Oil seal washers are an often overlooked but essential component across various industries, prominently utilized in automotive and machinery applications. Their critical function is to prevent the leakage of lubricants and contaminants in mechanical systems, ensuring operational efficiency and prolonging the equipment's lifespan. Understanding the nuances of selecting the right oil seal washer can have substantial impacts on industrial output and machinery longevity.
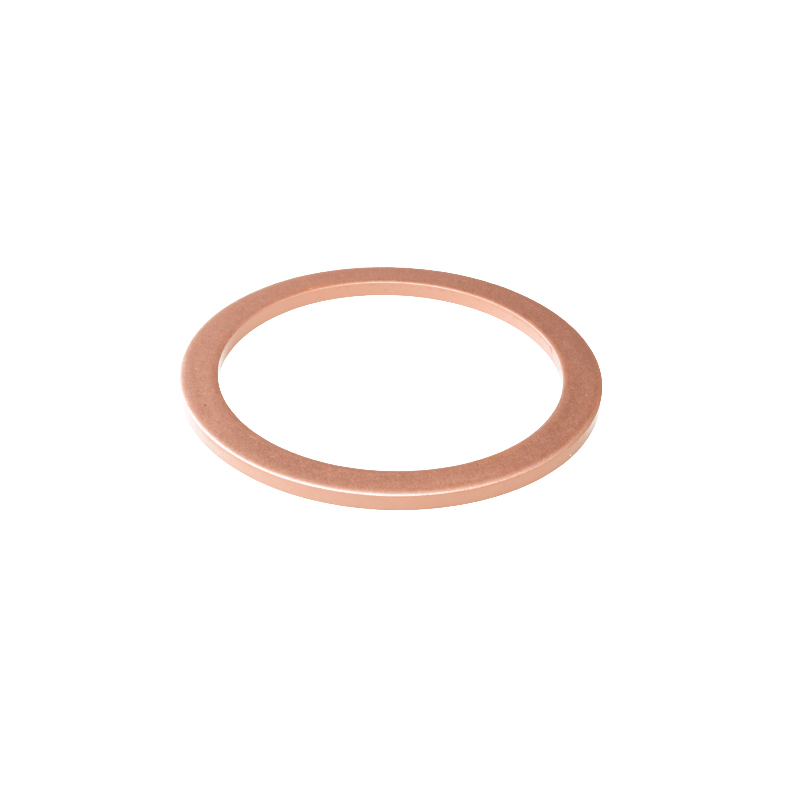
When choosing an oil seal washer, a primary consideration is the operational environment. Factors such as temperature extremes, pressure levels, and the nature of the fluid being sealed must be meticulously evaluated. For example, in automotive applications where temperatures can fluctuate significantly, selecting a washer made from materials like fluorocarbon can provide excellent thermal resistance, enhancing performance and reliability.
Materials matter immensely when it comes to oil seal washers. Rubber, polyurethane, and Teflon are among the various materials employed, each possessing distinct properties suitable for specific applications. Nitrile rubber, for example, offers robust resistance to petroleum-based fluids, making it a common choice in automotive applications, whereas silicone may be preferred for high-temperature applications due to its superior heat resistance.
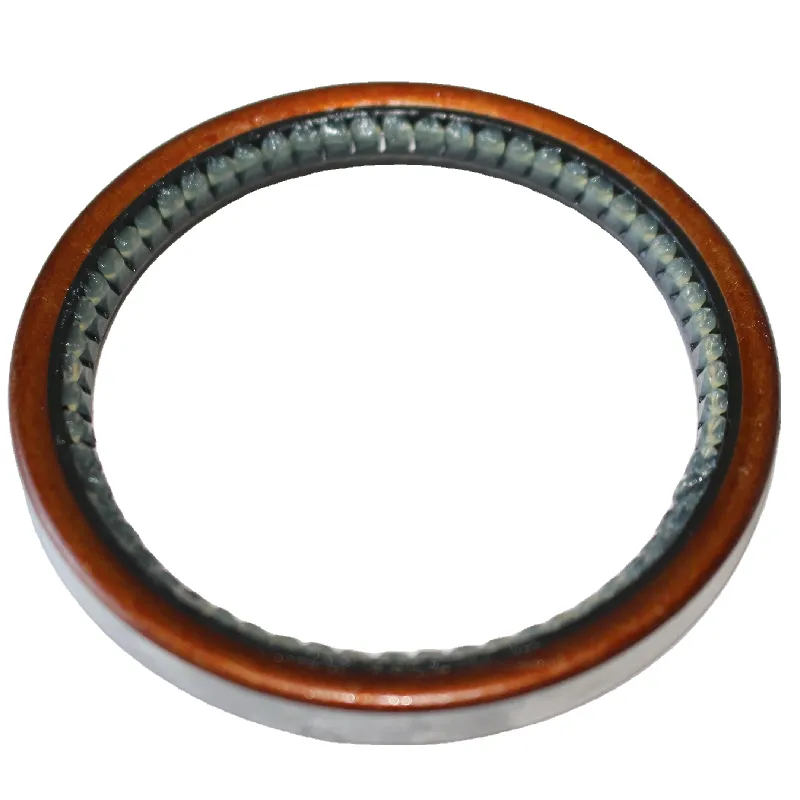
The engineering design of oil seal washers also plays a critical role in their effectiveness. The washer’s design must accommodate specific shaft speeds and pressures to effectively prevent leaks. Engineers must consider the lip design and the spring mechanism, ensuring these elements harmonize to maintain a firm seal under dynamic operating conditions.
oil seal washer
Moreover, the installation process of oil seal washers demands precision. Incorrect installation can lead to premature failure and inefficacy in sealing,
causing downtime and increasing maintenance costs. It's essential to ensure the sealing surface is clean and free from debris before installation, and the washer should be evenly seated to maintain its integrity over time.
In the context of maintenance and replacement, regular inspection is vital. Identifying wear and tear early can prevent costly repairs and system failures. Look for signs of cracking, hardening, or excessive wear. Regular maintenance schedules should include checks for these signs, ensuring the washer continues to function optimally.
Oil seal washers are indispensable in sealing solutions, playing a pivotal role in safeguarding machinery and systems against leaks and contamination. For industry professionals, keeping abreast of the latest advancements in materials and seal technologies can significantly enhance system performance and operational reliability, embodying the essence of Expertise, Authoritativeness, and Trustworthiness.
Adopting a rigorous approach to understanding and implementing oil seal washers not only mitigates risk but also reinforces the credibility of manufacturing and mechanical processes. By investing in high-quality materials and ensuring proper installation and maintenance, industries can yield substantial savings and bolster machinery efficiency, underscoring a commitment to excellence and innovative engineering solutions.