Rotary seals are crucial components in many industrial applications, boasting a legacy of innovation and advancement that underscores their pivotal role in ensuring operational efficiency and reliability. As an integral part of rotary motion systems, these seals prevent the leakage of fluids or gases, safeguard against contamination, and maintain pressure differentials in various equipment ranging from pumps and compressors to turbines and engines.
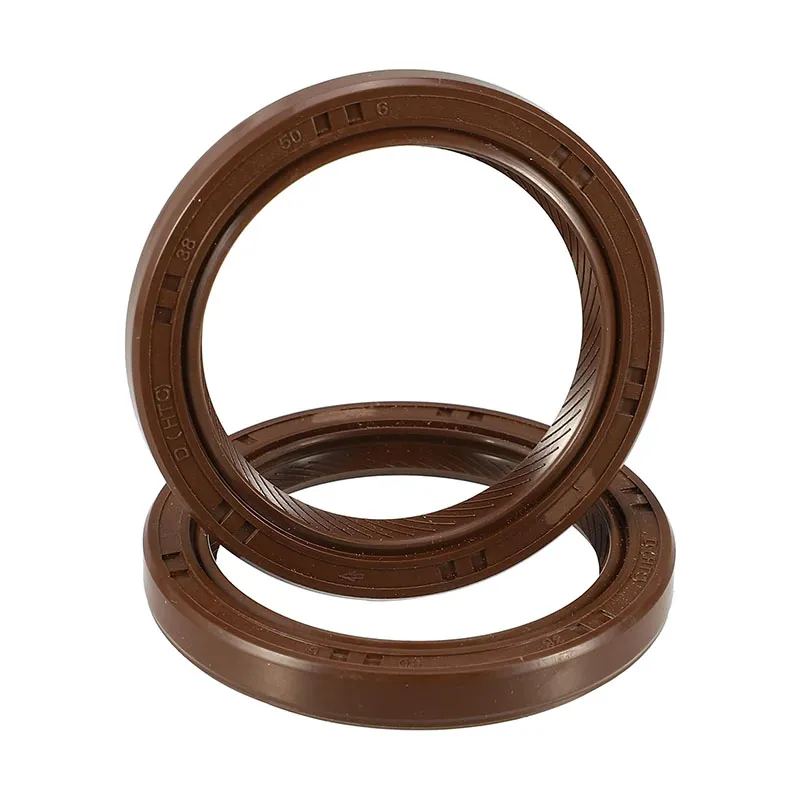
With years of experience in observing the transformation of rotary seals, it's evident that their design and material composition dictate their functionality and longevity. Early iterations relied heavily on rudimentary materials, which, while effective, had limitations in terms of temperature tolerance and chemical resistance. However, advancements in material science have enabled the development of seals crafted from high-performance elastomers and polymers, such as PTFE and FKM. These materials exhibit enhanced durability, flexibility, and compatibility with a wide array of substances, thereby expanding their applicability across industries.
Industry experts understand that selecting the appropriate rotary seal involves a thorough consideration of multiple factors, including the operating environment, the nature of the fluid being sealed, and the desired lifespan of the seal. For instance, in environments exposed to high temperatures and aggressive chemicals, seals made from materials with superior thermal stability and chemical resilience are favored.
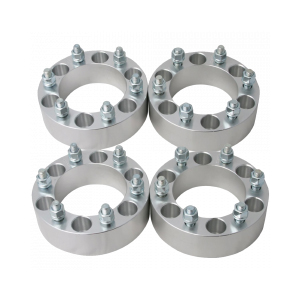
Furthermore, the design of rotary seals has evolved to address specific application demands. Labyrinth seals, for instance, are favored in high-speed applications due to their minimal contact with the rotating shaft, thus reducing wear and extending service life. Conversely, lip seals are renowned for their effectiveness in applications requiring low friction and minimal leakage. This diversity in design highlights the importance of precision engineering in the development of rotary seals, ensuring they meet the exacting standards of modern mechanical systems.
rotary seals
As an authoritative voice in the field, it's worth noting the impact of technological advancements on the manufacturing processes of rotary seals. The incorporation of computer-aided design (CAD) and finite element analysis (FEA) has empowered manufacturers to produce seals with optimal geometry and structural integrity. Such innovations ensure not only superior performance but also cost-effectiveness, as they reduce the need for frequent replacements and maintenance.
Trustworthiness in rotary seal performance can also be attributed to rigorous testing protocols that these components undergo. Manufacturers typically subject seals to a series of tests, including pressure cycling, temperature variation, and exposure to corrosive substances, to verify their reliability under real-world conditions. These tests are crucial for industries where seal failure could lead to catastrophic consequences, ensuring that each product lives up to its promise of performance and safety.
In recent years, the demand for environmentally friendly solutions has prompted a shift towards the development of rotary seals with reduced environmental impact. This includes the use of recyclable materials and the implementation of manufacturing processes that minimize waste and energy consumption. Such efforts align with global sustainability goals and reflect a broader commitment to responsible manufacturing practices.
In conclusion, the realm of rotary seals is marked by a blend of experience, expertise, authoritativeness, and trustworthiness, each of which plays a significant role in the continued development and application of these essential components. As industrial demands evolve, so too must the design and functionality of rotary seals, ensuring they remain indispensable to the efficient and safe operation of machinery across countless sectors. For those seeking to harness the full potential of rotary seals, understanding their capabilities, limitations, and innovations is paramount to achieving optimal performance and operational success.