Elevating the understanding of O-ring backing rings involves delving deep into their essential applications, material choices, and best industry practices. O-ring backing rings are an often overlooked yet crucial component in the sealing industry, serving to enhance the performance and longevity of O-rings in various high-pressure environments.
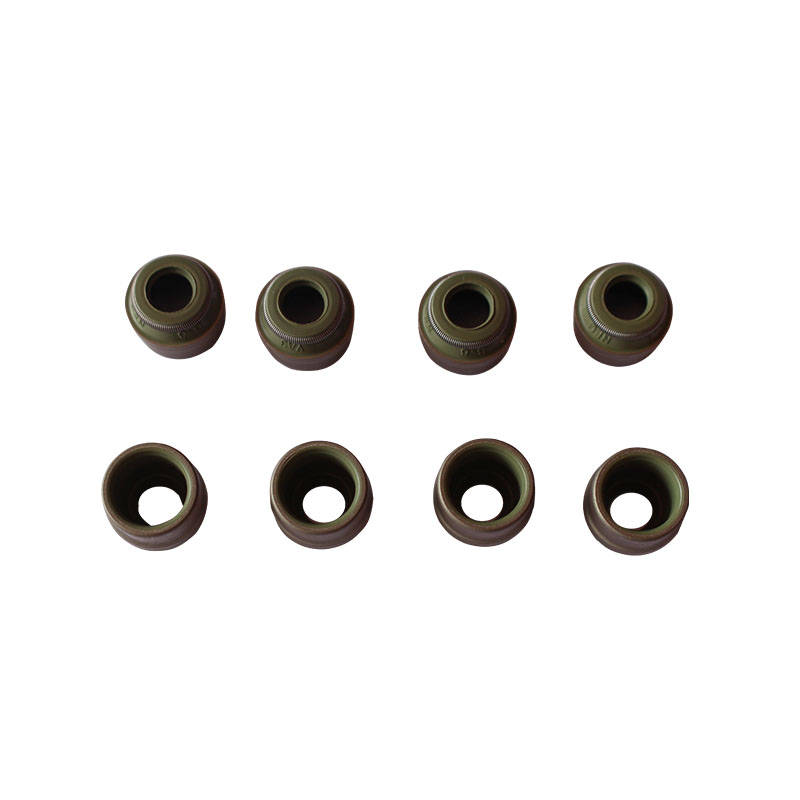
In hydraulic and pneumatic systems,
O-ring backing rings play an indispensable role. These systems often operate under intense pressure, and the absence of adequate support can lead to seal extrusion or failure. Backing rings provide a mechanical safeguard against extrusion, thereby ensuring that O-rings maintain optimal sealing capabilities and extend their service life. This capability is vital in industries ranging from automotive to aerospace, where the integrity of seals affects overall system performance and safety.
Backed by years of field experience, experts in sealing solutions unanimously highlight the importance of selecting the right material for backing rings. The choice of material substantially impacts the performance of the sealing system. Common materials include PTFE (polytetrafluoroethylene), PEEK (polyether ether ketone), and various elastomers, each offering unique properties. PTFE, for instance, is renowned for its excellent chemical resistance and low friction, making it suitable for applications involving aggressive fluids and high temperatures. On the other hand, PEEK is favored for its exceptional mechanical strength and thermal stability, suitable for extreme environments. Selecting the appropriate material requires a thorough understanding of the application's specific conditions and demands.
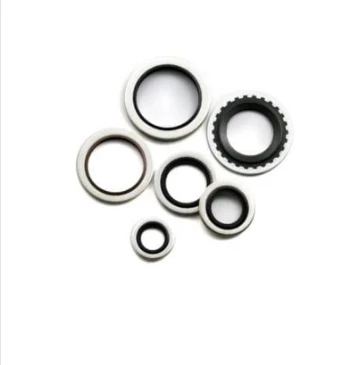
The expertise of O-ring backing ring manufacturers plays a crucial role in their efficacy. Leading industry players employ advanced manufacturing techniques and rigorous quality control measures to ensure that each backing ring meets stringent tolerances and specifications. Precision in design and manufacturing is crucial as even minor deviations can compromise seal integrity. Years of research and development have culminated in innovative designs that cater to the evolving needs of various industries, showcasing a deep understanding of sealing challenges.
o ring backing ring
Authoritative insights from industry professionals emphasize that proper installation of O-ring backing rings is as crucial as selecting the right material. Installation errors can lead to premature failure and costly downtime. It is imperative for technicians to follow precise installation procedures, which include ensuring clean surfaces, correct alignment, and adequate lubrication. Adopting best practices in installation not only prevents issues but also enhances the trustworthiness of the sealing system, fortifying its reliability under extensive operational demands.
Moreover, ongoing maintenance and inspection are necessary to sustain the performance of O-ring backing rings. Regular inspection can preemptively identify signs of wear or damage, allowing for timely intervention. This proactive approach is essential in industries where equipment failure can result in significant operational and financial setbacks. By adhering to stringent maintenance protocols, companies can uphold the trust and reliability attributed to their sealing systems.
O-ring backing rings are more than mere ancillary components; they are pivotal for achieving optimum sealing solutions. Through informed material selection, adherence to expert manufacturing protocols, meticulous installation, and vigilant maintenance, O-ring backing rings can vastly improve the reliability and performance of sealing systems. By incorporating these elements, industry professionals can ensure that their sealing solutions withstand the challenges presented by their operating environments, enhancing overall system durability and efficiency.