In the dynamic landscape of mechanical engineering, oil seals play a pivotal role in ensuring the seamless operation of machinery. Known for preventing the leakage of lubricants and the ingress of detrimental contaminants, oil seals are indispensable components in various applications. This article delves into the world of oil seal manufacturers, dissecting the elements that contribute to their success and the features that elevate their products above industry standards.
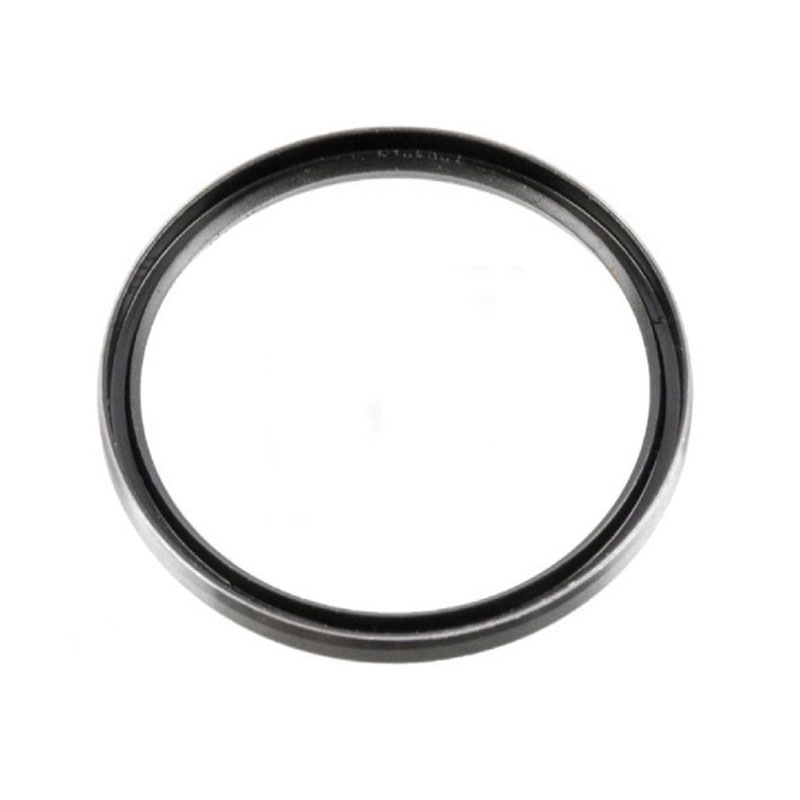
From the bustling factories in Asia to the precision-focused workshops in Europe, the oil seal manufacturing industry is as diverse as the applications of its products. A comprehensive understanding of materials and production techniques distinguishes top-tier manufacturers from the rest. These companies invest significantly in research and development to innovate and enhance oil seal performance. For instance, the integration of advanced materials such as fluorocarbon and silicone not only improves the temperature tolerance of oil seals but also enhances their chemical resistance, thereby extending the lifespan of the machinery they protect.
The expertise of oil seal manufacturers is demonstrated through their ability to produce seals that cater to a wide array of industries. Whether for automotive, marine, or industrial applications, each seal must meet the unique requirements of its environment. This specialization is often supported by a strong engineering team that collaborates closely with clients to design custom seals, tailored to meet specific operational needs. The authority of a manufacturer in this sector is often exhibited by certifications that speak to their adherence to international standards, such as ISO 9001, which assures quality management systems are in place.
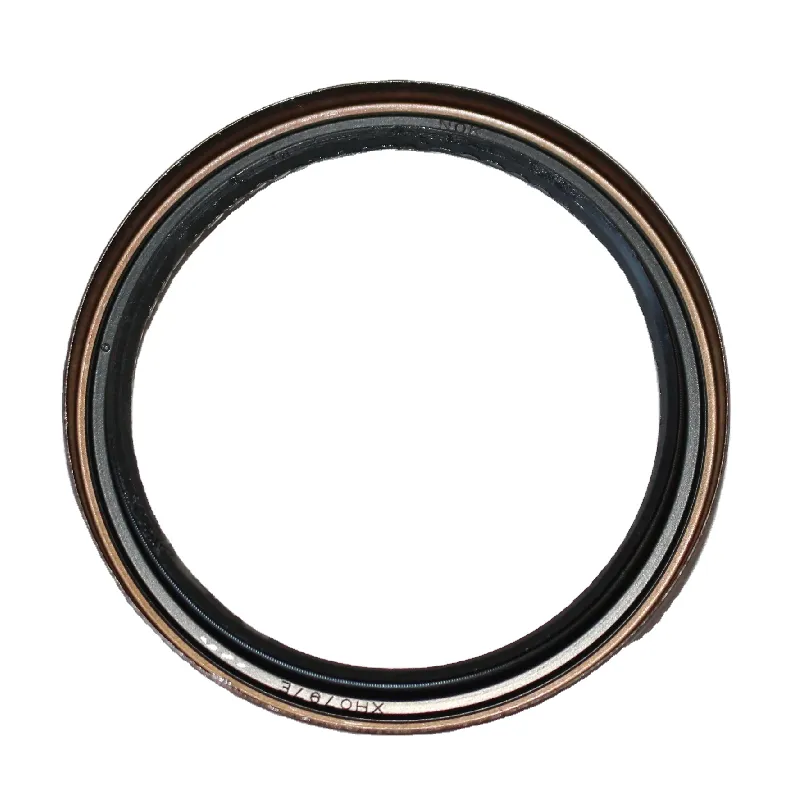
Trustworthiness in the oil seal industry is paramount, as the failure of these components can lead to costly downtimes and catastrophic machinery failures. Reputable manufacturers provide guarantees on their products, backed by rigorous testing processes that simulate real-world conditions. The commitment to quality is further underscored by feedback mechanisms that enable continuous improvement. Customers who procure oil seals from reputable manufacturers often receive detailed information regarding installation, maintenance, and optimal usage to ensure seals deliver peak performance throughout their lifecycle.
oil seal manufacturers
One of the critical aspects that prospective buyers should consider is the level of customization and flexibility a manufacturer offers. The best manufacturers are those who are not just suppliers, but partners in creating solutions that enhance the operational efficiency of machinery. Their product lines often include standard seals as well as specialized variants that accommodate high-pressure environments or corrosive substances, proving their capability and foresight in addressing future industry challenges.
Furthermore, the digital presence of oil seal manufacturers cannot be overlooked. As primary information sources, their websites should offer a wealth of knowledge, including detailed product specifications, technical resources, success stories, and customer testimonials. This is critical in a market where decision-makers rely heavily on the credibility and depth of information available online to make informed purchasing decisions. Therefore, leading manufacturers invest in optimizing their online platforms to ensure they are not only reaching global audiences but also providing valuable insights that assert their expertise and reliability.
In conclusion,
selecting the right oil seal manufacturer involves more than just comparing prices. Companies that excel deliver a harmonious blend of innovative technology, customization, rigorous quality assurance, and educational resources. By choosing such partners, businesses are sure to secure not only high-performing oil seals but also the peace of mind that their machinery will run smoothly and efficiently.