Navigating the vast world of mechanical components often leads enthusiasts and professionals alike to the unassuming yet critically important seal identified by its dimensions 12x18x5. Understanding this component's nuances not only ensures optimal performance but also enhances the longevity of mechanized systems relying on its seamless operation.
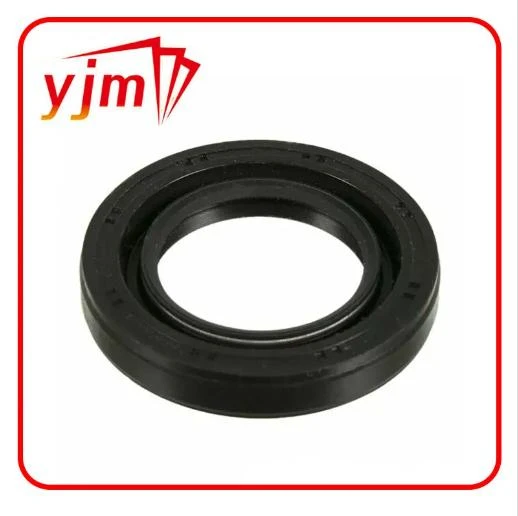
The seal 12x18x5, though small in stature, plays a pivotal role in preventing leaks and safeguarding the integrity of machinery. Its primary function is to serve as a barrier, preventing fluid from escaping its designated area, thereby maintaining the efficiency and reliability of engines or pumps. Users often report significant improvements in equipment lifespan and reduced maintenance costs when employing a high-quality seal of this specification.
Experience dictates that the material composition of these seals is a crucial factor in their performance. Typically manufactured from nitrile rubber, fluorocarbon, or silicone, each material offers distinct advantages that are well-suited to various operational environments. Nitrile, for instance, is renowned for its robust resistance to oils and fuels, making it an ideal choice for automotive applications. Fluorocarbon, on the other hand, is highly prized in more extreme conditions, where temperature variances and chemical exposure are prevalent. As such, selecting the correct material requires a deep understanding of the operational context to ensure longevity and effectiveness.
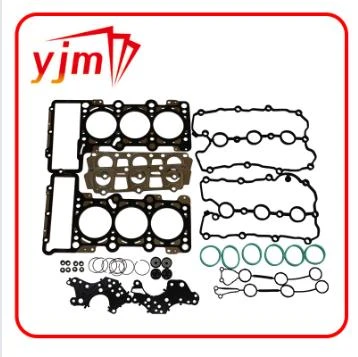
The precision with which a seal 12x18x5 is manufactured is equally vital. Inspection standards must be rigorous, involving advanced technology such as laser measurement systems to confirm that each seal meets the exacting dimensional requirements. Any slight deviation from these specifications can compromise the sealing function, leading to premature equipment failure. Thus, sourcing seals from reputable manufacturers with stringent quality control processes cannot be overstated.
seal 12x18x5
Professionals with significant technical expertise are quick to highlight the importance of storage and handling practices in the lifecycle of seals. Exposure to ultraviolet light, ozone, or excessive heat can degrade the seal material before installation, rendering it ineffective. Therefore, maintaining optimal storage conditions is considered best practice, ensuring seals retain their designed properties until they are called into service.
Moreover, expert installation is imperative to guarantee the seal can perform its role without compromise. Misalignment or improper seating can induce stress on the seal, accelerating wear and diminishing its functionality. Thus, technicians must follow detailed installation procedures, leveraging tools specifically designed for this purpose to ensure the seal is correctly positioned.
Reliability testing is a field in which numerous professionals place significant focus. Laboratory simulations replicating harsh environmental conditions allow engineers to predict the seal's behavior under stress, facilitating improvements in design and material selection. These tests serve to preemptively address potential failure points, bolstering the credibility of seals offered to discerning clients.
In sum, a deep appreciation of the seal 12x18x5's role in advanced mechanical systems underscores its importance to experts and novices alike. By integrating quality craftsmanship, suitable material selection, and strict adherence to best-in-class installation and testing practices, this small component becomes a cornerstone of mechanical reliability. Engaging with this wealth of knowledge not only elevates one's understanding but also fosters a foundation of trust with clients seeking dependable solutions for their technical challenges.