Rotating seals play a critical role in various industries, ensuring the efficient operation of machinery by preventing fluid leakage while accommodating the movement between machine parts. Their importance cannot be understated, as they contribute to both operational efficiency and overall safety.
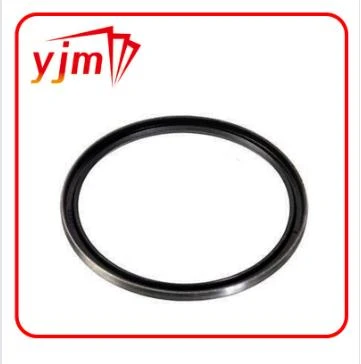
Understanding the nuances of rotating seals starts with their composition and functionality. Typically made from a combination of rubber, graphite, and metallic components, rotating seals are designed to withstand high pressures, extreme temperatures, and corrosive environments. The sophistication of their engineering allows them to maintain tight seals under dynamic conditions, where shafts rotate rapidly and continuously.
In industries like oil and gas, rotating seals are indispensable. They ensure that no hazardous liquids escape, which could potentially lead to environmental disasters or operational shutdowns. In manufacturing, where automation is key, having reliable seals means less downtime and contamination risks, thus improving product quality and throughput. The balance of flexibility and durability that rotating seals must achieve is critical, highlighting why expertise in their design and material selection is essential.
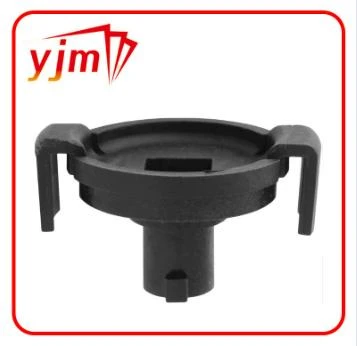
Select the right rotating seal by considering factors such as rotational speed, pressure, temperature, and the nature of the fluids involved. Engineers and maintenance personnel often rely on specialized knowledge and predictive analytics to determine seal longevity and performance within specific environmental conditions. For example, in aerospace applications, seals face extremely high pressures and wide temperature ranges, necessitating materials that can expand and contract without compromising integrity.
Installation and maintenance are equally pivotal in the lifecycle of rotating seals. Improper installation can lead to premature failure, resulting in costly repairs and downtime. Ensuring a snug fit, aligning components precisely, and following manufacturer guidelines are keys to longevity. Regular maintenance checks allow early detection of wear or potential failure points, further emphasizing the necessity for a trained eye and expert methodology in seal management.
rotating seals
Innovations in rotating seal technology continually push boundaries. Recent advancements have introduced seals with embedded sensors. These sensors monitor real-time performance data, highlighting factors like temperature changes, pressure variations, and anomalous vibrations, which can indicate impending failure. With such innovations, operators can undertake predictive maintenance, thus avoiding costly unscheduled downtimes and extending machinery life.
Despite these technological advancements, one cannot overlook the significance of ensuring compliance with safety standards and regulations. The seal industry adheres to international standards such as those from the American Society of Mechanical Engineers (ASME) or the International Organization for Standardization (ISO). These standards guarantee that seals are manufactured and tested to meet rigorous safety and operational benchmarks, lending credibility and trust to manufacturers and users alike.
The market also shows a trend towards customizable solutions for specific operational requirements. This allows for the custom adaptation of seals to unique situations, ensuring optimal performance and longevity. For this, the collaboration between end-users, mechanical engineers, and seal manufacturers becomes crucial. Sharing operational insights and specific needs facilitates the development of tailored seals that meet niche demands.
Educational resources, webinars, and workshops offered by industry leaders and organizations further bolster the knowledge pool surrounding rotating seals. Mechanical engineers, maintenance personnel, and industry decision-makers benefit from continuous learning, staying abreast of the latest technologies and best practices evolving in the field.
The importance of rotating seals spans across multiple dimensions in industry, transcending mere functionality to include economic and environmental impacts. Investing in quality seals and their proper management ultimately results in significant cost savings, improved safety, and enhanced operational efficiency. In markets that demand high performance and reliability, the judicious selection and maintenance of rotating seals stands as a testament to our ability to blend engineering excellence with practical application, driving industry forward.