Oil seals, often referred to as radial lip seals, play a critical role in machinery and equipment by keeping lubricants in and contaminants out, ensuring seamless operations. The specific oil seal variant, denoted as oil seal 20 40 7, indicates particular measurements and specifications that cater to unique operational needs.
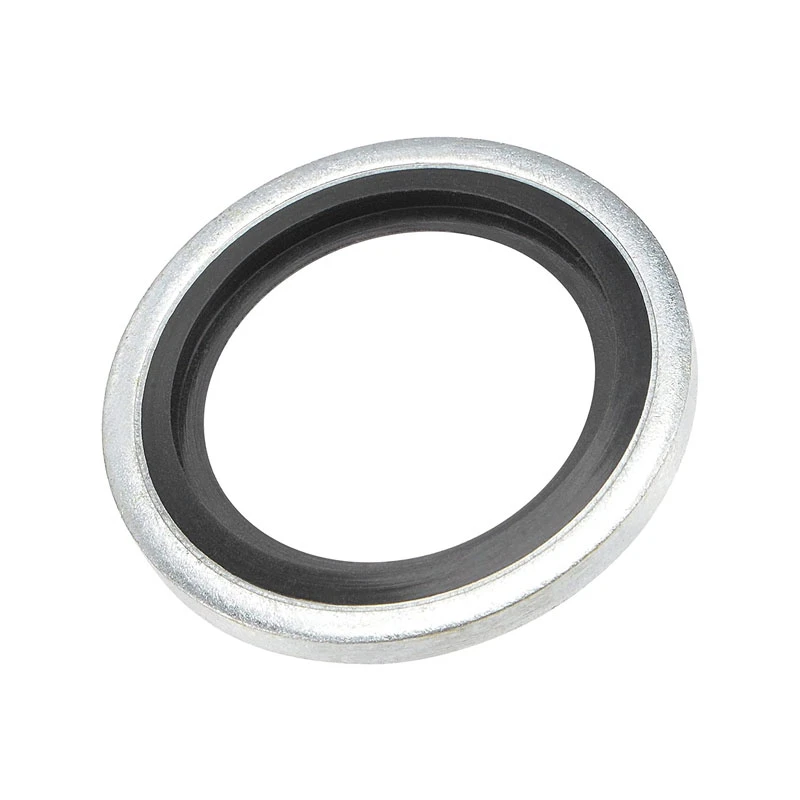
An oil seal with dimensions 20x40x7 is designed for specific industrial purposes, where each number signifies the seal's key measurements. The 20 denotes the inner diameter in millimeters, fitting snugly on the shaft to prevent oil from leaking out. The 40 refers to the outer diameter, which interacts with the housing or bore where the mechanized part is placed. Lastly, the 7 represents the thickness or width of the seal, critical for its durability and capability to handle pressure variations.
The exceptional engineering of the oil seal 20 40 7 showcases its specialization for applications requiring precision and reliability. This particular seal is often used in machinery where space-saving and efficiency take precedence. Its compact design allows it to fit snugly into compact spaces while maintaining its high performance under pressure.
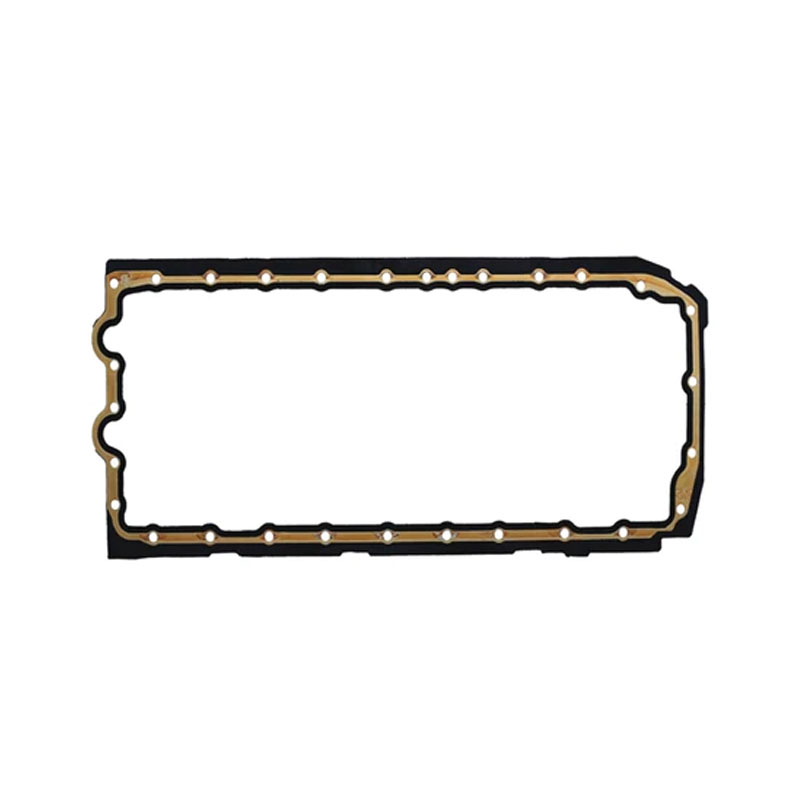
From an expertise perspective, the seal’s structure is a testament to advanced material science and engineering. Typically crafted from high-quality elastomers or polytetrafluoroethylene (PTFE), these materials ensure the seal withstands extreme temperatures and exposure to oils and other chemicals. Some variants may incorporate additional components such as garter springs, which apply uniform pressure on the seal lip, enhancing its effectiveness in relentless environments.
oil seal 20 40 7
Professionals often regard oil seals as silent custodians of machinery's longevity. They play a pivotal role in reducing metal-on-metal contact, a primary cause of wear and tear. By effectively sealing the lubricants within the machinery, they ensure that the moving components glide smoothly past each other, minimizing friction and consequently, energy consumption. This results in significant cost savings over time, as well-lubricated machinery tends to consume less energy, resulting in lower operational costs.
In terms of trustworthiness, procuring oil seals from reputable manufacturers or suppliers is crucial. Renowned brands rigorously test their seals for performance metrics such as pressure thresholds, temperature resistance, and longevity. Look for certifications or compliance with international standards like ISO 6194, which specifically addresses rotary shaft lip seals, ensuring they meet or exceed performance criteria.
When it comes to installation,
expertise plays a vital role. A poorly installed seal might lead to premature failures, leakages, or even complete machinery breakdowns. It is essential to adhere to the manufacturer’s guidelines, ensuring the shaft's surface is smooth and devoid of any nicks or burrs that could damage the seal. Additionally, the appliance of the correct pressure when placing the seal, possibly using a seal fitting tool, ensures even contact with the shaft and bore.
In essence, the oil seal 20 40 7 is more than just a component; it's a critical player in maintaining operational efficiency and extending machinery life. By choosing a reliable product and ensuring proper installation, industries can harness the full potential of their equipment, reducing downtime and maintenance costs. Ultimately, this oil seal dimensions convey a specification increasingly vital in industries where space efficiency and precision mechanics are the order of the day. These seals are indispensable for engineers and maintenance professionals dedicated to optimizing mechanical performance and achieving operational excellence.