Shaft lip seals are critical components in a wide range of applications, serving as the frontline defense against fluid leakage and contamination. Their primary function is to seal the gap between stationary and moving machine parts, typically around shafts. Understanding the experience of using shaft lip seals, along with their technical nuances, provides valuable insights into their critical role in industrial applications.
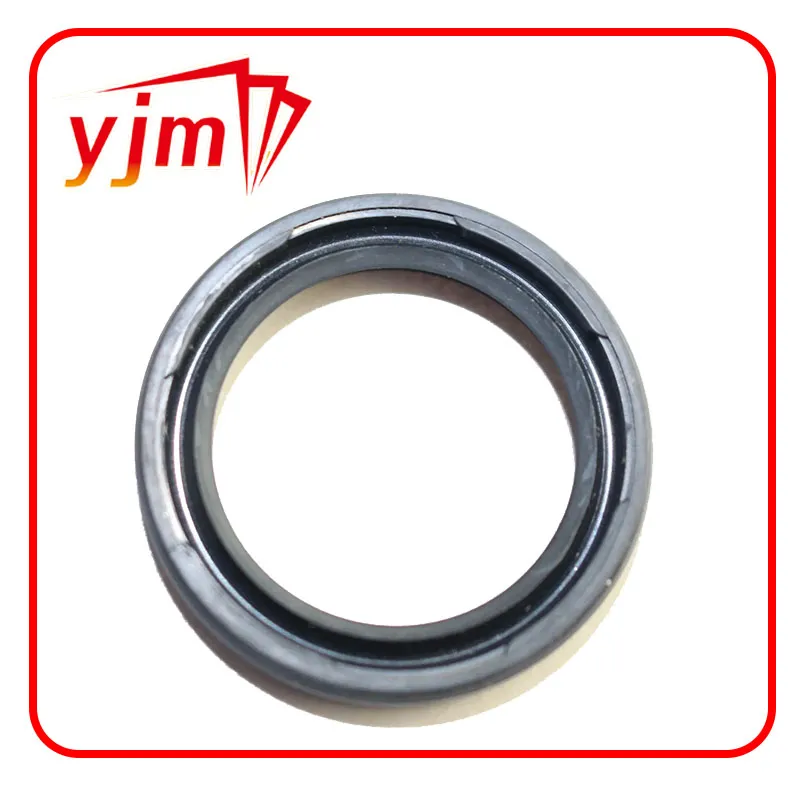
In practical terms, the experience of implementing shaft lip seals often reveals the importance of selecting the right seal material and design. For example, nitrile rubber is widely used due to its robust resistance to oil and wear, making it highly effective in automotive environments where exposure to oil and varying temperatures is common. However, in aggressive environments with chemicals or high temperatures, fluorocarbon elastomer, like Viton®, is preferred due to its enhanced chemical and thermal resistance. The right material choice can significantly extend the lifespan of the seal while maintaining its integrity and performance.
Expertise in shaft lip seals significantly involves understanding their complex functionality and how their design impacts efficiency. Engineers invest considerable time in ensuring the lip of the seal is designed appropriately to adapt to the shaft's rotation and minimize friction. This delicate balance optimizes performance by reducing energy loss and heat generation. Precision in design not only prolongs the seal’s life but also ensures the machinery operates smoothly without costly disruptions due to premature seal failure.
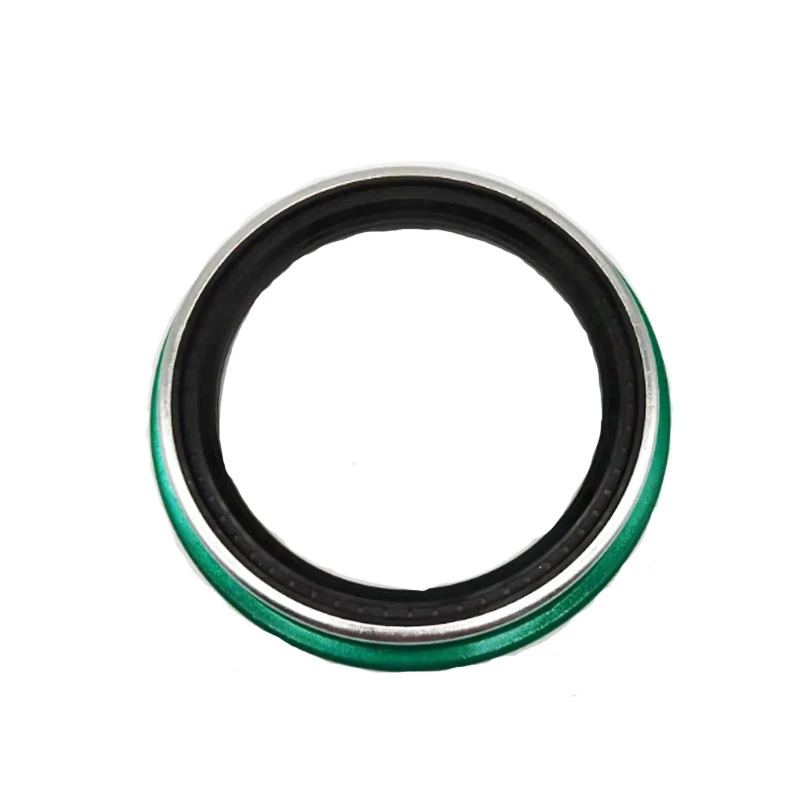
From an authority standpoint, the conversation around shaft lip seals often gravitates towards standardization and compliance. Recognized industry standards, such as DIN and ISO, provide the guidelines necessary to measure the reliability and quality of shaft lip seals. Companies that adhere to these standards in manufacturing and testing assure stakeholders of their commitment to quality and consistency. This authoritative approach is crucial, particularly in industries where machinery downtime can lead to significant financial losses.
In terms of trustworthiness, shaft lip seals have over time proven their reliability and durability, which are pivotal for any operational machinery. Manufacturers often conduct rigorous testing under various operational conditions to certify their products. These tests simulate years of operation to ensure the seals can withstand extreme pressure, temperature fluctuations, and corrosive substances without compromising their functionality. Customer testimonials often emphasize the peace of mind gained from using well-tested shaft lip seals, underscoring their dependability and performance.
shaft lip seals
Moreover, the innovation in coating technologies has enhanced the performance of shaft lip seals. Modern developments allow for low-friction coatings that not only extend the life of the seal but also reduce energy consumption. This is a significant advancement for industries focused on sustainability and energy conservation. Implementing seals with such forward-thinking technologies can give companies a competitive edge by enhancing both the efficiency and eco-friendliness of their operations.
To further understand the characteristic authority of shaft lip seals, industry case studies are weighty testimonials. For instance, the aerospace industry, requiring extreme precision and reliability, has long relied on high-quality shaft lip seals to ensure safety and performance in aircraft engines. The stakes in such industries highlight how shaft lip seals are not just components but are critical to maintaining the sanctity of larger, essential systems. This communication of reliability elevates the trust stakeholders have in these seemingly small, yet mighty, components.
Finally, an integral element to consider is the role of continuous technological advancement in enhancing shaft lip seal designs. The integration of computational fluid dynamics (CFD) and finite element analysis (FEA) allows for more precise modeling in the manufacturing process, predicting performance under varied stress conditions. These technological methodologies have propelled the understanding and development of shaft lip seals into new territories, providing clients with solutions that are both technically meticulous and operationally efficient.
In conclusion, harnessing the right materials, upholding authoritative standards, and embracing technological advancements culminate in the creation of shaft lip seals that are not only pivotal to machinery efficiency but are also trustworthy components within industrial operations. The experience, expertise, authority, and trustworthiness associated with these seals are central to bolstering their performance and extending their application across multiple industries.