The Importance of Radial Oil Seals in Machinery and Equipment
Radial oil seals, an essential component in the world of mechanical engineering, play a pivotal role in ensuring the efficient functioning and longevity of various machines and equipment. These seals, often underestimated, are the silent guardians that prevent lubricants from escaping and contaminants from infiltrating critical mechanical systems.
A radial oil seal, as the name suggests, operates radially, sealing the interface between rotating or reciprocating shafts and their housings. It is designed to maintain a barrier, preventing oil leakage while simultaneously blocking ingress of dust, dirt, and other environmental elements that could degrade performance or cause damage. The primary material used for manufacturing these seals is typically rubber, elastomers, or polyurethane, providing a flexible and durable barrier.
The design of a radial oil seal is intricate and sophisticated. It consists of a main body, usually made of a resilient material, with an inner and outer lip that contacts the shaft and housing respectively. The inner lip, being the primary sealing element, presses against the shaft surface, creating a seal while allowing for minimal friction-induced wear. The outer lip, on the other hand, acts as a secondary defense against contaminants.
In automotive applications, radial oil seals are crucial for protecting engine components like crankshafts and camshafts. They ensure that engine oil stays within the system, reducing the risk of oil leaks and potential engine damage. In industrial machinery, they are employed in pumps, compressors, and hydraulic systems to maintain optimal lubrication and prevent contamination In industrial machinery, they are employed in pumps, compressors, and hydraulic systems to maintain optimal lubrication and prevent contamination
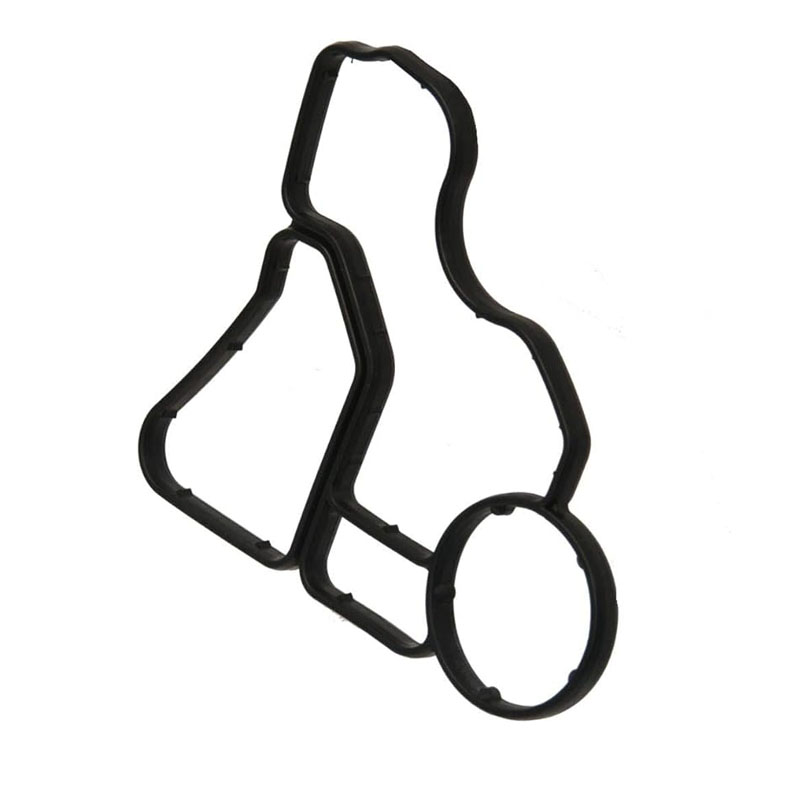
In industrial machinery, they are employed in pumps, compressors, and hydraulic systems to maintain optimal lubrication and prevent contamination In industrial machinery, they are employed in pumps, compressors, and hydraulic systems to maintain optimal lubrication and prevent contamination
radial oil seal.
Choosing the right radial oil seal is paramount. Factors such as operating temperature, pressure, speed, and the type of fluid or environment it will be exposed to must all be considered. A poorly chosen seal can lead to premature failure, increased maintenance costs, and even machine downtime.
Maintenance and proper installation of radial oil seals are also vital. Incorrect installation can compromise the seal's effectiveness, leading to oil leaks and reduced equipment lifespan. Regular inspection and timely replacement when signs of wear or damage are detected can prevent major issues.
In conclusion, radial oil seals are more than just a simple component; they are a critical aspect of machinery's overall health and performance. Their role in safeguarding lubricants, preventing contamination, and ensuring smooth operation cannot be overstated. Understanding their function, selecting the appropriate seal, and maintaining them properly is essential for maximizing the efficiency and longevity of any mechanical system. As technology advances, so too do the designs and materials of radial oil seals, continuously evolving to meet the demands of modern machinery and equipment.