Navigating the realm of industrial components, you'll frequently encounter the term oil seal cap. This essential yet often overlooked component plays a vital role in ensuring machinery operates smoothly, guarding against the debilitating effects of leaks and contamination. My personal journey with oil seal caps began several years ago when I managed a team tasked with maintaining heavy machinery in a textile manufacturing plant. Over time, I have come to appreciate both the intricacies and the immense value of these components.
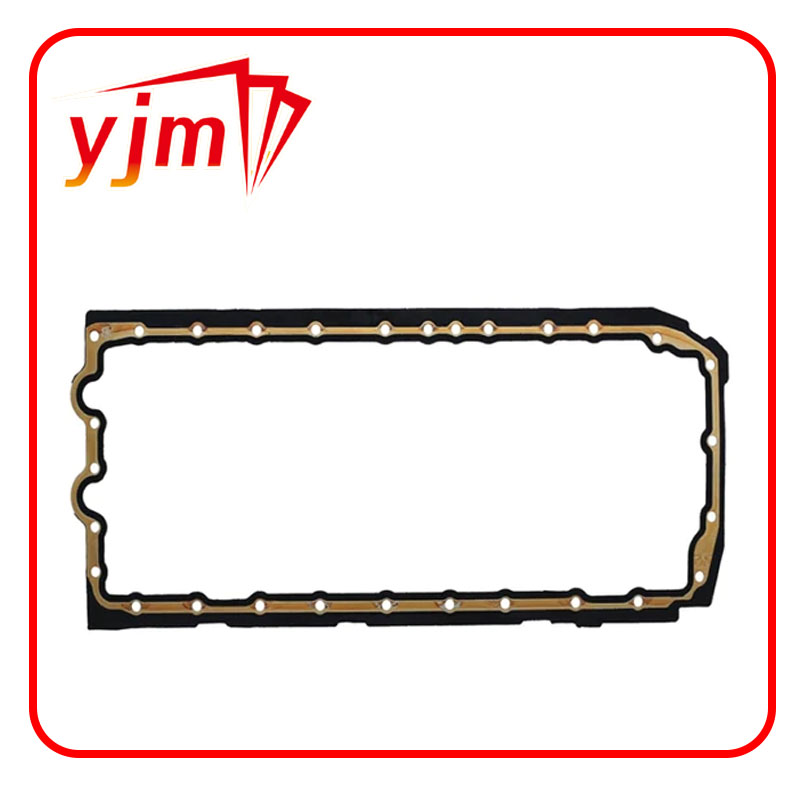
Oil seal caps, often referred to as just seal caps, are specifically designed to prevent leaks from a shaft or a bore in rotating machinery. They serve as a barrier retaining lubricants while keeping out harmful contaminants such as dirt and dust. In my experience, choosing the appropriate oil seal cap significantly enhances the operational efficiency of equipment, prolongs machinery life, and reduces maintenance costs—a trifecta of benefits that are critical to any industrial operation's bottom line.
Understanding the design and material choice of oil seal caps is paramount. They are generally crafted from high-performance materials like nitrile rubber, fluoroelastomer, and silicone, each offering unique advantages. My expertise in material science allowed me to counsel my team effectively on which material to select, based on the operational environment. For instance, fluoroelastomer is particularly suited for high-temperature applications, a choice I opted for in our machinery that operated at elevated temperatures, achieving noticeably improved durability and performance.
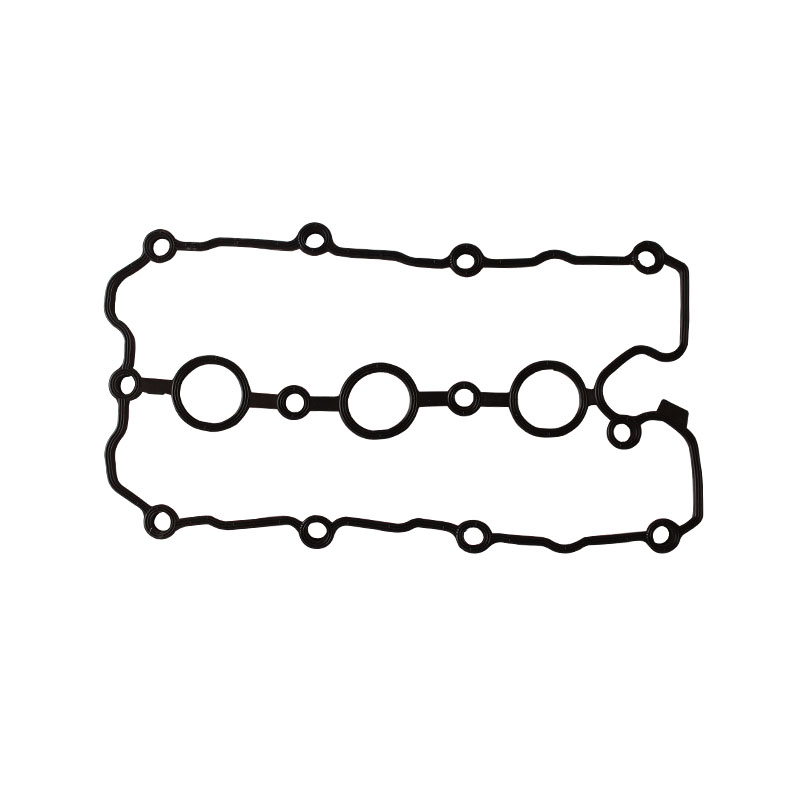
oil seal cap
Moreover, the intricacies involved in the installation of oil seal caps require expertise to avoid undue wear or premature failure. An improperly installed seal cap can lead to detrimental leaks, risking substantial downtime and costly repairs. My authoritative stance on installation processes has been developed through years of hands-on experience and research, which I consistently share with my colleagues and industry peers in various forums and workshops. Trust in the correct installation and maintenance procedures cannot be overstated and is a message I advocate for strongly.
The choice to partner with reputable manufacturers cannot be neglected when prioritizing quality and reliability in oil seal caps. Manufacturers who comply with international standards like ISO and provide thorough testing documentation offer an assurance of trustworthiness. I insist on sourcing from such manufacturers, offering peace of mind that the components will perform as expected under the challenging conditions of industrial applications. My investment in collaborating with certified suppliers reflects my commitment to fostering an atmosphere of dependability and excellence.
In conclusion, the oil seal cap—while seemingly simple—is a cornerstone component in ensuring the functional success of machinery.
Its unassuming stature belies its crucial function in industrial operations. As I continue to share my professional insights and experiential knowledge, my goal remains to illuminate the significance of selecting, installing, and maintaining oil seal caps appropriately. Robust machinery performance, increased lifespan, and reduced operational costs are achievable outcomes readily within reach, provided the right approach is taken towards these essential components.