The Significance of Oil Seal 50, 70, and 10 in Industrial Applications
In the realm of industrial machinery and engineering, oil seals play an indispensable role in ensuring optimal performance and longevity. The terms oil seal 50, oil seal 70, and oil seal 10 refer to specific types or sizes of these essential components, each with its unique characteristics and applications.
An oil seal, fundamentally, is a device designed to prevent the leakage of lubricants or fluids while preventing the ingress of contaminants into a mechanical system. It is a crucial element in various industries, including automotive, aerospace, and manufacturing, where maintaining a clean and lubricated environment is paramount.
The 'oil seal 50' typically denotes a seal with an inner diameter of 50 millimeters. This size is commonly used in medium-sized machinery, such as pumps and gearboxes, where it ensures a tight barrier against oil leaks and external debris. Its design and materials, often a combination of rubber and steel, provide flexibility and durability necessary for withstanding harsh operating conditions.
Moving on to 'oil seal 70', this refers to a seal with an inner diameter of 70 millimeters. Slightly larger than the 50, it is employed in more substantial equipment, such as heavy-duty engines or hydraulic systems. These seals are engineered to withstand high pressure and temperature fluctuations, providing reliable sealing solutions in demanding industrial environments.
Lastly, the 'oil seal 10' indicates a smaller size, with an inner diameter of 10 millimeters
Lastly, the 'oil seal 10' indicates a smaller size, with an inner diameter of 10 millimeters
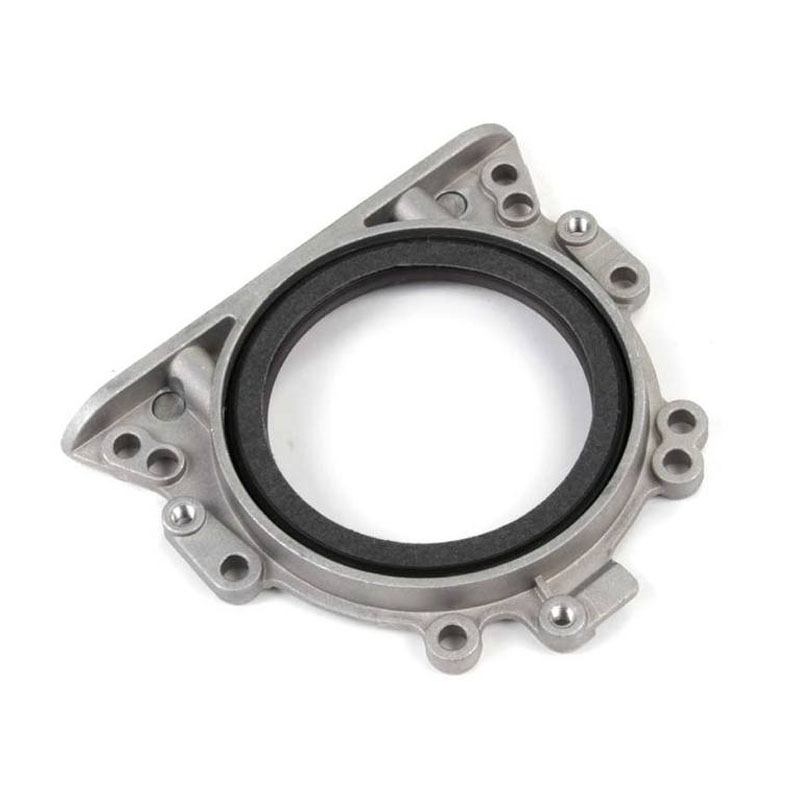
Lastly, the 'oil seal 10' indicates a smaller size, with an inner diameter of 10 millimeters
Lastly, the 'oil seal 10' indicates a smaller size, with an inner diameter of 10 millimeters
oil seal 50 70 10. This miniature version is commonly used in compact machinery or precision instruments where space is limited but leak prevention is still critical. Despite its small size, it delivers robust sealing performance, preventing fluid loss and contamination ingress effectively.
Each of these oil seals, 50, 70, and 10, serves a distinctive purpose based on the specific requirements of the machinery they are designed for. Their effectiveness lies not only in their ability to seal but also in their resistance to wear, heat, and chemical exposure. They contribute significantly to enhancing the efficiency, safety, and overall lifespan of the equipment they are installed in.
In conclusion, understanding the nuances of different oil seals like 50, 70, and 10 is vital for engineers and technicians in selecting the right seal for a given application. The right choice can make all the difference in maintaining peak operational efficiency, minimizing downtime, and ensuring a safe and clean working environment. Therefore, oil seals, regardless of their size, are a testament to the importance of detail in industrial engineering.