A stuffing box shaft seal is fundamentally pivotal in the realm of mechanical engineering, playing a critical role in preventing fluid leakage from a chamber containing pumps or propellers. Comprising a casing, packing material, and gland, these seals envelop a moving shaft to maintain operational integrity by curtailing the escape of substances under pressure. This mechanism serves as a linchpin in diverse industries such as maritime, chemical, and oil & gas – each relying on its robustness to sustain functionality and safety.
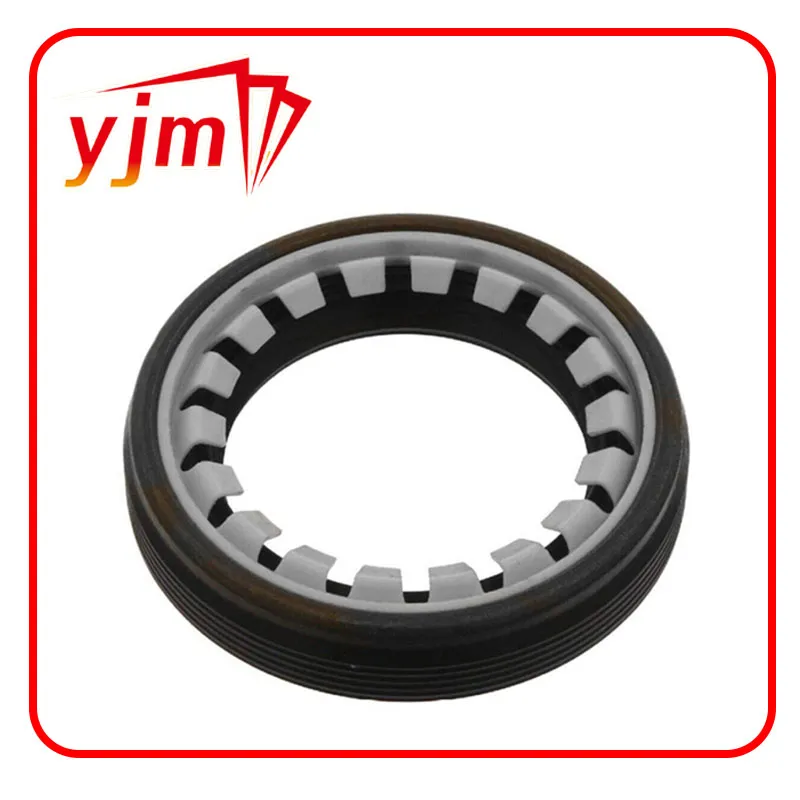
In environments dictated by aggressive conditions and variable pressures, understanding the intricacies of stuffing box shaft seals elevates operational proficiency to new heights. Having borne witness to their capabilities, I offer a journey into unraveling their design, installation, maintenance, and troubleshooting measures through hands-on experience.
To dissect the efficiency of a stuffing box shaft seal, it’s pertinent to explore the expertise behind its composition. The casing, its sturdy exterior, must withstand the rigors of environmental challenges, and thus, is often constructed from materials like stainless steel, bronze, or cast iron. Equally critical, the packing material, historically rope-like flax or hemp soaked in lubricants, has evolved into synthetic fibers and composite materials. These enhancements provide greater resilience and longer service life under demanding operational conditions.
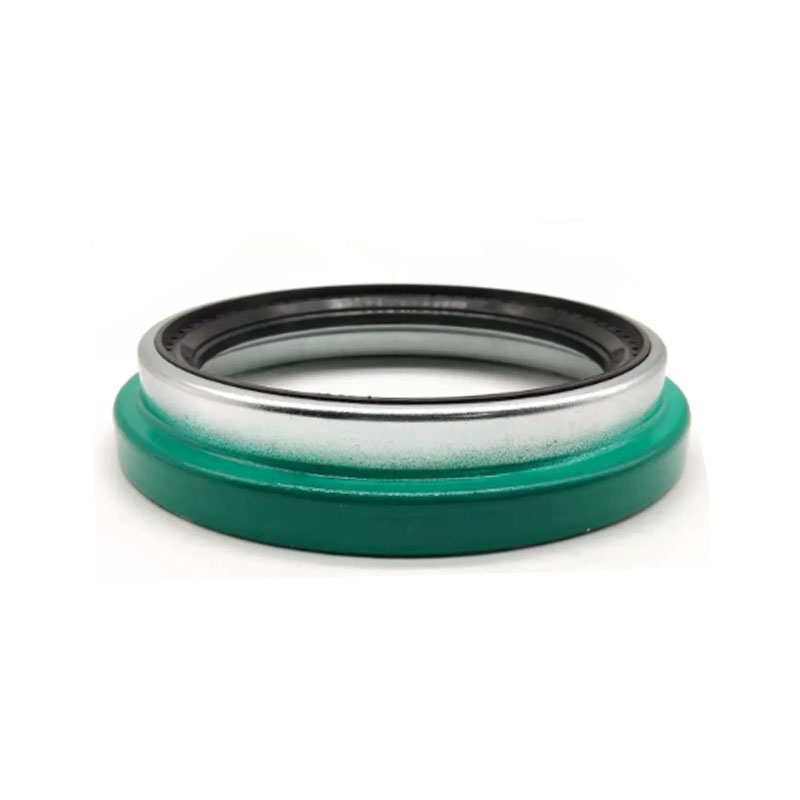
Installation precision is paramount to optimize the seal's functionality. A carefully fitted gland ensures the packing material is compressed evenly around the shaft. Too tight, and friction could generate excessive heat, potentially damaging the components; too loose, and leakage becomes inevitable. Expertise dictates the necessity for a balanced touch during installation, often employing specific torquing sequences and tools to achieve the optimal pressure without compromising the performance.
Having refined this skill through years of practice, it becomes evident that maintenance extends beyond regular lubrication. Observations reveal that a routine inspection schedule is fundamental. Early detection of wear indicators like visible leaks or increased operational noise paves the way for timely interventions, averting costly breakdowns and ensuring longevity.
stuffing box shaft seal
Troubleshooting challenges with stuffing box shaft seals mandates a combination of authoritative knowledge and methodical diagnosis. Common issues include gland packing deterioration,
shaft misalignment, and temperature-induced material degradation. By deploying infrared thermography and vibration analysis, specialists can predictably track changes in the seal's performance metrics, ultimately fostering a trust-based relationship with the technology.
In the domains where high fluid pressures and aggressive substances are commonplace, reliance on trustworthy sealing solutions becomes indispensable. The authority wielded by a well-maintained stuffing box shaft seal is fundamental to safeguarding not only machinery but the environment and personnel interacting with it. As advocates for sustainable engineering practices, professionals consistently prioritize technological advancements that elevate their efficacy.
To cement trustworthiness in the implementation of stuffing box shaft seals, transparency in certification processes and material sourcing is pivotal. Utilizing seals certified by recognized standards bodies ensures compliance with international engineering benchmarks, offering peace of mind in diverse operational settings.
In conclusion, the stuffing box shaft seal emerges as a testament to technical mastery in mechanical sealing solutions. It embodies the confluence of experience, providing operational continuity, expertise in materials and design, and the authority underscored by compliance and performance metrics. Such trustworthiness guarantees its place at the forefront of essential equipment in various industries, handling every demand with a seamless balance of precision and reliability. This dynamic underscores their invaluable role, not just as components, but as custodians of safety and efficiency across the industrial and maritime landscapes.