Cr seals, also known as cylinder rod seals, are a critical component in the functioning of hydraulic cylinders. They are designed to withstand high pressure, extreme temperatures, and continuous exposure to fluids, making them essential for maintaining the integrity and efficiency of machinery in various industrial applications.
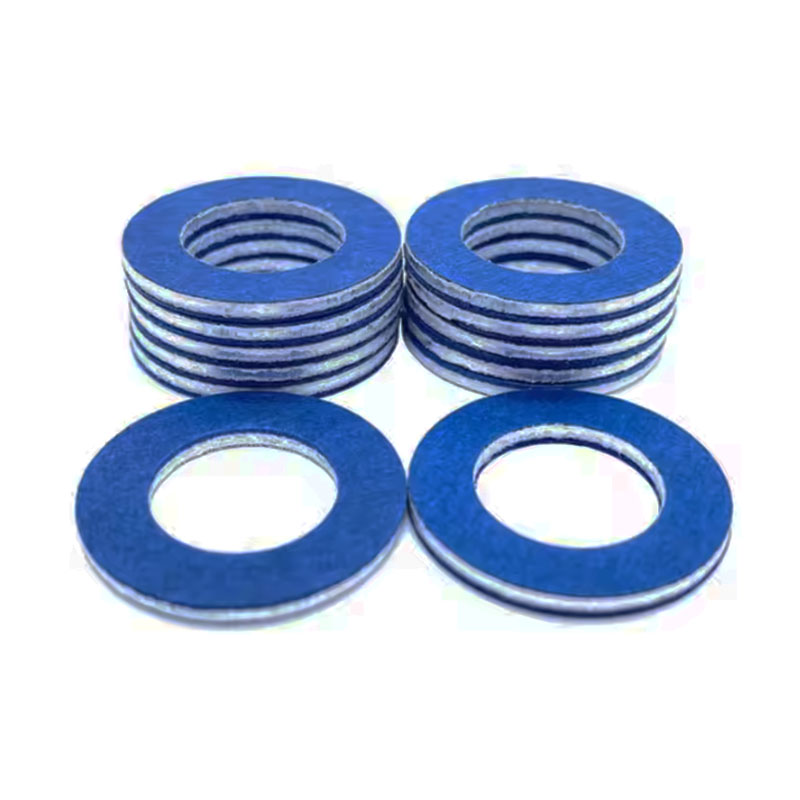
In the intricate ecosystem of hydraulic systems, cr seals serve as the frontline protectors, preventing hydraulic fluid leakage and contamination. Their primary role is to ensure the smooth operation of hydraulic cylinders by keeping the hydraulic fluid where it is needed and maintaining pressure within the system. This directly impacts the performance of the machinery, making the choice and maintenance of cr seals a matter of paramount importance.
The efficacy of cr seals hinges on several factors, including material composition, design configuration, and compatibility with hydraulic fluids. The most commonly used materials for cr seals are polyurethane, rubber, and PTFE (Polytetrafluoroethylene), each offering distinct advantages. Polyurethane is known for its resilience to wear and tear, rubber provides excellent elasticity and sealing capabilities, while PTFE is celebrated for its high resistance to chemicals and extreme temperatures.
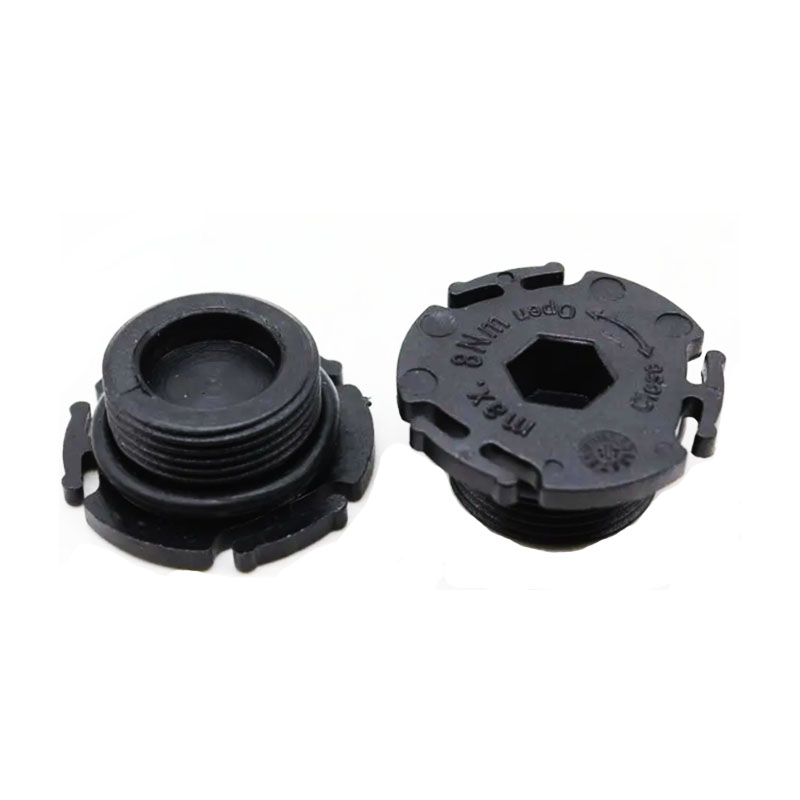
For industries that operate in harsh environments, such as construction, mining, and agriculture, the selection of the right cr seal goes beyond material considerations. Design configurations such as u-cup seals, symmetrical rod seals, and rod wipers provide unique sealing solutions tailored to specific operational demands. For instance, u-cup seals offer a dynamic sealing capability that adapts to fluctuating pressure, whereas rod wipers prevent external contaminants like dirt and moisture from entering the system.
From an expert perspective, the successful deployment of cr seals requires regular inspection and maintenance. Industry standards recommend a routine check-up to identify signs of wear, such as cracks, abrasions, or hardening of the seal material. Early detection of potential seal failure can prevent catastrophic system failures, thereby prolonging the life of the machinery and reducing maintenance costs.
cr seal
In the competitive marketplace, authoritative brands like SKF, Parker Hannifin, and Freudenberg Sealing Technologies set the benchmark for quality and innovation in cr seal technology. These brands invest heavily in research and development, continuously enhancing their product offerings to meet the evolving needs of various industries. Collaborating with such reputable brands assures stakeholders of product reliability and performance, fostering trust and confidence in hydraulic system operations.
Moreover, integrating technology and advanced analytics into seal maintenance practices can significantly enhance trustworthiness and reliability. Predictive maintenance, using IoT sensors and machine learning algorithms, enables real-time monitoring of seal conditions, offering insights that preempt issues before they manifest into operational downtime.
Ultimately, the choice of cr seals must align with the broader operational goals of the organization. Engaging with a qualified seal supplier who provides expert guidance and support is crucial. They can offer bespoke solutions that not only meet technical specifications but also contribute to the overall efficiency and sustainability of hydraulic systems.
In conclusion, the role of cr seals in the machinery landscape is indispensable. Their ability to maintain hydraulic integrity, withstand adverse conditions, and ensure optimal performance underpins their importance. By combining expertise and cutting-edge technology, industries can harness the full potential of cr seals, driving innovation and achieving greater operational excellence.