Choosing the right oil seal can make a significant difference in the efficiency and longevity of machinery. In this context, the oil seal with dimensions 160x190x15 presents itself as a unique component tailored for specific industrial applications, offering superior performance due to its precise engineering. For anyone involved in machinery maintenance or manufacturing, understanding the nuances of such a seal is imperative. Here is a comprehensive exploration of its features, uses, and benefits
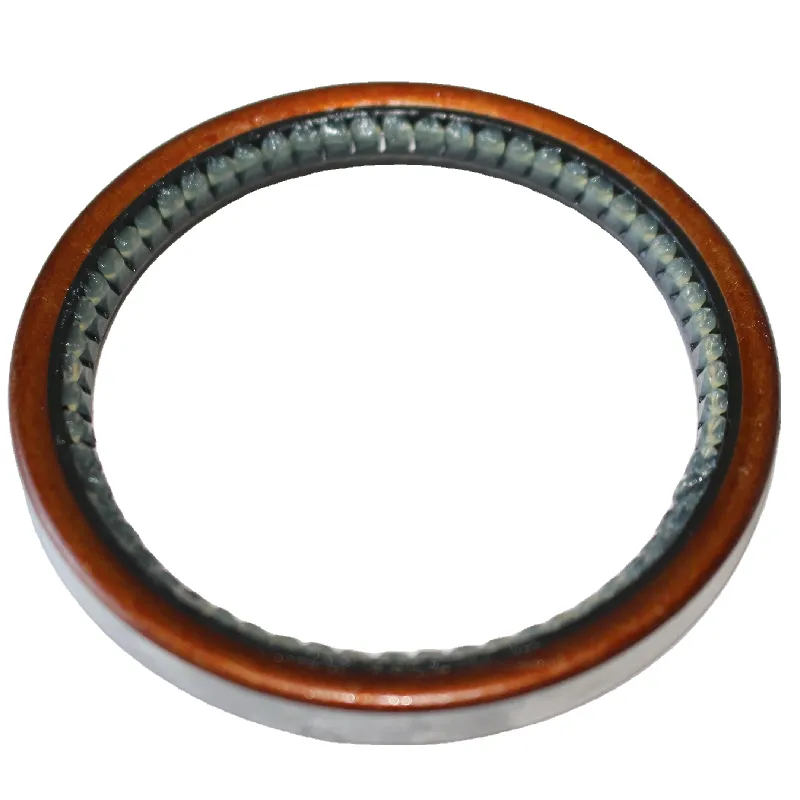
The 160x190x15 oil seal is meticulously designed to fit various industrial machines. Its dimensions—160mm inner diameter, 190mm outer diameter, and a 15mm width—indicate suitability for specific shafts, helping to prevent lubricant leakage while keeping contaminants out. In heavy machinery, where operational efficiency is paramount, such precision in seal size ensures optimal performance by minimizing friction and wear on rotating parts.
From an expertise standpoint, oil seals serve as crucial components in hydraulic and pneumatic systems. The 160x190x15 oil seal is commonly constructed from nitrile rubber, which is acclaimed for its resilience to a wide range of temperatures and resistance against oil, fuel, and other chemicals. This material choice is instrumental in providing a long service life and maintaining the stability of mechanical operations in challenging environments. Alternatively, materials like fluorocarbon or silicone may be selected for environments where extreme temperatures or unique chemical exposures are present.
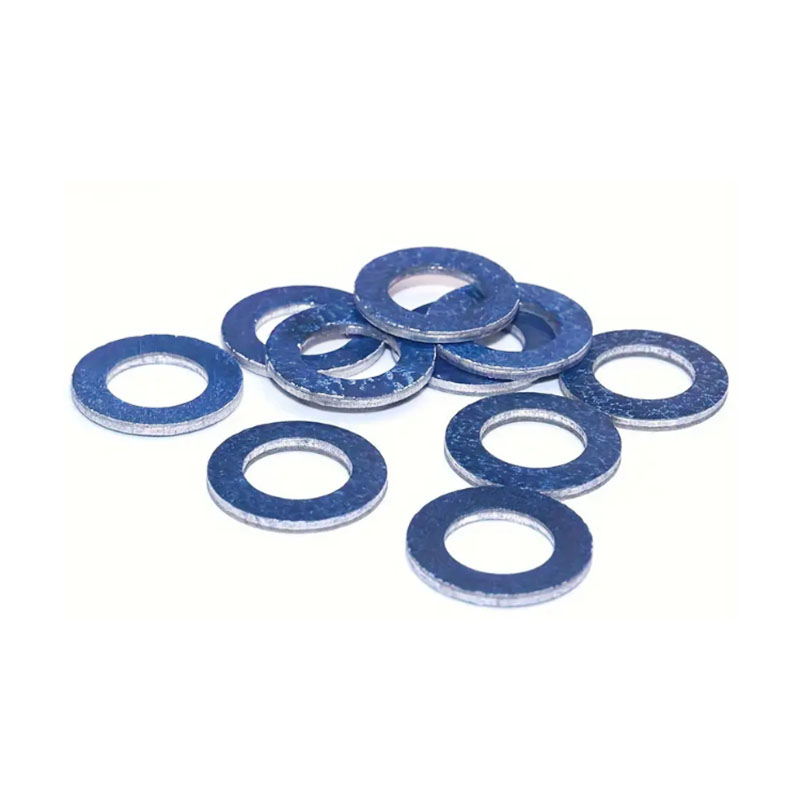
In terms of authoritativeness, engineering professionals advocate for the use of appropriately sized seals such as the 160x190x15 in real-time applications that demand reliability and reduced maintenance. This seal can be integral in automotive applications, heavy equipment, machine tools, and even aerospace technology. The engineers and technicians who have employed these seals report improved machinery uptime and a reduction in unscheduled maintenance, underscoring the importance of precision and quality in seal selection.
oil seal 160x190x15
For the user experience,
the installation of a 160x190x15 oil seal offers significant benefits. When fitted correctly, it ensures optimal lubrication of moving parts, reducing the need for frequent maintenance interventions. The seal helps maintain the integrity of the lubricant, resulting in smoother operational processes and thereby enhancing the life of the machinery. This means that the cost of ownership is reduced over time, which is a compelling factor for procurement and operations professionals.
Trustworthiness in product selection frequently ties back to manufacturer credentials and product reviews. Suppliers who provide this specific dimension often back their products with certifications that affirm quality manufacturing standards, such as ISO 9001. As such, sourcing the 160x190x15 oil seal from reputable vendors is crucial. Reading case studies or testimonials from other industries about their successful implementation can provide additional assurance regarding the seal’s performance.
Moreover, interacting with detailed product documentation and guides ensures users understand the correct handling techniques and installation procedures, which is vital in maintaining the reliability of the seal. Correct installation avoids premature wear or failure, thus emphasizing the importance of following expert guidelines and using the recommended tools and ancillary products like lubricants and sealants designed for the specific material of the seal.
In conclusion, the 160x190x15 oil seal is not merely a component but a key element that contributes to the seamless function of numerous industrial machines. By aligning with best practices in selection, installation, and maintenance, users can ensure that this seal supports their machinery’s peak performance, justifying its role not only as a purchase but as an investment in operational excellence. These insights and expertise highlight the need for thoughtful consideration when selecting such an oil seal, ensuring it meets the stringent demands of modern industrial applications.