Shaft seals play a critical role in numerous industries, ensuring that machinery operates efficiently and without the risk of contamination between different environments. Understanding shaft seal dimensions is essential for professionals who aim to select the right seal for their specific applications. Drawing from years of expertise, this article delves into the importance of shaft seal dimensions, their impact on performance, and how to choose the right size for your needs.
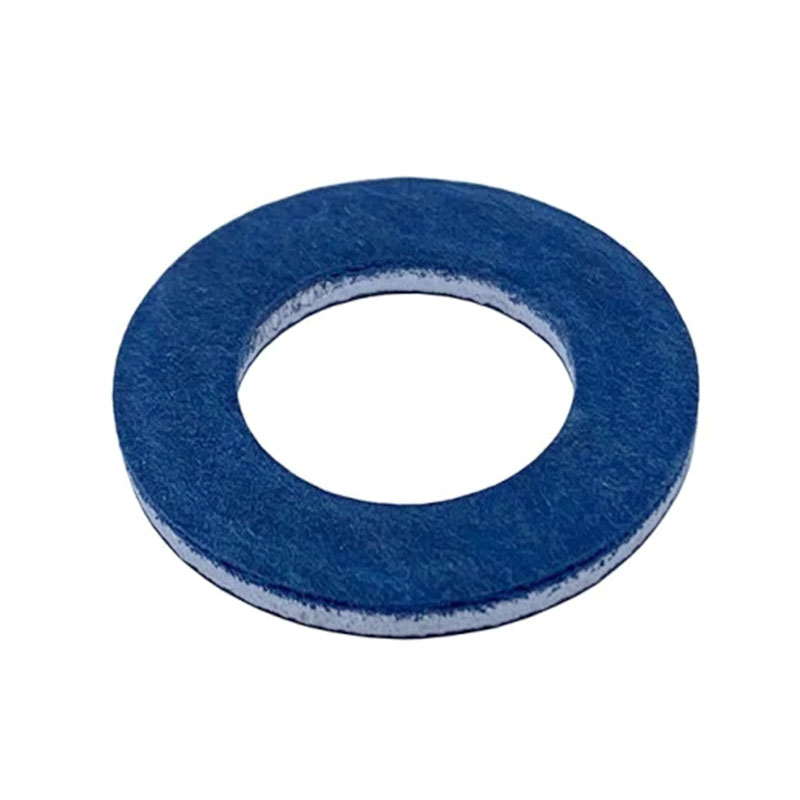
Shaft seals, also known as oil or radial shaft seals, perform the important task of retaining lubricants and keeping contaminants at bay. A fundamental aspect of their effectiveness lies in their precise dimensions. Incorrect sizing can lead to leaks, increased wear, and premature failures, impacting both the machinery's longevity and operational safety.
Experience in dealing with shaft seals reveals that the dimensions must align perfectly with the machinery's requirements. Key considerations include the inner diameter, outer diameter, and width of the seal. The inner diameter should closely fit the shaft size, minimizing gaps that could allow leaks. A common mistake is to select a seal that is slightly oversized, thinking it will offer a better seal. However, this can lead to excessive friction, increased wear, and eventually, a seal breakdown.
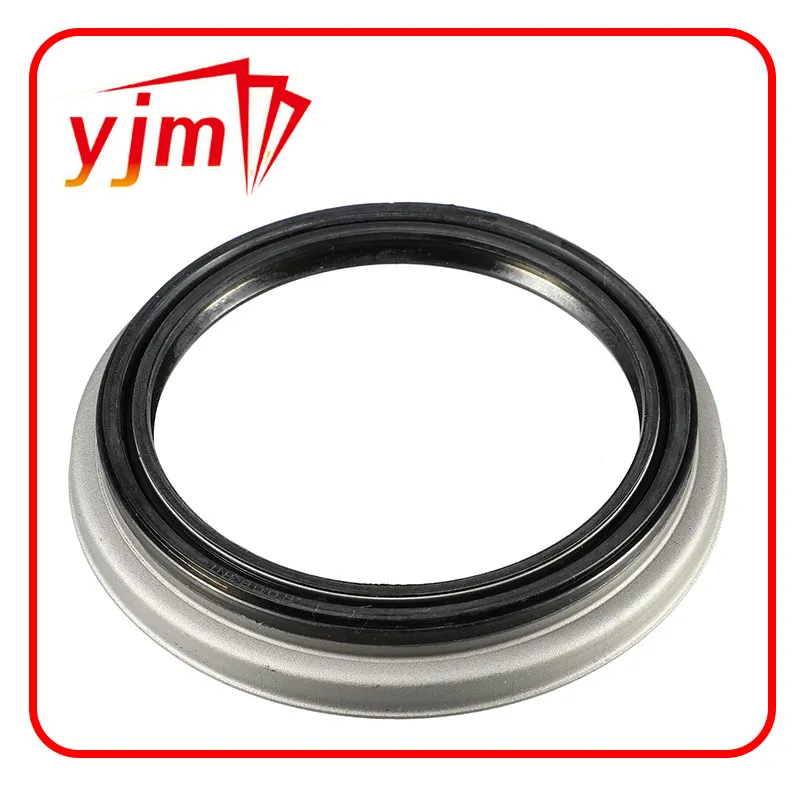
The outer diameter is equally important, as it ensures that the seal fits snugly within the housing.
Precision in this measurement prevents seal displacement during operation. Moreover, the width of the seal can affect its pressure-handling capabilities as well as the bearing load. Sufficient width is crucial, particularly in applications involving higher pressures or dynamic motion.
Expertise in the field emphasizes the significance of material compatibility alongside dimensions. Shaft seals come in various materials such as nitrile rubber, silicone, and polytetrafluoroethylene (PTFE), each with specific properties suitable for different environments. Dimensions might change slightly depending on the material used due to potential swelling or contraction under various conditions.
shaft seal dimensions
The interplay between dimensions and materials underscores the need for adaptability. Today’s markets demand customized solutions tailored to specific operational challenges. Professionals should not merely rely on standard dimensions but should be prepared to source bespoke seals. Customization achieves the perfect balance between dimension accuracy and material resilience, enhancing the seal's performance and longevity, even in the most demanding conditions.
Authoritative knowledge in shaft seal dimensions also involves understanding the application context. For example, seals used in food processing require dimensions that permit easy cleaning and prevent build-up of residues, while seals in chemical industries might need to withstand corrosive substances, demanding precise specifications to maintain a safe operating environment.
Trustworthiness in the selection process is paramount, as incorrect seal dimensions can lead to costly downtimes. Thus, collaborating with reputable manufacturers known for precision engineering and quality assurance can mitigate this risk. These manufacturers often provide dimension charts and detailed specifications, enabling engineers to make informed decisions.
Technological advancements have further edged the precision of shaft seal dimensions. With the advent of CAD (Computer-Aided Design) tools and CNC (Computer Numerical Control) machining, producing seals with exact dimensions has become more efficient. These technologies allow for meticulous design and testing, ensuring that seals perform optimally under specified parameters.
To conclude, selecting the correct shaft seal dimensions is indispensable in ensuring operational efficiency and machinery reliability. Experience teaches that precision in measurement directly impacts performance, while expertise guides the adaptation of materials to suit specific needs. Authoritative sources provide the groundwork for informed decision-making, while trustworthiness fortifies the relationship between suppliers and users, ensuring success across diverse applications. By focusing on these dimensions meticulously, industries can achieve enhanced productivity and longevity of their machinery, safeguarding their investments and operations.