a sufficient seal.
Car manufacturers often provide specific recommendations on washer material and tightness in service manuals. Adhering to these guidelines is essential to maintain not only the oil system's integrity but also to preserve warranty conditions and the longevity of the vehicle.
In conclusion, the sump plug crush washer is a testament to the idea that sometimes the smallest components hold the most significant responsibilities. As someone seasoned in automotive maintenance, I urge vehicle owners, especially those who prefer doing their own oil changes, to prioritize the seemingly insignificant act of replacing this washer. It's a practice that embodies professionalism, expertise, and a commitment to preserving the trustworthiness of the machinery that gets us from point A to point B reliably and safely. Neglecting this simple step not only risks the vehicle’s performance but also undermines the meticulous engineering that goes into these complex machines. Through understanding and applying these principles, automotive enthusiasts can ensure their vehicles run smoothly and efficiently for years to come.