In the intricate world of mechanical engineering and industrial applications, radial seals play a pivotal role in ensuring the seamless operation of machinery and equipment. These seals are crafted to prevent fluid leakage in dynamic systems, maintaining the integrity and performance of mechanical assemblies. Here, we delve into the comprehensive aspects of radial seals, exploring their types, functionalities, and the expertise needed to select the right seal for specific applications.
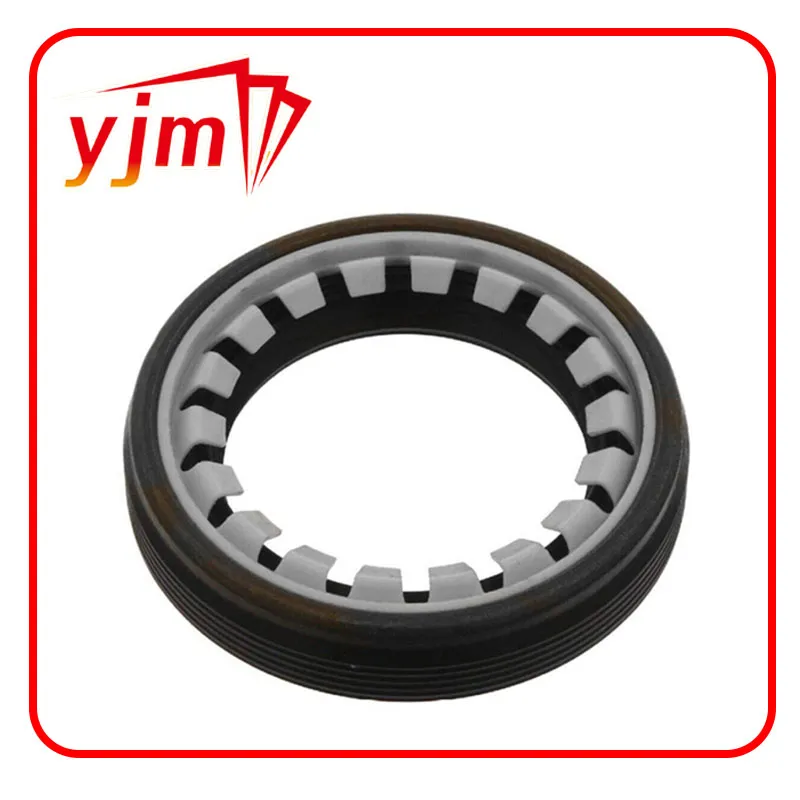
Radial seals are commonly used in various industries, including automotive, aerospace, and manufacturing. Their primary function is to provide a barrier between two or more components, effectively containing lubricants or other fluids and keeping contaminants at bay. This critical sealing is achieved through different design profiles and materials, each selected based on specific operational environments and requirements.
There are two main categories of radial seals dynamic and static. Dynamic radial seals are used in applications where there is relative motion between the mating surfaces, such as in rotating shafts or reciprocating movements. Static radial seals, on the other hand, are employed where there is no motion between surfaces, acting more as a gasket. Understanding the difference between these two categories is fundamental in choosing the correct seal for the job.

Material selection is paramount in the design and application of radial seals. Elastomers, such as nitrile, silicone, and fluorocarbon, are commonly used due to their flexibility and resistance to various environmental factors. Metal seals, though less common, are utilized in extreme conditions that require durability and robustness. The choice of material influences the seal's performance, durability, and compatibility with the fluids or gases in the system.
For optimal performance, factors such as temperature range, pressure, speed of movement, and exposure to chemicals or abrasive materials must be considered. Engineers and specialists rely on extensive experience and scientific expertise to make these selections, often using computer-aided design and simulation tools to predict a seal's behavior under hypothetical conditions before installation.
radial seals
One of the challenges in utilizing radial seals lies in installation and maintenance. Improper installation can lead to premature failure, while maintenance is essential for ensuring the longevity and efficiency of the seal. Regular inspection and timely replacement of worn seals help prevent unexpected downtimes and costly repairs.
The authoritativeness in the domain of radial seals is reinforced by standards and testing methodologies set by industry bodies such as ASTM International and the International Organization for Standardization (ISO). Compliance with these standards ensures reliability, safety, and quality, establishing a benchmark that enhances trustworthiness in production and application.
As the landscape of industrial applications evolves, so too does the technology behind radial seals. Innovations in materials science and precision manufacturing techniques continue to expand the capabilities and applications of radial seals. This progress serves industries by providing solutions that not only meet current demands but also anticipate future challenges.
In conclusion, radial seals are indispensable components in the machinery that propels industries forward. Their successful application hinges on the structured knowledge and expertise applied in their selection, design, and maintenance. Whether in the form of cutting-edge elastomers or hearty metal variations, radial seals testify to human ingenuity and the relentless pursuit of efficiency and reliability in mechanical systems. As we forge ahead, the principles guiding the evolution of radial seals will remain rooted in experience, expertise, authority, and trust—pillars essential to the industrial world’s ongoing advancements.