O-ring rotary seals are commonly used in various industries to prevent leakage and contamination in rotating equipment. These seals are designed to provide a tight seal between the rotating shaft and the stationary housing, ensuring that no fluid or debris can escape or enter the system.
The O-ring rotary seal consists of a flexible rubber O-ring that is placed in a groove on the rotating shaft. As the shaft rotates, the O-ring moves along with it, maintaining contact with the stationary housing and creating a seal that prevents leakage. The O-ring is typically made of materials such as rubber, silicone, or Viton, which are known for their durability and resistance to abrasion and chemical exposure.
One of the key advantages of O-ring rotary seals is their ability to accommodate a wide range of shaft speeds and temperatures. These seals can be used in high-speed applications where traditional seals may fail, and they are also capable of withstanding extreme temperatures without losing their sealing properties. This makes them ideal for use in a variety of industries, including automotive, hydraulic, and aerospace.
Another benefit of O-ring rotary seals is their ease of installation and maintenance. Unlike other types of seals that require complex installation procedures and regular maintenance, O-ring seals can be easily replaced when needed without the need for specialized tools or training Unlike other types of seals that require complex installation procedures and regular maintenance, O-ring seals can be easily replaced when needed without the need for specialized tools or training
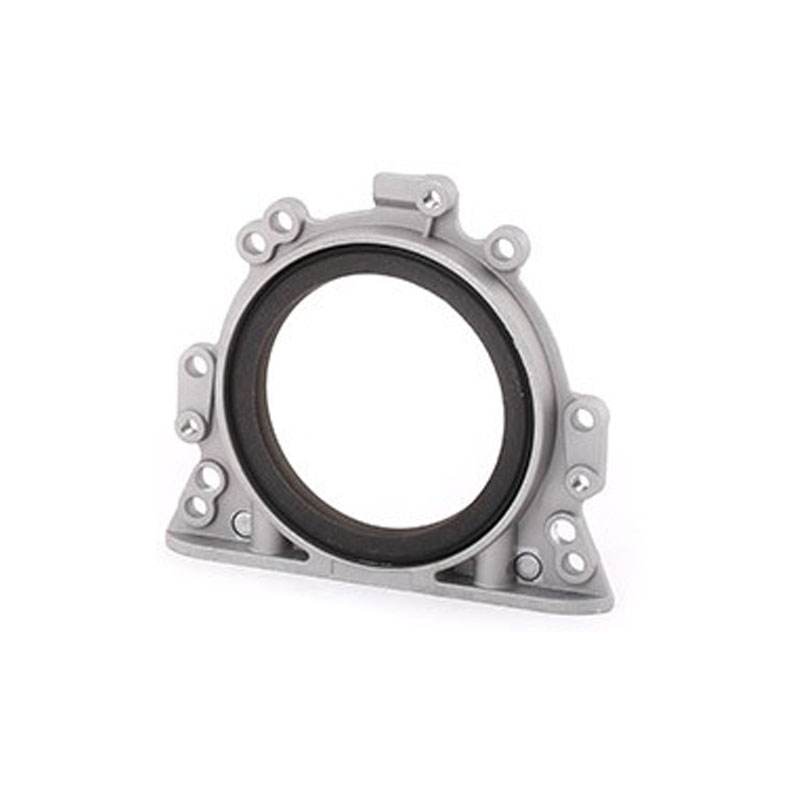
Unlike other types of seals that require complex installation procedures and regular maintenance, O-ring seals can be easily replaced when needed without the need for specialized tools or training Unlike other types of seals that require complex installation procedures and regular maintenance, O-ring seals can be easily replaced when needed without the need for specialized tools or training
o ring rotary seal. This significantly reduces downtime and maintenance costs, making them a cost-effective solution for rotating equipment.
Despite their many advantages, O-ring rotary seals have some limitations that need to be considered. For example, these seals may not be suitable for applications with high pressure differentials or extreme operating conditions. In such cases, alternative sealing solutions, such as lip seals or mechanical seals, may be more appropriate.
In conclusion, O-ring rotary seals are a versatile and reliable sealing solution for a wide range of applications. Their ability to accommodate varying speeds and temperatures, as well as their ease of installation and maintenance, make them a popular choice for industries where leakage and contamination are a concern. While they may not be suitable for all applications, O-ring rotary seals offer a cost-effective and efficient sealing solution for many rotating equipment systems.