Rubber flat gaskets, an essential component in a myriad of industries, serve as a sealing solution for many engineering and mechanical applications. Whether you're in the business of manufacturing or you're seeking reliable sealing methods for your machinery, understanding the nuances of these gaskets can significantly enhance operational efficiency and reliability.
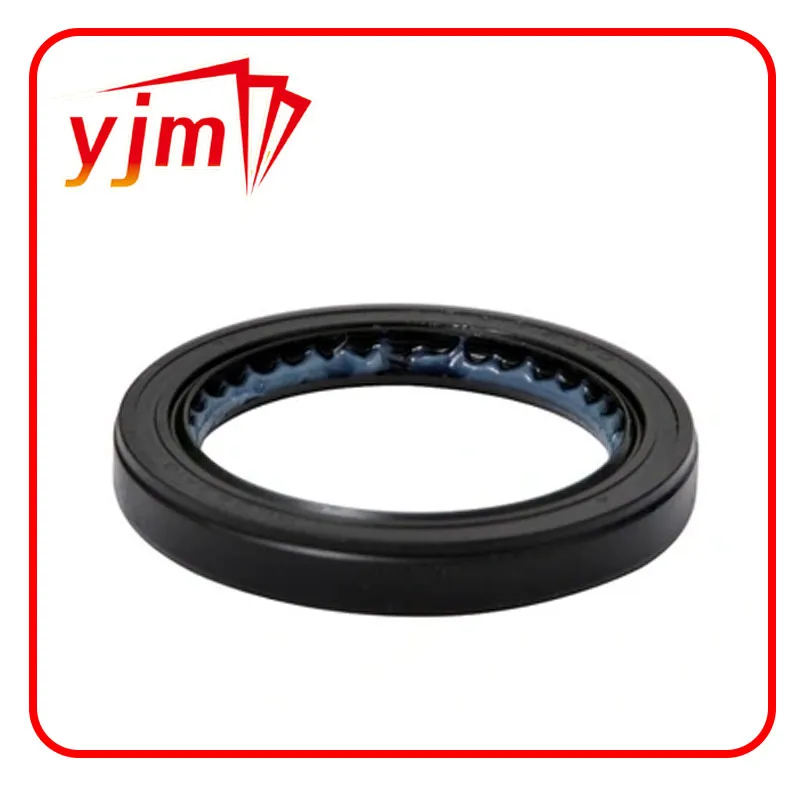
Rubber flat gaskets, crafted from various elastomers like EPDM, Nitrile, and Viton, offer unparalleled flexibility and resilience. These materials are chosen based on specific environmental conditions they need to withstand. For instance, EPDM gaskets are renowned for their exceptional resistance to heat, ozone, and weather. This makes them ideal for outdoor and automotive applications. On the other hand, Nitrile gaskets excel in resisting oils and fuels, which are perfect for use in petrochemical environments.
Experience proves that the selection of the right rubber material is crucial not only for performance but also for longevity. Using a rubber flat gasket that doesn’t align with environmental pressures can lead to frequent gasket failures, resulting in costly downtimes and maintenance. Workshops and factories that have made informed decisions regarding their gasket materials report a significant reduction in maintenance frequencies and an increase in operational uptime.
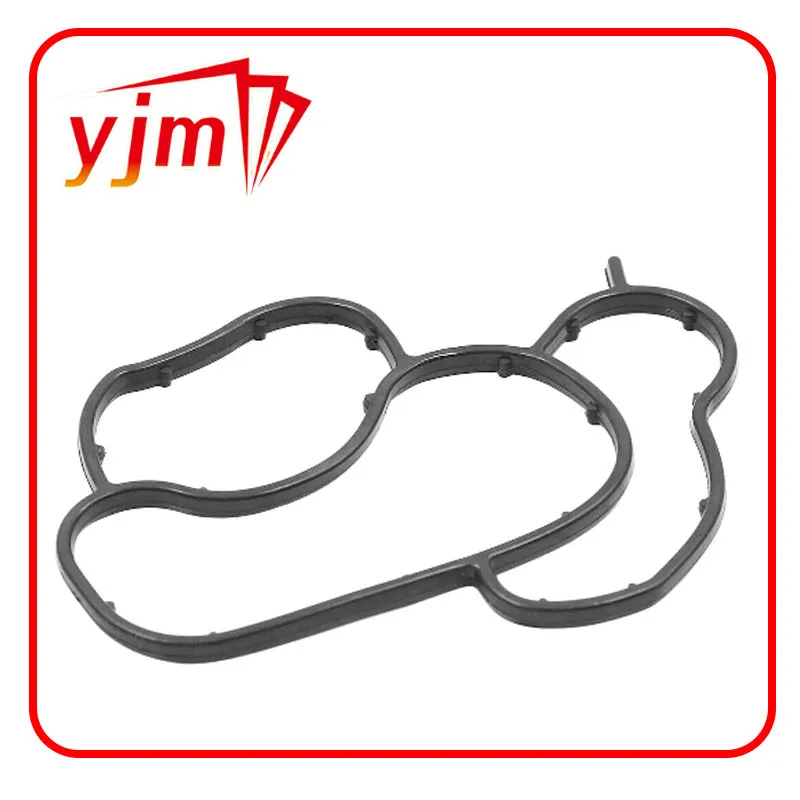
The design of a rubber flat gasket is as critical as the material itself. Expertise in its design can help in customizing them to meet specific requirements. This is especially true in situations where the machine parts are irregularly shaped or where the operating pressures fluctuate significantly. Custom-designed rubber flat gaskets ensure a snug fit, preventing leaks and ensuring consistent performance. Professionals with extensive experience in gasket customizations advise testing the fit in actual operating conditions to confirm efficacy before large-scale implementation.
rubber flat gasket
Rubber flat gaskets offer authority in the sealing landscape due to their simplicity and effectiveness. Their design and function are supported by years of engineering advancements and practical applications. Industry professionals continually trust these gaskets for their sealing needs, primarily due to their low cost juxtaposed with high efficacy. The simplicity of rubber flat gaskets is what makes them versatile; they can be installed with minimal skill and limited tools, making them accessible for many applications around the globe.
Trustworthiness of rubber flat gaskets is confirmed by their widespread and long-standing use across industries. When properly installed, these gaskets offer a reliable seal that can withstand varying degrees of pressure and temperature. Regular inspections and appropriate maintenance are advised to uphold their sealing capacity over time. Reputable manufacturers adhering to stringent quality standards provide gaskets that come with certifications ensuring compliance with international safety and performance standards. This adds an additional layer of confidence for engineers and technicians reliant on their performance.
In conclusion, rubber flat gaskets are indispensable components in industrial operations requiring reliable sealing solutions. Their selection and application require a careful consideration of the operating environment and material-specific properties. By leveraging expert advice and adhering to best practices in gasket usage, industries can optimize their operations, minimize costs, and ensure longevity in their machinery. Seeking guidance from seasoned professionals and investing in gaskets from reputable suppliers are steps in the right direction towards achieving impeccable sealing solutions.