In the realm of fluid engineering, the pump shaft seal is an often underestimated yet vital component. It plays an essential role in the function and efficiency of pumps by preventing fluid leakage and maintaining pressure within the pump assembly. A proficient design and choice of shaft seal can lead to enhanced operational longevity, energy efficiency, and significant savings in maintenance costs. Herein, we provide a comprehensive exploration of pump shaft seals guided by essential markers of Experience, Expertise, Authoritativeness, and Trustworthiness.
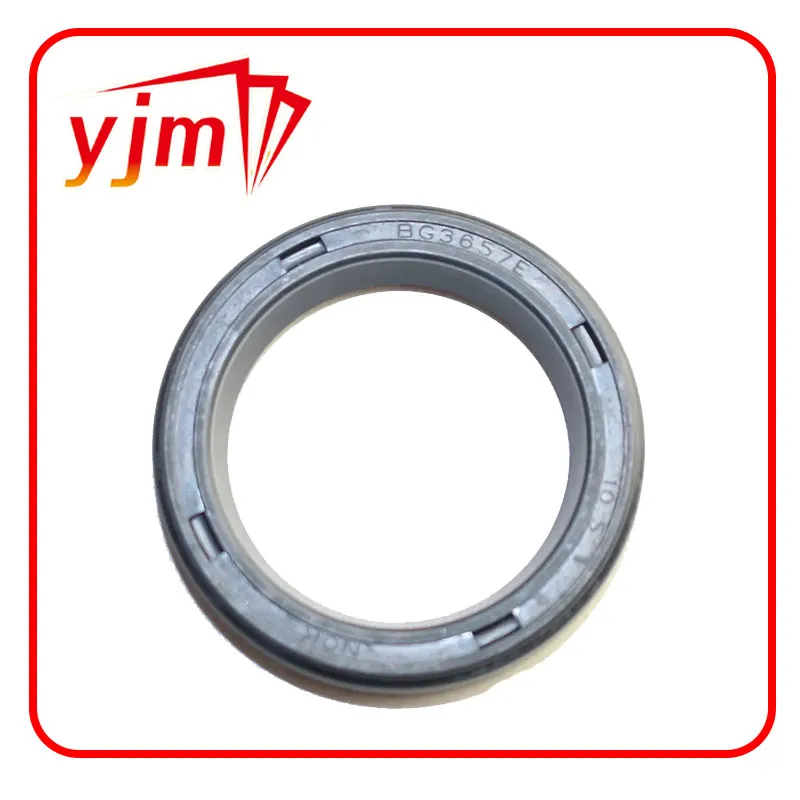
Pump shaft seals embody a fusion of engineering precision and material science. These seals are generally tasked with preventing leakage of fluids such as water, chemicals, or oil along the rotating shaft. The choice of seal depends heavily on the type of pump and the fluid being transferred, which can vary from corrosive chemicals to slurry mixtures.
Experience in selecting the correct pump shaft seal is substantially informed by understanding the operational environment. Different seals are suited to different applications mechanical seals, for instance, are ideal for high-pressure and high-speed applications due to their robust design and ability to handle wear and tear. Conversely, packing seals might be deployed in applications where simple and cost-effective solutions suffice. Over time, engineers and operators learn to identify nuanced operational disturbances that hint at seal wear or failure, relying on firsthand experience to make timely maintenance calls.
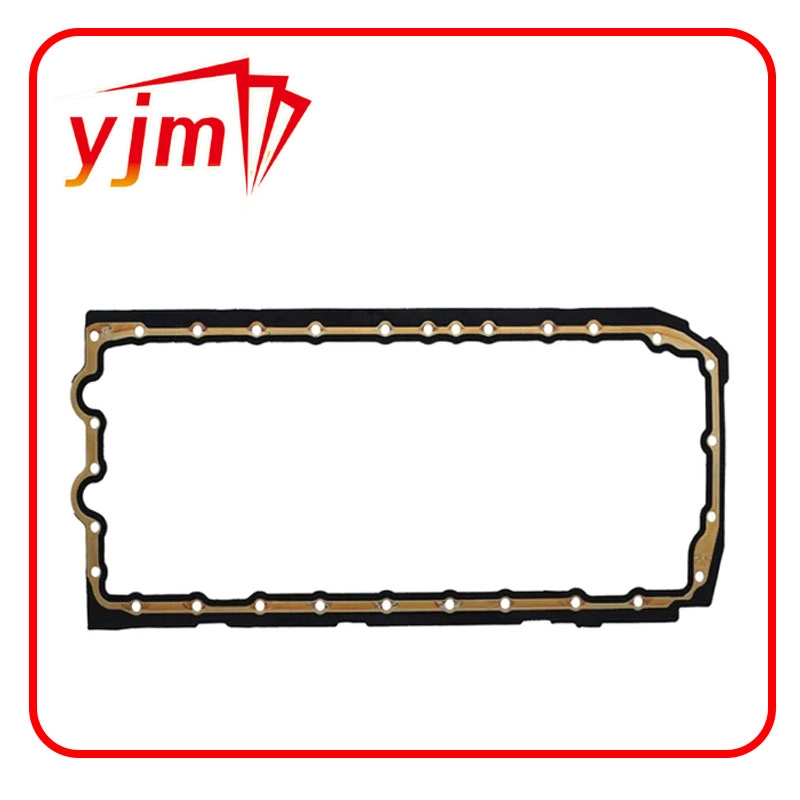
Delving into expertise, the manufacturing and selection of a pump shaft seal require profound technical proficiency. The engineering behind a successful seal involves calculating variables like shaft speed, pressure, temperature, and fluid viscosity. For instance, seals in chemical processing industries often need to withstand aggressive fluids, demanding materials such as Viton or PTFE, known for their chemical inertness. Expertise also plays a role in understanding the latest technological advancements in seal designs, such as edge-welded bellows mechanical seals that offer superior performance in extreme conditions.
pump shaft seal
From an authoritative viewpoint, credible knowledge on pump shaft seals comes from industry standards and qualifications. Standards such as API 682 provide a framework for seal technology used in petroleum, petrochemical, and natural gas industries, ensuring reliability and safety. Manufacturers and suppliers that adhere to such standards earn a reputable standing in the market. Furthermore, certified training programs and accreditation from renowned engineering bodies lend authority and reliability to professionals dispelling advice on seal selection and maintenance.
Trustworthiness in information about pump shaft seals is critical and is built on transparency and validated performance data. Customers place high trust in brands and service providers who offer extended warranties, and who transparently communicate the conditions under which their products perform optimally. User testimonials and third-party endorsements often cement trustworthiness, providing real-life validation to the specified claims.
Innovations continue to shape the landscape of pump shaft seals. Recent advancements like the introduction of bi-directional seals, which maintain functionality irrespective of shaft rotation direction, demonstrate the industry's commitment to solving complex operational challenges. Smart seals equipped with sensors that monitor parameters like pressure and temperature further push boundaries, offering predictive maintenance insights that preempt failures and downtime.
In sum, the pump shaft seal is not merely a component but a cornerstone of efficient industrial fluid handling. The combination of lived experience, specialized expertise, recognized authority, and demonstrated trustworthiness underpins effective use and technological advancement in pump shaft seals. By understanding and leveraging these facets, operators and engineers can significantly enhance their operational efficiencies and maintenance outcomes.