The Vital Role of Rubber Oil Seals in Industrial Applications
Rubber oil seals, an often-overlooked component, play a pivotal role in a myriad of industrial applications. These seemingly insignificant elements are the unseen heroes that ensure the efficient and safe operation of numerous machines and systems. Their primary function is to prevent the leakage of oils, greases, and other fluids, while also protecting the internal components from dust, dirt, and other environmental contaminants.
The term rubber oil seal refers to a specific type of sealing device made primarily from rubber, which exhibits excellent resistance to various oils and chemicals. The material composition of rubber oil seals is crucial, as it determines their compatibility with different types of oils and their ability to withstand temperature extremes. Common materials used for manufacturing these seals include Nitrile Butadiene Rubber (NBR), Fluorocarbon Rubber (FKM), Silicone Rubber, and Ethylene Propylene Diene Monomer (EPDM).
Nitrile rubber, for instance, is widely used due to its excellent resistance to petroleum-based oils and fuels, making it ideal for automotive and industrial applications. On the other hand, FKM or Viton rubber oil seals are preferred in high-temperature environments and chemical-resistant applications. Silicone seals, with their broad temperature range and resistance to ozone and weathering, find usage in automotive and aerospace industries, while EPDM seals are commonly used in water and steam applications.
The design of rubber oil seals is another critical factor. They can be simple lip seals, O-rings, or more complex designs like double-lip seals or scraper seals. Each design has its unique advantages and is chosen based on the specific application requirements Each design has its unique advantages and is chosen based on the specific application requirements
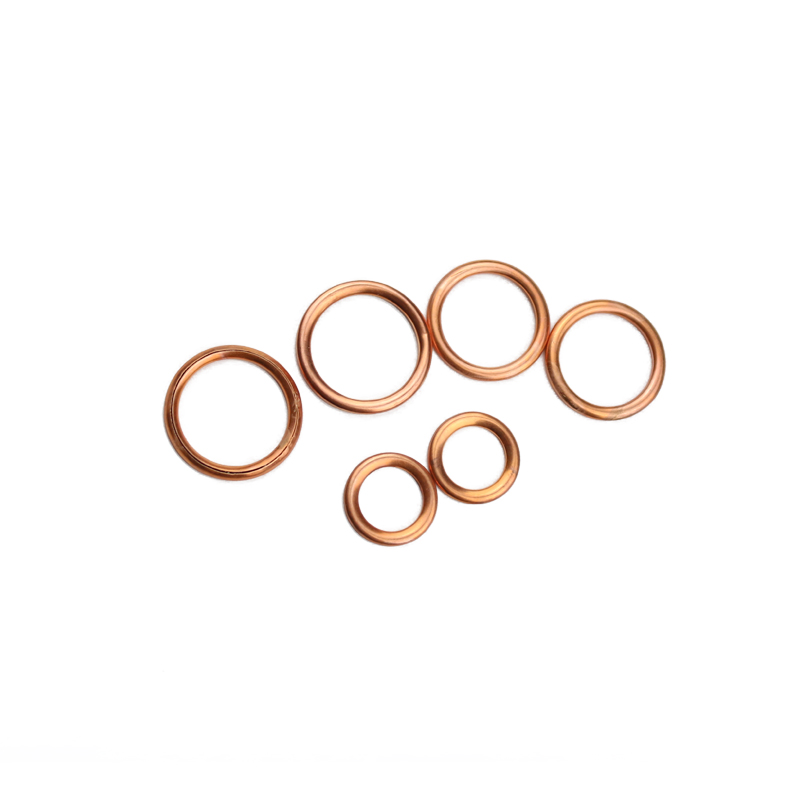
Each design has its unique advantages and is chosen based on the specific application requirements Each design has its unique advantages and is chosen based on the specific application requirements
rubber oil seal. For example, O-rings, due to their simplicity and versatility, are widely used in static and dynamic sealing applications. Scraper seals, on the other hand, are designed to remove contaminants from the sealing interface, making them suitable for dirty environments.
Installation and maintenance of rubber oil seals are equally important. Incorrect installation can lead to premature failure, whereas proper maintenance ensures their longevity. It's essential to follow manufacturer guidelines, as over-tightening or under-tightening can damage the seal, compromising its effectiveness.
In conclusion, rubber oil seals, though small, contribute significantly to the overall performance and reliability of equipment in various industries, from automotive to aerospace, from food processing to oil and gas exploration. Their selection, design, and maintenance are critical aspects that cannot be overlooked. As technology advances, so does the sophistication of these seals, ensuring they continue to meet the evolving demands of modern machinery and systems. Despite their humble appearance, rubber oil seals remain a vital component in safeguarding the integrity and efficiency of industrial processes.