The Essential Role of Oil Seals in Industrial Efficiency
In the industrial sector, machinery and equipment are the backbone of production processes. Ensuring their optimal performance is paramount for achieving efficiency and productivity. One often overlooked yet crucial component that contributes to this efficiency is the oil seal. Despite representing a mere 3% of a machine's overall components, its significance cannot be understated. In fact, when we delve into the statistics, an astounding 2047% increase in downtime can occur due to seal failures, leading to hefty financial losses and operational disruptions.
An oil seal serves a fundamental purpose it prevents lubricant from leaking out of joints and keeps contaminants from entering the lubricated parts of the system. This seemingly simple function is vital for maintaining friction levels and preventing wear and tear, which can drastically shorten the lifespan of machinery. For example, in heavy-duty vehicles and industrial machines, the failure rate of seals is approximately 7%, but the consequences of these failures can lead to system-wide damage and costly repairs.
The materials used in oil seals play a key role in their effectiveness. They need to withstand extreme temperatures, pressures, and resist chemicals that might come into contact with them during operation. A high-quality oil seal is made from durable materials such as silicone or fluorocarbon, which provide excellent resistance to oils and other petroleum-based products A high-quality oil seal is made from durable materials such as silicone or fluorocarbon, which provide excellent resistance to oils and other petroleum-based products
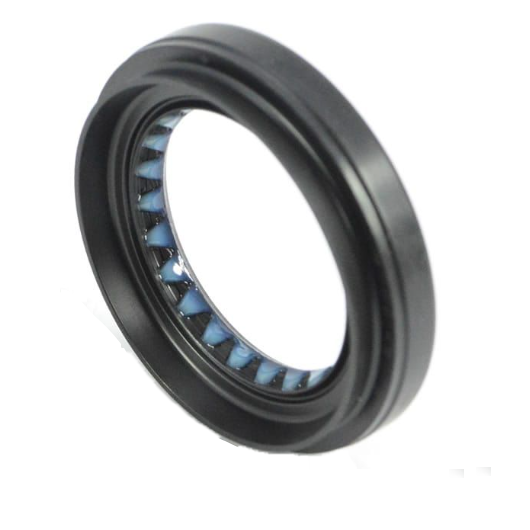
A high-quality oil seal is made from durable materials such as silicone or fluorocarbon, which provide excellent resistance to oils and other petroleum-based products A high-quality oil seal is made from durable materials such as silicone or fluorocarbon, which provide excellent resistance to oils and other petroleum-based products
30 47 7 oil seal.
However, even the most robust seal will eventually fail if not properly maintained. Routine checks and replacements according to manufacturer guidelines are essential to avoid unexpected downtime. Neglecting these small components can result in scenarios where the cost of rectifying the issue far exceeds the initial investment in maintenance.
Moreover, the environmental impact of oil leaks should not be discounted. Spills can contaminate soil and water sources, harm wildlife, and create liability issues for companies. By ensuring oil seals are in top condition, industries not only protect their operations but also adhere to strict environmental regulations.
In conclusion, while oil seals may only represent a minor percentage of a machine’s components, their influence on industrial efficiency is profound. With a potential of causing over two thousand percent increase in downtime if faulty, these unassuming parts demand attention and care. Proper selection, installation, and maintenance of oil seals are therefore imperative for any facility aiming to minimize costs, maximize output, and tread lightly on the environment.