Rotating shaft seals play a critical role in a multitude of industrial applications, ensuring that machinery operates efficiently and without unnecessary wear and tear. These seals are designed to prevent the leakage of fluids along a rotating shaft, which not only helps in maintaining the operational integrity of the system but also extends the lifespan of the equipment. When one delves into the world of rotating shaft seals, understanding the nuances can significantly impact both application success and equipment durability.
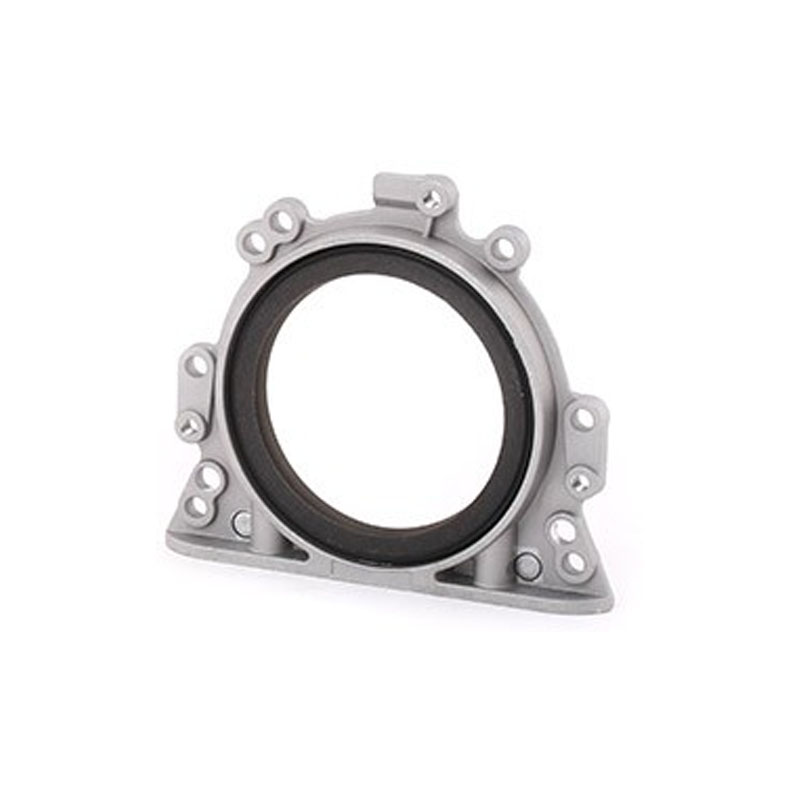
The primary function of rotating shaft seals is to separate environments or contain fluids within a system, thus preventing contamination and leakage. In industries ranging from automotive to aerospace, maintaining this separation is essential for both efficiency and safety. High-quality seals ensure minimal friction, reducing heat generation and wear on components, which are crucial for maintaining operational efficiency and extending service intervals.
From a technical perspective, the design of rotating shaft seals has evolved significantly, reflecting advancements in materials science and engineering. Seals are now crafted from a variety of materials including elastomers, plastics, and composite materials, each chosen for their specific attributes such as chemical resistance, temperature tolerance, and compatibility with different types of fluids. Material selection is paramount and is often determined by the operating conditions such as speed, temperature, and the type of fluids involved.
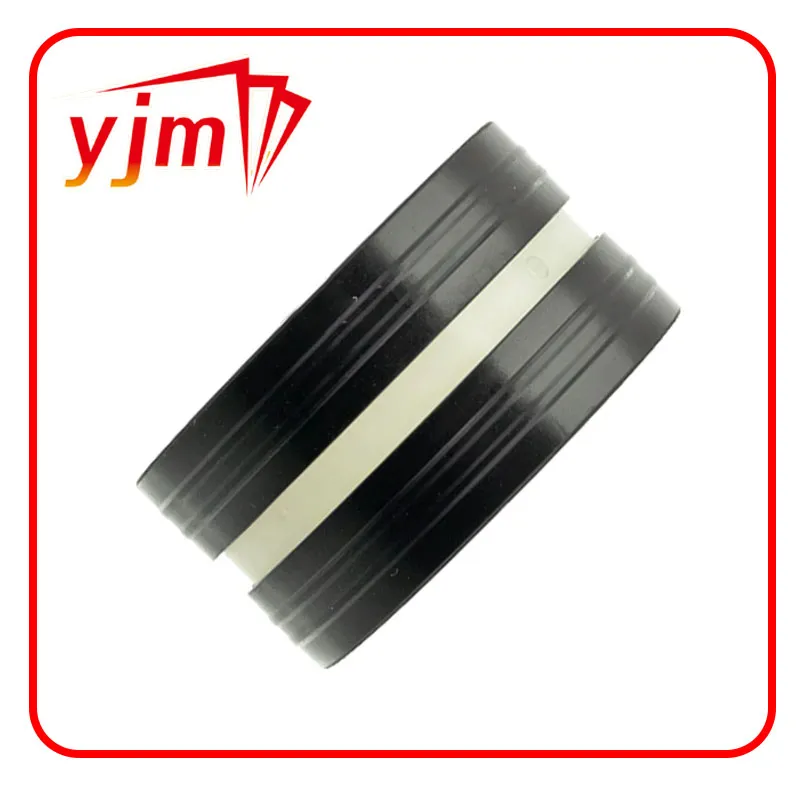
In practical application, the choice of a rotating shaft seal should always be aligned with the system requirements and environmental conditions. For instance, seals used in high-temperature environments are typically made from fluorocarbon or other heat-resistant materials to prevent degradation and maintain elasticity at elevated temperatures. In contrast, seals in contact with aggressive chemicals require materials with superior chemical resistance to avoid breakdown and failure.
rotating shaft seals
Expert engineers and maintenance teams place considerable emphasis on the installation process, which plays a vital role in seal performance.
Improper installation can lead to misalignment, causing uneven wear and potential failures. Therefore, ensuring that the installation is performed accurately by knowledgeable professionals is imperative. This involves not just placing the seal carefully but also ensuring that the shaft surface is prepared appropriately to prevent seal damage during installation.
Trust in a seal’s performance is often established by robust testing and validation, a process that leading manufacturers prioritize to guarantee reliability. Advanced testing methods simulate real-world operational conditions, assessing the seal's endurance, performance under pressure, and long-term durability. By investing in such rigorous testing procedures, manufacturers enhance the credibility and trustworthiness of their products, providing assurance to end-users about their reliability in critical applications.
In the ever-evolving landscape of mechanical engineering and maintenance, staying informed about the latest developments in rotating shaft seals can vastly improve equipment performance and reduce operational costs. Industry experts continuously emphasize the importance of ongoing training for maintenance teams and proactive consultation with seal manufacturers to select the optimal seal for each specific application.
In conclusion, the selection and maintenance of rotating shaft seals are critical to any operation relying on rotary machinery. Investing time in understanding the characteristics of various seal materials, along with rigorous and precise installation practices, can significantly enhance equipment longevity and performance. It’s the amalgamation of sophisticated engineering expertise, authority in seal technology, and a steadfast commitment to quality that forms the cornerstone of achieving operational excellence through superior rotating shaft seals.